
Illuminate your space with the brilliance of LED lights! These energy-efficient lighting fixtures have revolutionized the way we brighten our homes. However, installing them can seem daunting, particularly for those who are unfamiliar with electrical work. But fret not! With our comprehensive guide, you’ll discover the secrets to putting up LED lights like a pro, ensuring your space radiates with light and style.
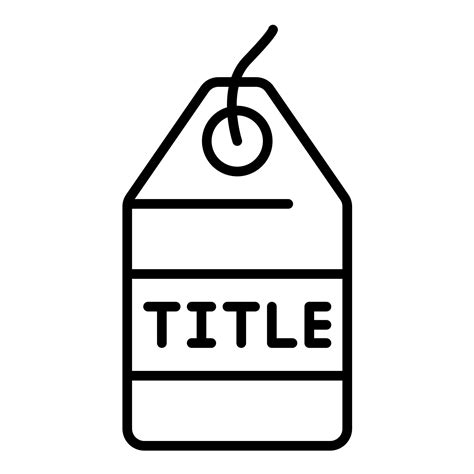
Before embarking on your LED lighting journey, gather your essential tools. You’ll need a pair of wire strippers, a voltage tester, and a screwdriver. Don’t forget to turn off the power at the main circuit breaker for safety. Now that you’re armed and ready, let’s delve into the installation process. First, identify the location for your LED lights, ensuring they are evenly spaced and positioned for optimal illumination.
Next, connect the wires. LED lights typically have two wires, a positive wire and a negative wire. Match the positive wire of the LED light to the positive wire of the power source, and the negative wire of the LED light to the negative wire of the power source. Securely fasten the wires using wire nuts, ensuring the connections are tight and insulated. Finally, turn on the power at the main circuit breaker and marvel at the radiant glow of your newly installed LED lights. Bask in the ambiance they create, knowing you have successfully completed this illuminating project.
Planning the Layout
Before installing your LED lights, it’s essential to plan the layout carefully. This will help ensure that you create the desired ambiance and functionality for your space. Here are some key considerations:
1. Purpose and Ambiance
Determine the primary purpose of the lighting, whether it’s for task lighting (e.g., in a kitchen or workspace), ambient lighting (e.g., for general illumination in a living room), or accent lighting (e.g., to highlight artwork or architectural features). Different purposes require varying light intensity, color temperature, and placement. Consider the mood you want to create: warm and cozy, bright and energizing, or something in between.
2. Fixture Selection
Choose LED light fixtures that align with the style and functionality of your space. For example, recessed lights are ideal for a clean, modern look and provide even illumination. Pendant lights can create a more decorative touch and are great for spotlighting specific areas. Under-cabinet lights are perfect for task lighting in kitchens and work areas.
3. Placement and Spacing
The placement and spacing of your LED lights will affect the overall lighting效果. For ambient lighting, distribute the fixtures evenly throughout the space to create a uniform glow. For task lighting, focus the lights directly on the work surfaces. Accent lighting can be used to highlight specific features by positioning the fixtures strategically.
Type of Lighting |
Purpose |
Recommended Placement |
Ambient |
General illumination |
Evenly distributed throughout space |
Task |
Illuminating work surfaces |
Directly over or near work areas |
Accent |
Highlighting specific features |
Strategically placed to draw attention to focal points |
Selecting the Right Bulbs and Strips
Choosing the Right Bulbs
Selecting the appropriate LED bulbs depends on several factors. First, consider the size of the bulb base, which should match the existing fixture. The shape of the bulb, such as A19, BR30, or GU10, determines its compatibility with specific fixtures and applications.
The brightness of LED bulbs is measured in lumens. For general lighting, aim for 800-1000 lumens per 60W equivalent bulb. For task lighting or accent lighting, opt for 400-800 lumens.
Color temperature refers to the warmth or coolness of the light emitted. Warm white (2700-3000K) creates a cozy and inviting atmosphere, while cool white (4000-5000K) provides a more energizing and focused light.
Choosing the Right Strips
LED strips, also known as LED ribbons, offer versatile lighting solutions. Their flexibility and self-adhesive backing allow for easy installation in various applications.
Factors to Consider When Choosing LED Strips
Strip Length: Determine the desired length of the strip based on the area to be illuminated.
LED Density: The number of LEDs per meter affects the brightness and uniformity of the light. Higher density strips produce brighter and more continuous illumination.
Color Temperature: Similar to bulbs, LED strips offer a range of color temperatures to suit different ambiance preferences.
Adhesive Strength: Consider the strength of the adhesive backing to ensure the strips remain securely attached to the installation surface.
IP Rating: The IP rating indicates the protection level of the strip against moisture and dust ingress. Indoor strips typically require an IP20 rating, while outdoor or bathroom applications may necessitate a higher IP rating.
Factor |
Considerations |
Strip Length |
Determined by the area to be illuminated |
LED Density |
Higher density for brighter and more continuous illumination |
Color Temperature |
Select based on ambiance preference, from warm white to cool white |
Adhesive Strength |
Ensure strong adhesion to the installation surface |
IP Rating |
Select based on environmental conditions, such as moisture or dust exposure |
Measuring and Cutting the Strips
Before you begin, you’ll need to measure the area where you want to install the LED strips. Measure the length of the area, rounding up to the nearest inch. This will be the length of the LED strip you need to purchase.
Next, you’ll need to cut the LED strips to the desired length. LED strips are typically sold in rolls of 5 meters (16.4 feet). If you need a shorter length, you can cut the strip with a pair of scissors. Be sure to cut the strip between the copper pads, as cutting through the pads will damage the strip.
Once you have measured and cut the LED strips, you’re ready to start installing them.
Tips for measuring and cutting LED strips:
Tip |
Use a ruler or measuring tape to get an accurate measurement. |
Round up the measurement to the nearest inch. |
Cut the strip between the copper pads. |
Be careful not to cut the strip too short. |
Mounting the Strips
Once you’ve planned your layout and cut the strips to the proper length, it’s time to mount them. LED light strips come with an adhesive backing, making installation a breeze. Here’s how:
-
Clean the Mounting Surface
Wipe down the surface where you’ll be mounting the strips with a cloth and rubbing alcohol. This will remove any dirt or debris that could prevent the strips from adhering properly.
-
Remove the Backing
Peel off the paper backing from one end of the LED strip. Be careful not to touch the adhesive with your fingers, as this could weaken its bond.
-
Position the Strip
Starting at one end, slowly press the LED strip onto the mounting surface. Use your fingers to smooth out any wrinkles or bubbles.
-
Secure the Strip
Once the strip is in place, press firmly along its entire length to ensure it adheres securely. You can use a rolling pin or a flat-edged object to apply even pressure.
Mounting Options |
Pros |
Cons |
Adhesive Backing |
Easy to use, no drilling required |
May not be suitable for all surfaces |
Mounting Clips |
More secure than adhesive backing, can be used on irregular surfaces |
Requires drilling or nailing |
Magnetic Tape |
Easy to remove and reposition, can be used on metal surfaces |
May not be strong enough for heavy strips |
Connecting the Lights
Connecting LED lights involves carefully following instructions and ensuring proper electrical connections to avoid any potential hazards. Here’s a detailed guide on how to connect LED lights:
1. Plan the Layout
Determine the desired lighting arrangement and measure the areas where the lights will be installed. Mark the locations for power outlets, switches, and wire runs.
2. Prepare the Wires
Cut the electrical wires to the appropriate lengths and ensure they are rated for the power consumption of the LED lights. Strip the insulation from the ends of the wires to expose the copper conductors.
3. Connect the Power Supply
Connect the power supply to the electrical outlet. This provides the necessary voltage and current to power the LED lights.
4. Connect the Controller (Optional)
If using a controller for dimming or color changing, connect it to the power supply and the LED lights. Follow the manufacturer’s instructions for wiring.
5. Wire the LED Lights
This is the most crucial step in connecting LED lights. Ensure the lights are connected in series or parallel, depending on the desired effect and power requirements.
Series Connection:
- Connect the positive terminal of one light to the negative terminal of the next.
- Repeat the process until all lights are daisy-chained together.
Parallel Connection:
- Connect the positive terminals of all lights to the positive terminal of the power supply.
- Similarly, connect the negative terminals of all lights to the negative terminal of the power supply.
Connection Type |
Advantages |
Disadvantages |
Series |
Easier wiring |
Reduced brightness if one light fails |
Parallel |
Independent lighting |
More complex wiring |
6. Secure the Connections
Use electrical tape or wire connectors to secure the wire connections and prevent any loose contacts or potential electrical hazards.
7. Test the Lights
Turn on the power supply and check if the LED lights are functioning correctly. If there are any issues, re-check the connections and ensure everything is wired properly.
Powering Up the Lights
Once your LED lights are assembled and ready to go, it’s time to give them some juice. Here’s how to do it:
1. Choose a Power Source
LED lights typically require a power supply that provides a specific voltage and amperage. Determine the power source that is compatible with your lights by checking the packaging or documentation.
2. Connect the Power Supply
Connect the power supply to an appropriate power outlet. Ensure that the outlet is compatible with the voltage and amperage of your power supply.
3. Connect the Lights to the Power Supply
Use appropriate connectors or cables to connect the LED lights to the power supply. Follow the instructions provided with your lights to ensure proper connection.
4. Check for Loose Connections
After connecting the lights to the power supply, check for any loose connections. Ensure that all connectors are securely fastened and cables are not loose or damaged.
5. Adjust Power Output (Optional)
Some power supplies allow you to adjust the power output. If your lights are too bright or dim, you can adjust the output voltage or amperage to achieve the desired brightness.
6. Troubleshooting: Power Issues
If you encounter any power issues with your LED lights, consider the following troubleshooting steps:
Issue |
Solution |
Lights don’t turn on |
Check power connections, power supply voltage/amperage, and loose wires |
Lights are flickering |
Ensure stable power supply, check for loose connections, or voltage irregularities |
Lights are dimming |
Check power supply capacity, voltage drop in the circuit, or loose connections |
Power supply is overheating |
Increase ventilation, ensure adequate power supply capacity, and check for overloaded circuits |
Lights are damaged |
Inspect lights for physical damage, electrical shorts, or blown LEDs |
Troubleshooting Common Issues
1. LED Lights Not Turning On
Check if the power switch is on. Ensure the power supply is properly connected and the LED lights are securely plugged in. If necessary, use a multimeter to test the voltage at the power supply and the LED lights.
2. LED Lights Flickering
Loose connections, faulty wiring, or an unstable power supply can cause flickering. Tighten all connections, inspect the wiring for any damage, and ensure the power supply voltage is within the specified range.
3. LED Lights Dimming or Brightening
Voltage fluctuations, dimmer compatibility issues, or aging LED components can lead to dimming or brightening. Check the power supply voltage, ensure the dimmer is compatible with LED lights, and consider replacing the LED lights if they are old.
4. LED Lights Overheating
Excessive operating temperature can reduce the lifespan of LED lights. Ensure proper heat dissipation by providing adequate ventilation and avoiding installation in enclosed spaces. Use heat sinks or aluminum profiles to improve heat transfer.
5. LED Lights Turning Yellow or Blue
LEDs gradually degrade over time, leading to color shifts. Poor-quality LEDs or extreme operating conditions can accelerate this process. Consider using high-quality LEDs with a long lifespan and maintaining the recommended operating conditions.
6. LED Lights Not Connecting to Wi-Fi
Make sure your router is broadcasting the correct Wi-Fi network name and password. Check the range of your Wi-Fi signal and move the LED lights closer to the router if necessary. Ensure the LED lights have the latest firmware update and follow the manufacturer’s instructions for pairing.
7. LED Lights Malfunctioning After Power Outage
Power outages can sometimes cause damage to LED lights, especially if the voltage surges or drops excessively during the outage. Check the LED lights for any physical damage and replace them if necessary. Consider using a surge protector or voltage regulator to protect the LED lights from voltage fluctuations.
Use LED Strip Lights
LED strip lights are a great way to add ambient lighting to any room. They are flexible and can be cut to any length, making them perfect for a variety of applications. LED strip lights are also very energy-efficient, so you can save money on your electric bill.
Mount LED Lights on a Wall
Mounting LED lights on a wall is a great way to create a dramatic and stylish effect. You can use LED light strips to create a backlighting effect behind a piece of furniture or artwork, or you can use LED spotlights to highlight a particular area of the room.
Hang LED Lights from the Ceiling
Hanging LED lights from the ceiling is a great way to create ambient lighting in a room. You can use LED pendants to create a soft, diffused light, or you can use LED chandeliers to create a more dramatic effect.
Use LED Lights to Create a Focal Point
LED lights can be used to create a focal point in a room. By placing LED lights in a strategic location, you can draw attention to a particular feature of the room, such as a fireplace, a piece of furniture, or a work of art.
Use LED Lights to Highlight Architectural Features
LED lights can be used to highlight architectural features in a room. By placing LED lights in the corners of a room, you can create a sense of depth and drama. You can also use LED lights to highlight beams, columns, and other architectural details.
Use LED Lights to Create a Mood
LED lights can be used to create a specific mood in a room. By choosing the right color and intensity of LED lights, you can create a relaxing, romantic, or energizing atmosphere.
Use LED Lights to Save Energy
LED lights are very energy-efficient, so you can save money on your electric bill by using them. LED lights use up to 80% less energy than traditional incandescent light bulbs, and they last much longer. This means that you can save even more money in the long run.
Experiment with Different Types of LED Lights
There are many different types of LED lights available on the market, so you can experiment to find the ones that best suit your needs. Some of the most popular types of LED lights include:
Type of LED Light |
Description |
LED Strip Lights |
Flexible strips of LED lights that can be cut to any length |
LED Spotlights |
Small, focused LED lights that can be used to highlight specific areas |
LED Pendants |
Hanging LED lights that create a soft, diffused light |
LED Chandeliers |
Larger, more elaborate LED lights that can create a dramatic effect |
Safety Precautions
Mind the Electricity
Always remember that electricity is a potential hazard. Before you start working with LED lights, make sure that the power source is turned off or unplugged.
Proper Use of Ladders
If you need to reach high places to install LED lights, use a sturdy ladder that is tall enough to provide you with safe access. Ensure the ladder is stable and secure before climbing it.
Avoid Touching Live Wires
When connecting or disconnecting LED lights, always double-check that the power is off and avoid touching any exposed wires.
Wear Protective Gear
Wear safety glasses to protect your eyes from any flying debris or particles. If you are working with sharp objects, wear gloves to prevent cuts or punctures.
Be Aware of Your Surroundings
Pay attention to your surroundings and be aware of potential trip hazards or obstacles while working with LED lights.
Take Breaks
Working with LED lights for long periods of time can strain your eyes. Take regular breaks to give your eyes a rest and prevent fatigue.
Use Proper Tools
Use the right tools for the job. Have a toolkit handy with screwdrivers, pliers, and other necessary tools to ensure a safe and efficient installation.
Inspect LED Lights Regularly
Once the LED lights are installed, check them regularly for any loose connections, flickering, or other issues. Promptly address any problems to ensure safety and optimal performance.
Know Your Electrical System
Before working with LED lights, it is crucial to have a basic understanding of your home’s electrical system. If you are not comfortable working with electricity, seek professional assistance to ensure safety.
Enjoying Your Illuminated Display
Once you’ve installed your LED lights, it’s time to enjoy your illuminated display. Here are 10 ways to make the most of your new lighting:
1.
Create a relaxing atmosphere:
Use warm, dim LED lights to create a cozy and inviting ambiance.
2.
Highlight architectural features:
Illuminate the exterior of your home or architectural details, such as columns or archways.
3.
Enhance outdoor living spaces:
Use LED lights to illuminate patios, decks, and gardens, extending your time spent outdoors.
4.
Improve home security:
Motion-activated LED lights can deter intruders and provide peace of mind.
5.
Add a festive touch:
Use LED lights in vibrant colors to create a festive atmosphere for holidays and special occasions.
6.
Uplight trees and shrubs:
Direct LED lights upward to highlight trees and shrubs, adding depth and interest to your landscape.
7.
Create a nightlight effect:
Use low-wattage LED lights to provide soft illumination in hallways, bathrooms, and other areas that need ambient lighting.
8.
Illuminate pathways and driveways:
Provide safe and convenient access to your home with LED lights that illuminate pathways and driveways.
9.
Complement interior décor:
Use LED lights in different colors and intensities to enhance the style and ambiance of your living spaces.
10.
Customize lighting with smart home integration:
Connect your LED lights to a smart home system to control them remotely, adjust brightness, and create custom lighting scenes.
How To Put Up Led Lights
LED lights are a great way to add some extra light to your home or business. They’re energy-efficient, long-lasting, and come in a variety of colors and styles. If you’re thinking about installing LED lights, here are a few tips to help you get started.
First, you’ll need to decide where you want to put your LED lights. Once you’ve decided on a location, you’ll need to gather your materials. You’ll need LED lights, a power source, and some wire.
Once you have your materials, you can start installing your LED lights. First, you’ll need to connect the LED lights to the power source. Once the lights are connected, you can start attaching them to the wall or ceiling. You can use screws, nails, or adhesive to attach the lights.
Once the lights are attached, you’re ready to turn them on and enjoy the extra light. LED lights are a great way to add some extra light to your home or business. They’re energy-efficient, long-lasting, and come in a variety of colors and styles.
People Also Ask
How do you connect LED lights together?
To connect LED lights together, you will need to use a connector. Connectors come in a variety of shapes and sizes, so you will need to choose one that is compatible with your LED lights. Once you have a connector, you can simply insert the LED lights into the connector and twist them to secure them.
Can you cut LED lights?
Yes, you can cut LED lights. However, it is important to note that you can only cut LED lights at designated cutting points. Cutting LED lights at any other point could damage the lights.
How do you install LED lights under cabinets?
To install LED lights under cabinets, you will need to first measure the length of the cabinet. Once you have the measurement, you can cut the LED lights to the desired length. Next, you will need to attach the LED lights to the underside of the cabinet using screws or adhesive. Finally, you can connect the LED lights to a power source and enjoy the extra light.