
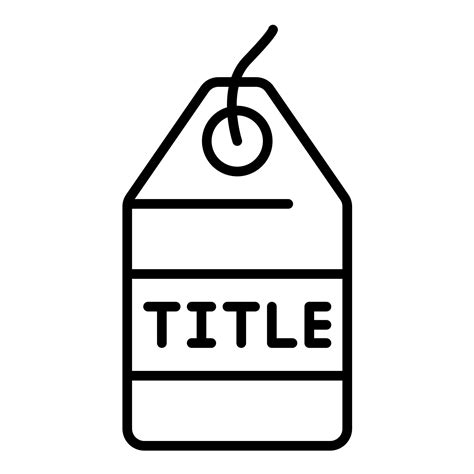
When working with silicone, it’s essential to understand its unique properties and how to handle it effectively. Drying silicone is a crucial step in many applications, and understanding the right techniques can save you time and ensure a successful outcome. In this article, we will delve into the details of drying silicone faster, providing practical tips and tricks to accelerate the process.
Drying silicone faster requires controlling the environment and harnessing specific techniques. Controlling temperature and humidity plays a significant role, as higher temperatures and higher humidity levels can slow down the drying process. Conversely, exposing silicone to lower temperatures and lower humidity levels can accelerate drying. Using a fan or dehumidifier can create the desired conditions and promote faster drying. Additionally, preheating the silicone before application can reduce the drying time since it allows the silicone to start curing at a higher temperature.
Beyond controlling the environment, surface preparation and proper application techniques also contribute to faster drying. Cleaning the surface thoroughly before applying silicone removes any contaminants or oil that could interfere with adhesion and hinder drying. When applying silicone, ensure a thin and even layer to facilitate faster curing. Avoid applying excessive silicone, as thicker layers take longer to dry. Furthermore, consider using a silicone accelerator, a chemical additive that speeds up the curing process. Choosing the right type of silicone is equally important, as different formulations have varying drying times. Understanding these factors and implementing the appropriate techniques will significantly improve the drying efficiency of silicone.
Applying Heat
Using heat is an effective way to accelerate the drying process of silicone. There are several options available to apply heat, including:
1. Hairdryer
A hairdryer can provide a gentle stream of warm air that can help dry silicone faster. Hold the hairdryer a few inches away from the silicone surface and move it around continuously to avoid overheating.
2. Heat Gun
A heat gun produces a more intense stream of hot air than a hairdryer. It is important to use caution when using a heat gun, as overheating can damage the silicone. Keep the heat gun moving constantly and avoid holding it too close to the surface.
3. Silicone Curing Oven
A silicone curing oven is a specialized device designed to dry silicone quickly and evenly. It provides controlled heat and air circulation, ensuring optimal curing conditions. Here are some key considerations when using a silicone curing oven:
Parameter |
Recommended Value |
Temperature |
60-80°C (140-176°F) |
Duration |
As per manufacturer’s instructions |
Airflow |
Moderate to high |
By following these guidelines, you can effectively apply heat to dry silicone faster while maintaining its integrity and performance.
Baking in the Oven
Step 1: Preheat the Oven
Preheat your oven to the temperature specified by the silicone manufacturer. Typically, this will be around 150-200 degrees Fahrenheit (65-93 degrees Celsius).
Step 2: Place the Silicone on a Baking Sheet
Place the silicone object on a baking sheet lined with parchment paper. This will prevent the silicone from sticking to the pan and make cleanup easier.
Step 3: Bake the Silicone
Place the baking sheet in the preheated oven and bake for the amount of time specified by the manufacturer. This will typically be around 10-30 minutes.
Step 4: Monitor the Silicone
During baking, keep an eye on the silicone to ensure that it does not overheat. If the silicone starts to brown or bubble, remove it from the oven immediately.
Step 5: Remove the Silicone from the Oven
Once the baking time is complete, remove the baking sheet from the oven and allow the silicone to cool completely on a wire rack. This can take several hours, depending on the thickness of the silicone.
To further accelerate the drying process, consider these additional tips:
Tip |
Description |
Use a fan oven |
The air circulation will help to dry the silicone more quickly. |
Place the baking sheet near the top of the oven |
The higher temperature will help to evaporate the moisture from the silicone. |
Use a lower temperature for a longer period of time |
This will help to prevent the silicone from overheating and becoming brittle. |
Using a Dehumidifier
A dehumidifier is an excellent option to effectively reduce the humidity in your space, allowing silicone to dry faster. Here are some key points to remember when utilizing a dehumidifier:
Choose the Right Dehumidifier
Select a dehumidifier with sufficient capacity for the size of the area where the silicone is being dried. A higher capacity dehumidifier will remove moisture more rapidly.
Proper Placement
Place the dehumidifier near the silicone to maximize its effectiveness. Ensure there are no obstructions blocking the airflow, as this can hinder the dehumidification process.
Continuous Drainage
Connect the dehumidifier to a continuous drainage hose to prevent it from shutting off due to a full water tank. This ensures uninterrupted dehumidification, allowing the silicone to dry more efficiently.
Circulate the Air
Use fans or open windows to circulate air around the silicone. This promotes even drying and prevents moisture from settling on the surface.
Monitor Humidity
Monitor the humidity levels in the area using a hygrometer. Once the humidity drops below the ideal range for silicone drying (around 30-50%), you can discontinue using the dehumidifier.
Types of Dehumidifiers
There are two main types of dehumidifiers available:
Type |
Description |
Refrigerant Dehumidifiers |
Use a compressor and refrigerant to remove moisture from the air. They are typically more efficient and effective in warm and humid environments.
|
Desiccant Dehumidifiers |
Use a desiccant material to absorb moisture from the air. They are more suitable for cold and dry environments where refrigerant dehumidifiers may not be as effective.
|
Natural Sunlight Drying
Sunlight is a natural and effective way to dry silicone. The UV rays in sunlight break down the silicone bonds and cause the silicone to release its moisture.
To dry silicone using sunlight, follow these steps:
1. Clean the silicone with a mild soap and water solution.
2. Rinse the silicone thoroughly with water.
3. Place the silicone on a clean, dry surface.
4. Expose the silicone to direct sunlight.
5. Allow the silicone to dry for 24-48 hours.
6. If the silicone is not completely dry after 24-48 hours, you can repeat the process.
7. Once the silicone is dry, you can store it in a cool, dry place. Here is a table summarizing the steps for drying silicone using sunlight:
Step |
Description |
1 |
Clean the silicone with a mild soap and water solution. |
2 |
Rinse the silicone thoroughly with water. |
3 |
Place the silicone on a clean, dry surface. |
4 |
Expose the silicone to direct sunlight. |
5 |
Allow the silicone to dry for 24-48 hours. |
6 |
If the silicone is not completely dry after 24-48 hours, repeat the process. |
7 |
Once the silicone is dry, store it in a cool, dry place. |
Forced Air Drying
Forced air drying is a method of accelerating the drying process by using a fan or hair dryer to blow warm air over the silicone. This helps to evaporate the water and speed up the curing process.
To force air dry silicone, follow these steps:
1. Clean the silicone surface.
Remove any dirt or debris from the surface of the silicone using a clean cloth.
2. Set up a fan or hair dryer.
Fan |
Hair Dryer |
Set up a fan in a well-ventilated area and position it so that the air is blowing directly over the silicone surface. |
Set the hair dryer to a low or medium heat setting and hold it about 6 inches away from the silicone surface. Keep the hair dryer moving to prevent overheating. |
3. Dry the silicone.
Fan |
Hair Dryer |
Allow the fan to blow air over the silicone for several hours, or until the surface is dry to the touch. |
Use the hair dryer for 10-15 minutes at a time, then let the silicone cool down. Repeat this process as needed until the silicone is dry to the touch. |
4. Cure the silicone.
Once the silicone is dry to the touch, let it cure for the time specified by the manufacturer. This will allow the silicone to reach its full strength and durability.
Microwave Drying
Microwave drying is a fast and effective way to dry silicone. It works by using microwaves to heat the water molecules in the silicone, which causes them to evaporate. This process can significantly reduce the drying time compared to air drying.
Materials Needed
- Microwave
- Silicone item
- Paper towels
Instructions
1. Place the silicone item on a microwave-safe plate.
2. Cover the silicone item with paper towels.
3. Microwave on high for 30-60 seconds.
4. Check the silicone item to see if it is dry. If not, microwave for an additional 15-30 seconds.
5. Remove the silicone item from the microwave and let it cool completely.
Precautions
* Do not microwave silicone for more than 60 seconds at a time.
* Do not leave the silicone unattended while it is in the microwave.
* If the silicone starts to smoke or burn, stop microwaving immediately and let it cool down.
Tips
* For thicker silicone items, you may need to microwave for longer periods of time.
* You can also use a fan to help circulate the air and speed up the drying process.
* If you are drying a silicone mold, make sure to flour it before microwaving to prevent sticking.
* Do not microwave silicone with metal objects.
* Dry silicone in a well-ventilated area.
How To Dry Silicone Faster
Silicone is a versatile material used in a variety of applications, from construction to automotive to medical. One of the challenges of working with silicone is that it can take a long time to dry. However, there are a few things you can do to speed up the drying process.
1. Use a heat gun. A heat gun can be used to quickly heat up the silicone, which will cause it to dry faster. Be careful not to overheat the silicone, as this can damage it.
2. Apply a catalyst. A catalyst is a substance that can be added to silicone to speed up the drying process. Catalysts are available in a variety of forms, so be sure to read the instructions carefully before using one.
3. Increase the air circulation. Increasing the air circulation around the silicone will help to evaporate the moisture and speed up the drying process. You can do this by opening windows or doors, or by using a fan.
4. Use a dehumidifier. A dehumidifier can be used to remove moisture from the air, which will help to speed up the drying process. Dehumidifiers are available in a variety of sizes and capacities, so be sure to choose one that is appropriate for the size of your space.
People Also Ask About How To Dry Silicone Faster
How long does silicone take to dry?
The drying time for silicone can vary depending on the type of silicone, the thickness of the application, and the environmental conditions. In general, silicone will dry to the touch in 24-48 hours and will be fully cured in 7-14 days.
Can you speed up the drying time of silicone?
Yes, there are a few things you can do to speed up the drying time of silicone. These include using a heat gun, applying a catalyst, increasing the air circulation, and using a dehumidifier.
Is it OK to use a hair dryer to dry silicone?
It is not recommended to use a hair dryer to dry silicone. The heat from the hair dryer can damage the silicone and make it more difficult to dry.