
Prepare to witness the future of equipment innovation at Equip Expo 2025, a groundbreaking event that will unveil the latest advancements in construction, landscaping, and material handling.
Step into a realm where cutting-edge technologies and industry experts converge. Immerse yourself in an unparalleled experience, exploring the most innovative equipment and machinery shaping the future of these vital industries. Equip Expo 2025 promises to ignite your imagination and empower you with the tools to drive progress and efficiency.
Discover a symphony of innovation, where industry leaders unveil their latest creations and experts share their insights on the future of equipment. Expect thought-provoking demonstrations, interactive workshops, and invaluable networking opportunities that will propel your business to new heights. Equip Expo 2025 is not merely an exhibition; it is a catalyst for industry transformation.
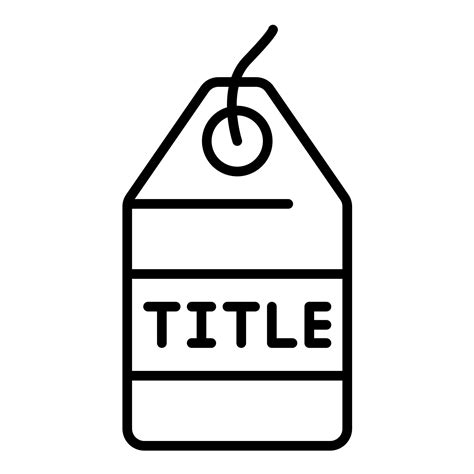
Unveiling the Future of Equipment at Equip Expo 2025
Discover the Latest Innovations:
Equip Expo 2025, the premier event for equipment professionals, is set to unveil the latest advancements and technologies shaping the future of equipment. Held from March 10-14, 2025, in Las Vegas, this year’s expo will showcase an unparalleled range of equipment, from construction and agriculture to industrial and mining. Attendees will have the opportunity to explore groundbreaking products, witness live demonstrations, and engage with industry leaders. Equip Expo 2025 promises to be an immersive experience, providing attendees with invaluable insights and inspiration.
Cutting-Edge Technology:
At Equip Expo 2025, attendees will witness firsthand the latest innovations driving equipment advancements. From artificial intelligence (AI)-powered machines to autonomous vehicles and sustainable energy solutions, the expo will showcase the transformative technologies shaping the industry. Experts will present cutting-edge research and case studies, demonstrating the practical applications and benefits of these technologies. Attendees will leave the expo with a comprehensive understanding of the future of equipment and how to leverage it for increased efficiency, productivity, and safety.
Interactive Demonstrations:
Beyond static displays, Equip Expo 2025 will offer attendees an unparalleled opportunity to witness live demonstrations of the latest equipment in action. Industry-leading manufacturers will showcase their products in dedicated demonstration areas, providing attendees with a firsthand look at their capabilities and applications. From heavy machinery in motion to innovative autonomous systems, these demonstrations will offer attendees a tangible experience of the future of equipment.
Industry Expertise:
Equip Expo 2025 will gather the brightest minds and industry experts from around the world. Attendees will have the opportunity to engage with leading manufacturers, researchers, and thought leaders. Through keynote speeches, panel discussions, and interactive workshops, attendees will gain valuable insights into the latest trends, best practices, and challenges facing the equipment industry. The expo provides a platform for knowledge sharing and collaboration, enabling attendees to expand their network and develop innovative solutions.
Networking and Collaboration:
Equip Expo 2025 is more than just an exhibition; it’s a hub for networking and collaboration. Attendees will have ample opportunities to connect with industry professionals, build relationships, and exchange ideas. The expo will host social events, networking receptions, and dedicated meeting spaces where attendees can connect with potential partners, customers, and suppliers. By leveraging the diverse expertise and connections at Equip Expo 2025, attendees can foster innovation and drive the industry forward.
|Event: Equip Expo 2025|Dates: March 10-14, 2025|Location: Las Vegas|
Technological Advancements Driving Industry Transformation
As the world continues to grapple with the Fourth Industrial Revolution, the construction industry is undergoing a profound transformation driven by technological advancements. Equip Expo 2025 will showcase the latest and most innovative technologies that are shaping the future of construction.
Internet of Things (IoT) and Connectivity
The Internet of Things (IoT) is rapidly changing the way we live and work, and the construction industry is no exception. IoT devices enable equipment, materials, and workers to communicate with each other and with central systems, providing real-time data and insights that can improve efficiency, safety, and sustainability.
At Equip Expo 2025, visitors will see IoT technologies in action, from sensors that monitor equipment performance to wearable devices that track worker safety. These technologies are giving construction companies the ability to optimize their operations, reduce downtime, and improve worker safety.
Technology |
Benefits |
Equipment tracking |
Monitor equipment location and utilization |
Predictive maintenance |
Identify potential equipment failures before they become critical |
Remote monitoring |
Access equipment data and control remotely |
Wearable safety devices |
Monitor worker health, fatigue, and location |
Data analytics |
Analyze data to improve decision-making and increase efficiency |
Industry Leaders Converge to Showcase Latest Innovations
Equip Expo 2025 will bring together industry leaders from around the globe to showcase the latest innovations in the construction industry. Attendees can expect to see a range of products and technologies, including:
- Advanced construction equipment
- Innovative building materials
- Smart construction technologies
Smart Construction Technologies
One of the most exciting areas of innovation in the construction industry is smart construction technologies. These technologies use data and analytics to improve efficiency, productivity, and safety. For example, drones can be used to inspect construction sites, collect data on progress, and identify potential hazards. 3D modeling and virtual reality can be used to create digital twins of buildings, which can help architects and engineers identify problems before construction begins.
Table 1: Examples of Smart Construction Technologies
Technology |
Benefits |
Drones |
Site inspection, data collection, hazard identification |
3D Modeling |
Digital twins, design optimization, clash detection |
Virtual Reality |
Immersive design review, training simulations, virtual walkthroughs |
Smart construction technologies are transforming the way buildings are designed, constructed, and managed. By leveraging data and analytics, these technologies can help the construction industry improve efficiency, productivity, and safety.
Sustainable Innovations Driving Equipment Development
Biodegradable and Recyclable Materials
Equipment manufacturers are increasingly using biodegradable and recyclable materials in their products to reduce waste and protect the environment. For example, companies like Caterpillar and Komatsu are developing construction equipment with biodegradable hydraulic fluids and lubricants, reducing the environmental impact of fluid leaks and spills.
Energy-Efficient Technologies
Advancements in energy-efficient technologies are reducing fuel consumption and emissions in equipment. Electric and hybrid equipment, coupled with improved battery technology, offer significant energy savings and lower operating costs.
Water-Saving Technologies
Water conservation is becoming a critical concern in equipment operations. Manufacturers are developing innovative solutions to reduce water usage. For example, dust suppression systems with advanced sensors optimize water application, minimizing waste.
Next-Generation Construction Technology
The construction industry is adopting next-generation technologies to enhance safety, productivity, and sustainability. Equipment like self-driving dozers, drones for site monitoring, and 3D modeling for design optimization are transforming construction processes. These technologies reduce human errors, increase efficiency, and contribute to a more sustainable future.
Technology |
Benefits |
Self-Driving Dozers |
Increased safety, reduced operator fatigue, and improved grading accuracy |
Drones for Site Monitoring |
Real-time data collection, progress monitoring, and enhanced safety |
3D Modeling for Design Optimization |
Reduced waste, improved material allocation, and enhanced collaboration |
Connectivity and Automation Shaping the Future Workspace
Efficiency and Productivity
Connectivity and automation enable seamless communication and coordination among equipment, operators, and systems. This enhanced connectivity streamlines workflows, reducing downtime and maximizing productivity.
Predictive Maintenance and Diagnostics
Automated monitoring systems continuously collect and analyze data, enabling the early detection of potential equipment issues. This allows for proactive maintenance and repairs, preventing costly breakdowns and unplanned downtime.
Enhanced Safety
Automated systems can perform hazardous or repetitive tasks, improving operator safety. Connected devices also enable real-time monitoring of work environments, ensuring compliance with safety regulations.
Data-Driven Decision-Making
The vast amounts of data generated by connected equipment and automated systems provide valuable insights for decision-making. This data empowers managers to optimize operations, identify areas for improvement, and enhance overall efficiency.
Value-Added Services
Connectivity and automation facilitate the delivery of value-added services, such as remote monitoring and support. Equipment manufacturers can provide proactive assistance, minimizing downtime and ensuring optimal performance.
Benefits of Connectivity and Automation |
– Increased efficiency |
– Improved safety |
– Predictive maintenance |
– Data-driven decision-making |
– Enhanced value-added services |
The Role of Artificial Intelligence in Optimizing Equipment Performance
Predictive Maintenance
AI algorithms analyze data from sensors to identify anomalies and predict failures before they occur. This enables proactive maintenance, reducing downtime and extending equipment life.
Autonomous Operation
AI-powered equipment can operate autonomously, performing tasks such as data collection, analysis, and decision-making. This frees up human resources for more complex tasks.
Condition Monitoring
AI algorithms monitor equipment conditions in real-time, identifying potential problems before they escalate. This helps prevent catastrophic failures and ensures optimal performance.
Energy Optimization
AI can optimize energy consumption by adjusting equipment parameters and identifying inefficiencies. This reduces energy costs and improves sustainability.
Quality Control
AI-based systems can perform automated quality checks, ensuring that equipment meets desired specifications. This improves product quality and reduces the risk of defects.
Historical Data Analysis
AI algorithms analyze historical data to identify trends, optimize operating parameters, and predict future performance. This helps equipment owners make informed decisions and improve equipment utilization.
|
Benefits of AI in Equipment Optimization: |
– Reduced downtime |
– Extended equipment life |
– Proactive maintenance |
– Improved efficiency |
– Increased safety |
– Reduced energy costs |
Smart Equipment Leading the Way to Increased Productivity
Precision Farming
Smart farming equipment utilizes sensors and data analytics to enhance crop yields, reduce input costs, and optimize water usage. Farmers can access real-time data on soil health, plant growth, and weather patterns, empowering them to make informed decisions.
Automated Harvesting and Sorting
Advanced harvesting machines with AI capabilities automate the harvesting process, increasing efficiency and reducing labor costs. Smart sorters classify and grade produce based on size, color, and quality, ensuring higher-quality products reach the market.
Precision Application Technologies
Smart sprayers and fertilizer applicators use GPS and variable-rate technology to deliver inputs with precision. This minimizes waste, reduces environmental impact, and maximizes crop yields.
Autonomous Vehicles
Self-driving tractors and other agricultural vehicles enable farmers to automate repetitive tasks, such as field preparation, planting, and spraying. This frees up valuable time for higher-level tasks, increasing overall efficiency.
Monitoring and Remote Control
Smart equipment is equipped with sensors and connectivity, allowing farmers to monitor and control operations remotely. Real-time alerts and diagnostic tools enable prompt maintenance and troubleshooting, reducing downtime.
Smart Livestock Management
Smart sensors and wearable devices track livestock health, feed intake, and movement patterns, providing valuable data for herd management. This information optimizes feeding strategies, improves animal health, and enhances productivity.
Benefits of Smart Equipment
- Increased productivity and efficiency
- Improved crop yields and quality
- Reduced labor costs and environmental impact
- Enhanced decision-making
- Time savings
- Improved animal health and welfare
- Greater flexibility and responsiveness
Safety and Ergonomics at the Forefront of Equip Expo 2025
In the fast-paced and demanding world of construction, safety and ergonomics must be a top priority. At Equip Expo 2025, these crucial factors will be at the forefront of every exhibitor’s showcase.
Enhanced Safety Features
Manufacturers will unveil groundbreaking safety technologies, including advanced equipment monitoring systems, real-time hazard detection, and collision avoidance tools.
Ergonomic Innovations
Exhibitors will present cutting-edge ergonomic solutions to reduce operator fatigue and enhance comfort, including adjustable seats, intuitive controls, and vibration-absorbing materials.
Training and Education
A comprehensive training program will provide hands-on demonstrations, case studies, and expert insights on the latest safety and ergonomic best practices.
Interactive Exhibits
Immersive exhibits will engage attendees with interactive simulations and virtual reality experiences, demonstrating the real-world applications of safety and ergonomic advancements.
Collaborative Partnerships
Industry leaders, regulatory bodies, and safety organizations will collaborate to promote industry-wide safety and ergonomic standards.
Showcase of Success Stories
Companies will share compelling case studies highlighting how safety and ergonomic initiatives have transformed their operations, resulting in reduced accidents, increased productivity, and improved employee well-being.
Data-Driven Insights
Advanced data analytics will be utilized to provide valuable insights into equipment performance, identify potential hazards, and optimize safety protocols.
Future-Focused Solutions
Exhibitors will present cutting-edge technologies that anticipate future safety and ergonomic challenges, ensuring a proactive approach to safeguarding construction workers.
Safety Feature |
Ergonomic Innovation |
Collision avoidance systems |
Adjustable seats |
Real-time hazard detection |
Intuitive controls |
Advanced equipment monitoring |
Vibration-absorbing materials |
Equipment Financing and Investment Strategies for the Future
Equipment Leasing
Leasing allows businesses to acquire equipment without the upfront capital investment. This can free up cash flow for other expenses while spreading out the cost of equipment acquisition over a longer period.
Equipment Loans
Equipment loans provide a fixed financing option with monthly payments and a term typically ranging from two to five years. This option offers ownership of the equipment once the loan is repaid.
Venture Capital
Venture capital is a funding option for businesses with high growth potential. Investors provide capital in exchange for an equity stake in the business, which can be used to purchase or lease equipment.
Crowdfunding
Crowdfunding is a popular method of raising small amounts of capital from a large number of individuals. This option can be used to fund the acquisition of equipment or other business expenses.
Government Grants and Loans
Government grants and loans can provide funding for equipment acquisitions, particularly for businesses engaged in research or innovation.
Equipment Investment Strategies
Investing in Energy-Efficient Equipment
Energy-efficient equipment can reduce operating costs and improve sustainability. Investing in energy-efficient equipment can also qualify businesses for tax incentives or rebates.
Automation and Robotics
Automating processes and investing in robotics can increase productivity, reduce labor costs, and enhance accuracy. This can allow businesses to remain competitive and respond to changing market demands.
Remote Monitoring and Predictive Maintenance
Remote monitoring and predictive maintenance technologies can help businesses monitor their equipment remotely and identify potential issues before they become major problems. This can extend the life of equipment and minimize unplanned downtime.
The Impact of Global Economic Trends on the Equipment Industry
Economic Slowdown and Recovery
Global economic fluctuations impact equipment demand. Economic downturns lead to reduced investment in equipment, while recoveries spur spending on new and upgraded machinery.
Demographic Changes
Aging populations and shrinking workforces in developed economies create demand for equipment that enhances productivity and automation.
Technological Advancements
Innovations in artificial intelligence, automation, and connectivity are revolutionizing equipment design and capabilities.
Environmental Regulations
Stricter environmental regulations drive demand for equipment that reduces emissions and improves sustainability.
E-commerce and Digitalization
The rise of e-commerce and digital platforms has increased the need for equipment to support supply chains and distribution networks.
Geopolitical Dynamics
Trade wars, sanctions, and political instability can disrupt supply chains and equipment availability.
Infrastructure Investments
Government investments in infrastructure projects create opportunities for equipment manufacturers.
Competition from Emerging Economies
Equipment manufacturers from emerging economies are gaining market share with lower-cost and innovative products.
Smart Cities and Urbanization
Increasing urbanization drives demand for equipment for construction, waste management, and other urban services.
Sector-Specific Trends
Each equipment sector faces unique trends, such as healthcare’s focus on automation and construction’s adoption of virtual reality.
Sector |
Trends |
Healthcare |
Automation, Telemedicine |
Construction |
Virtual Reality, Pre-fabrication |
Manufacturing |
Industrial Internet of Things, Robotics |
Transportation |
Electric Vehicles, Autonomous Driving |
Agriculture |
Precision Farming, Data Analytics |
Equip Expo 2025: The Future of Construction Equipment
Equip Expo 2025 is shaping up to be the most cutting-edge and innovative construction equipment show ever. The event will feature the latest and greatest in earthmoving, paving, concrete, and other construction equipment from leading manufacturers around the world. In addition to the equipment on display, Equip Expo 2025 will also offer a variety of educational sessions, workshops, and demonstrations. These sessions will cover a wide range of topics, including the latest trends in construction technology, best practices for equipment operation, and safety on the job site.
If you are involved in the construction industry, then you need to attend Equip Expo 2025. This is your chance to see the latest equipment, learn about the latest trends, and network with other professionals in the industry. Equip Expo 2025 is the premier event for construction equipment, and it is an event that you will not want to miss.
People Also Ask
When is Equip Expo 2025?
Equip Expo 2025 will be held on March 14-18, 2025, at the Las Vegas Convention Center in Las Vegas, Nevada.
How do I register for Equip Expo 2025?
You can register for Equip Expo 2025 online at the show’s website.
What is the cost to attend Equip Expo 2025?
The cost to attend Equip Expo 2025 is $100 for a one-day pass, $200 for a three-day pass, and $300 for a five-day pass. Registration fees include access to all exhibits, educational sessions, workshops, and demonstrations.
What are the hours of Equip Expo 2025?
Equip Expo 2025 will be open from 9:00 am to 5:00 pm each day.