
Arc welding is an incredibly versatile fabrication technique that allows users to join two pieces of metal together using an electric arc. The process is relatively simple, but it does require some specialized equipment and safety precautions. In this article, we will provide a comprehensive guide on how to use an arc welder, covering everything from safety tips to the step-by-step welding process. Whether you’re a beginner or an experienced welder, this guide will provide you with the knowledge and skills you need to use an arc welder safely and effectively.
Before you begin welding, there are certain safety measures that you need to take. First and foremost, you should always wear a welding helmet to protect your eyes from the intense light of the arc. You should also wear protective clothing, such as gloves and a flame-resistant jacket, to protect your skin from sparks and molten metal. Additionally, you should ensure that your work area is well-ventilated, as welding can produce fumes that can be harmful if inhaled.
Once you have taken the necessary safety precautions, you can begin the welding process. The first step is to clean the metal surfaces that you will be welding together. This will help to ensure a strong weld. Next, you need to set the welding machine to the appropriate settings for the thickness of the metal that you are welding. Once the machine is set up, you can strike an arc by touching the welding electrode to the metal and pulling it away slightly. This will create an electric arc, which will melt the metal and allow you to join the two pieces together. As you weld, you need to move the electrode along the joint, keeping the arc length consistent. Once the weld is complete, you can allow it to cool and then inspect it for any defects.
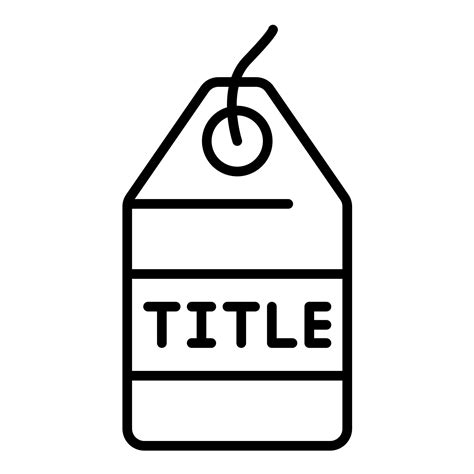
Getting Started with Arc Welding
Arc welding is a highly versatile and widely used metalworking technique that requires a high level of skill and precision. To master arc welding, it’s essential to start with a solid foundation. Here’s a comprehensive guide to get you started with this intricate craft:
Equipment You’ll Need:
Item |
Purpose |
Welding Machine |
Generates the electric current for the welding process |
Electrodes |
Consumables that provide the arc and filler material |
Welding Helmet |
Protects your eyes and face from harmful UV radiation |
Welding Gloves |
Protects your hands from heat and sparks |
Welding Jacket |
Provides protection for your skin and clothing |
Safety Precautions:
Before starting any welding work, it’s imperative to prioritize safety:
- Wear proper protective gear, including a helmet, gloves, jacket, and sturdy shoes.
- Ensure your workspace has adequate ventilation to remove welding fumes.
- Keep flammable materials well away from the welding area.
- Never weld near combustible materials or liquids.
- Always inspect your equipment before use and ensure it’s in good working condition.
Selecting the Right Equipment
Choosing the appropriate arc welding equipment is crucial for a successful welding experience. The following factors should be considered when selecting your gear:
Power Source
The power source is the heart of an arc welding system, providing the electrical current necessary to create the welding arc. There are two main types of power sources:
- Transformer-based machines are more economical and offer stable voltage for consistent welds. They are suitable for most general welding applications.
- Inverter-based machines are more portable and efficient, with better arc control and penetration capabilities. They are ideal for precise welding tasks and working in confined spaces.
Welding Process
The welding process you choose will determine the type of welding machine you need. Here are the most common welding processes:
Process |
Description |
SMAW (Stick Welding) |
Uses a consumable electrode covered in flux that shields the weld from contamination. |
MIG/MAG (Wire Feed Welding) |
Uses a continuously fed wire electrode with a shielding gas, suitable for various materials and thicknesses. |
TIG (Tungsten Inert Gas Welding) |
Uses a non-consumable tungsten electrode and a shielding gas, providing precise and high-quality welds. |
Preparing Your Workspace
Before you start welding, it’s important to prepare your workspace properly. This will help you stay safe and organized, and it will make the welding process much easier.
1. Choose a well-ventilated area
Welding can produce harmful fumes, so it’s important to work in a well-ventilated area. Open windows and doors, or use a fan to circulate the air.
2. Clear away any flammable materials
Welding can create sparks and spatter, so it’s important to clear away any flammable materials from your workspace. This includes paper, cardboard, and gasoline.
3. Wear the proper safety gear
When you’re welding, it’s important to wear the proper safety gear to protect yourself from sparks, fumes, and ultraviolet radiation. This includes:
- A welding helmet with a face shield
- Welding gloves
- A welding apron
- Safety glasses
- Ear protection
- Respirator
Safety Gear |
Purpose |
Welding helmet with a face shield |
Protects your eyes and face from sparks, fumes, and ultraviolet radiation |
Welding gloves |
Protects your hands from heat and sparks |
Welding apron |
Protects your clothes and body from sparks and fumes |
Safety glasses |
Protects your eyes from sparks and flying debris |
Ear protection |
Protects your hearing from the loud noise of welding |
Respirator |
Protects your lungs from harmful fumes |
Setting Up the Arc Welder
Before you start welding, you need to ensure that your arc welder is set up properly. Here are the steps you need to follow:
1. Choose the right location
The location you choose for welding should be well-ventilated to avoid inhaling harmful fumes. It should also be away from any flammable materials that could catch fire.
2. Assemble the welder
If your welder is not already assembled, you will need to follow the manufacturer’s instructions to assemble it. This will typically involve attaching the power cable, the ground clamp, and the welding torch.
3. Connect the welder to power
Once the welder is assembled, you need to connect it to a power source. Make sure that the power source is compatible with the welder’s voltage requirements.
4. Adjust the welder settings
The welder settings will need to be adjusted depending on the type of metal you are welding and the thickness of the metal. Here is a more detailed explanation of each setting:
a. Amperage/Current Setting
Low amperage (less than 100 A) |
High amperage (more than 100 A) |
Thinner metals (less than 1/8 inch) |
Thicker metals (more than 1/8 inch) |
Produces a narrower, more focused arc |
Produces a wider, less focused arc |
Requires less heat input |
Requires more heat input |
Results in less distortion |
Results in more distortion |
b. Voltage Setting
Low voltage (less than 20 V) |
High voltage (more than 20 V) |
Short arc length |
Long arc length |
Produces a more stable arc |
Produces a less stable arc |
Results in less spatter |
Results in more spatter |
Requires more welder skill |
Easier for beginners to use |
Striking the Arc
Striking the arc is the initial step in arc welding, where an electrical circuit is established between the welding electrode and the workpiece. To strike the arc successfully, follow these steps:
-
Position the Electrode: Hold the welding electrode perpendicular to the workpiece surface at a slight angle (10-20 degrees).
-
Touch and Withdraw: Lightly tap the electrode tip against the workpiece and quickly withdraw it. This creates a short circuit and initiates the flow of current.
-
Drag the Electrode: As you withdraw the electrode, slightly drag it along the workpiece surface. This maintains the arc and prevents the electrode from sticking.
-
Adjust the Distance: Maintain a consistent distance (arc length) of 3-6 millimeters between the electrode tip and the workpiece. Too short an arc may result in sticking, while too long an arc can produce porosity.
-
Maintain Arc Stability: To ensure a stable arc, consider the following factors:
Factor |
Effect |
Electrode Diameter |
Larger electrodes produce a more stable arc. |
Welding Current |
Lower currents lead to more stable arcs, but may not provide enough heat for effective welding. |
Arc Length |
A consistent arc length helps control the heat input and penetration. |
Shielding Gas |
Gas shielding protects the weld pool from contamination, improving arc stability. |
Electrode Condition |
Clean electrodes with a fresh coating result in a more stable arc. |
Controlling the Weld Pool
Maintaining a stable weld pool is crucial for successful welding. Here are some techniques to control the weld pool:
Arc Length
The distance between the electrode and the workpiece determines the arc length. A short arc length (1-2 mm) creates a focused and penetrating weld, while a long arc length (3-5 mm) results in a wider and shallower weld.
Travel Speed
The speed at which the electrode moves along the weld joint controls the size and shape of the weld pool. A faster travel speed produces a narrower and deeper weld, while a slower travel speed results in a wider and shallower weld.
Weaving
Weaving the electrode side-to-side across the weld joint helps distribute the heat evenly and reduce the risk of undercut. The width and frequency of the weave can be adjusted to suit the joint geometry and desired weld profile.
Manipulation of the Electrode Angle
The angle at which the electrode is held relative to the workpiece affects the weld pool shape. A steeper angle (45-60°) directs the arc more towards the workpiece, resulting in a deeper penetration. A shallower angle (20-30°) produces a wider and shallower weld.
Shielding Gas Flow
The proper flow of shielding gas is essential for protecting the weld pool from contamination. An adequate flow rate prevents air from entering the weld area, ensuring a clean and sound weld.
Visual Cues
Observing the weld pool and the behaviour of the molten metal provides valuable insights into the welding process. By paying attention to visual cues such as the pool shape, arc stability, and spatter, welders can adjust their technique to achieve the desired outcome.
Visual Cue |
Interpretation |
Stable, teardrop-shaped pool |
Optimal welding conditions |
Excessive spatter |
Arc length too short or workpiece surface contaminated |
Weld pool collapsing |
Travel speed too fast or arc length too long |
Running the Bead
Running the bead is the process of laying down a weld on the workpiece. It involves controlling the arc length, travel speed, and angle of the electrode. These factors determine the shape, size, and quality of the weld.
To run a bead, follow these steps:
1. Establish an Arc
Strike the arc by touching the electrode to the workpiece and quickly pulling it back. Once the arc is established, maintain a steady distance between the electrode tip and the workpiece.
2. Control Arc Length
The arc length should be twice the diameter of the electrode. Too long an arc can cause porosity, while too short an arc can lead to undercut.
3. Control Travel Speed
The travel speed should be consistent throughout the weld. Too fast a speed will result in a weak weld, while too slow a speed will cause the weld to overheat.
4. Control Electrode Angle
The electrode should be held at a 45-degree angle to the workpiece. This angle provides good penetration and bead shape.
5. Keep the Weld Clean
Remove slag and other contaminants from the weld as you go. This will prevent porosity and other defects.
6. Use the Proper Electrode Size
The size of the electrode should be appropriate for the thickness of the workpiece. A larger electrode will produce a wider weld, while a smaller electrode will produce a narrower weld.
7. Practice and Experiment
Developing proficiency in running the bead requires practice and experimentation. Try different electrode sizes, travel speeds, and arc lengths to see how they affect the weld. With practice, you’ll be able to create strong, consistent welds.
Joining Two Pieces of Metal
The process of joining two pieces of metal using an arc welder involves several steps. Here’s a detailed guide to help you achieve a successful weld:
1. Prepare the Metal
Clean the surfaces of the metal that will be welded to remove any dirt, grease, or oxidation. This will ensure a good electrical connection and a strong weld.
2. Set Up the Welder
Choose the correct welding process (e.g., MIG, TIG, stick), select the appropriate welding wire, and adjust the settings according to the manufacturer’s instructions.
3. Create a Joint
Prepare the joint where the two pieces of metal will be joined. This can be a butt joint, edge joint, or T-joint, depending on the application.
4. Position the Electrode
Hold the welding electrode at the correct angle and distance from the joint. The angle will vary depending on the welding process and material thickness.
5. Start Welding
Strike an arc between the electrode and the metal. Maintain a steady hand and a consistent speed while moving along the joint.
6. Feed the Wire
In MIG welding, continuously feed the welding wire into the weld pool. The wire speed should be adjusted to match the welding speed and material thickness.
7. Maintain a Stable Arc Length
The distance between the electrode and the weld pool should be kept constant. This will ensure a good electrical connection and a consistent weld bead.
8. Inspect the Weld
Once the weld is complete, inspect it for any defects. Check for cracks, voids, or any other irregularities that may compromise the weld strength. If necessary, grind the weld bead and re-weld to achieve the desired quality.
Welding Process |
Electrode Type |
Filler Material |
MIG |
Continuously fed wire |
Solid or flux-cored wire |
TIG |
Tungsten electrode |
Separate filler rod |
Stick |
Consumable electrode |
Covered electrode |
Safety Precautions for Arc Welding
1. Wear Protective Gear
Arc welding generates intense heat and sparks, so it’s crucial to wear protective gear to prevent burns and injuries. This includes wearing a welding helmet with a face shield, leather gloves, and protective clothing made from fire-resistant materials.
2. Ensure Proper Ventilation
Arc welding fumes contain harmful gases, so it’s essential to ensure proper ventilation in the workspace. Use an exhaust fan or respirator to remove fumes and provide fresh air.
3. Fire Safety Measures
Arc welding creates sparks and molten metal, which can easily ignite nearby materials. Clear the work area of flammable materials, and have a fire extinguisher readily available.
4. Ground the Workpiece
To prevent electrical shock, ensure that the workpiece is properly grounded. This involves attaching a ground clamp to the metal being welded and connecting it to the welding machine.
5. Avoid Electrocution
Never touch the welding torch or electrodes with bare hands. Always use insulated handles and wear dry clothing to prevent electrical shock.
6. Eye Protection
Arc welding emits harmful ultraviolet (UV) radiation, so it’s vital to wear a welding helmet with a face shield that blocks UV rays. Failure to do so can lead to eye damage.
7. Protect Bystanders
Arc welding creates bright light and sparks that can be hazardous to bystanders. Ensure that the work area is isolated and that anyone nearby is wearing protective gear.
8. Avoid Confined Spaces
Arc welding in confined spaces can lead to asphyxiation from the fumes. Always weld in well-ventilated areas or use proper respiratory protection.
9. Metal Fumes
Arc welding releases metal fumes that can be toxic if inhaled. Use a fume extractor or respirator to remove harmful particles from the breathing zone.
10. Electrical Hazards
Arc welding involves high-voltage electricity. Be aware of the potential for electrical shocks and take precautions to prevent accidents, such as wearing insulated gloves and ensuring that equipment is properly grounded.
How to Use an Arc Welder
Arc welding is a type of welding that uses an electric arc to melt metal and join it together. It is a versatile and powerful welding process that can be used to weld a wide variety of metals, including steel, aluminum, stainless steel, and cast iron. Arc welding is also relatively easy to learn, making it a good option for beginners.
To use an arc welder, you will need the following equipment:
- An arc welder
- Welding cables
- A welding helmet
- Safety glasses
- Welding gloves
- Filler metal
Once you have gathered your equipment, you can begin welding. The first step is to set up your welder. This involves connecting the welding cables to the welder and the ground clamp to a metal surface near the work area. You will also need to set the welding current and voltage according to the type of metal you are welding.
Once your welder is set up, you can begin welding. To do this, hold the welding torch in one hand and the filler metal in the other. Strike an arc by touching the welding torch to the metal surface and then quickly pulling it away. Once an arc is established, you can begin moving the welding torch along the joint, melting the metal and adding filler metal to create a weld.
Arc welding is a relatively simple process, but it does require some practice to get good at it. With a little practice, you will be able to weld like a pro!
People Also Ask
What is the best type of arc welder for beginners?
There are two main types of arc welders: stick welders and MIG welders. Stick welders are less expensive and easier to learn, making them a good option for beginners. MIG welders are more versatile and can be used to weld a wider variety of metals, but they are more expensive and require more practice to master.
What are the safety precautions I need to take when arc welding?
Arc welding can be dangerous if you do not take proper safety precautions. Always wear a welding helmet, safety glasses, and welding gloves when welding. Also, make sure to work in a well-ventilated area and keep flammable materials away from the work area.
What are the different types of welding joints?
There are many different types of welding joints, each with its own advantages and disadvantages. The most common types of welding joints are the butt joint, the edge joint, the corner joint, and the T-joint.