
A sash is an important part of any pageant ensemble. It can add a touch of elegance and sophistication to your look, and it can help you to stand out from the competition. If you’re looking for a way to make your pageant gown even more special, consider making your own sash. It’s a relatively simple project that can be completed in just a few hours. Here’s how to do it:
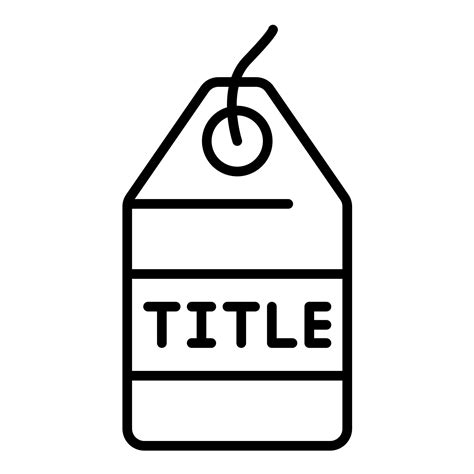
First, you’ll need to gather your materials. You’ll need a piece of fabric that is at least 6 inches wide and 36 inches long. You can use any type of fabric you like, but satin or silk is a good choice. You’ll also need a sewing machine, thread, a pair of scissors, and a measuring tape. Once you have your materials, you can begin to make your sash. Start by measuring and cutting a piece of fabric that is 6 inches wide and 36 inches long. Then, fold the fabric in half lengthwise and press it with an iron. This will create a crease down the center of the fabric.
Next, you’ll need to sew the two ends of the fabric together. Place the ends of the fabric together, right sides facing, and sew them together with a straight stitch. Be sure to leave a small opening in the seam so that you can turn the sash right side out. Once you have sewn the two ends of the fabric together, turn the sash right side out and press it with an iron. Then, you can add any embellishments you like to the sash. You could add sequins, beads, or embroidery. You could also add a fringe or a tassel to the ends of the sash. Once you’re happy with the way your sash looks, you’re ready to wear it to your next pageant.
Choosing the Right Fabric
The fabric you choose for your sash will have a significant impact on its overall appearance and durability. Here are some factors to consider when selecting your fabric:
- Material: Sashes can be made from a variety of materials, including satin, silk, velvet, and lace. Satin is a popular choice for sashes due to its smooth, glossy finish. Silk is another luxurious option, known for its soft and elegant drape. Velvet adds a touch of richness and opulence, while lace can create a more delicate and romantic look.
- Color: The color of your sash should complement your pageant outfit and theme. Choose a color that will stand out against your dress and convey the desired message or symbolism. You may want to consider using the colors of your pageant system or organization.
- Opacity: Consider the opacity of the fabric when choosing. Sheer fabrics, such as chiffon or organza, will allow light to pass through, while opaque fabrics will block out light. Choose an opacity that aligns with the desired level of visibility and modesty for your sash.
- Weight: The weight of the fabric will affect the drape and flow of the sash. Heavier fabrics, such as velvet, will create a more dramatic drape, while lighter fabrics, such as satin, will have a more fluid and graceful movement.
- Embellishments: You may also want to consider adding embellishments to your sash, such as embroidery, appliqués, or sequins. Embellishments can enhance the visual appeal of your sash and add a touch of personalization.
Measuring and Cutting the Sash
Step 1: Determine the Sash Length
The length of the sash will vary depending on the person’s height and the desired effect. For a traditional sash, measure from the shoulder to the opposite hip. For a longer sash that can be worn over the shoulder and crossed in the front, add an additional 6-12 inches.
Step 2: Determine the Sash Width
The width of the sash is typically 3-5 inches. However, you can adjust the width to suit your preferences or the size of the person wearing it.
Step 3: Cut the Sash
Once you have determined the length and width of the sash, cut a piece of fabric according to those measurements. Use a sharp pair of scissors to ensure a clean cut.
Sash Length |
Sash Width |
Shoulder to hip + 6-12 inches (for a longer sash) |
3-5 inches |
Adding the Fringe and Trim
The fringe and trim are the finishing touches that add flair to your sash. You can choose from a variety of materials and styles to complement your design.
To add fringe, first measure the length you need and cut it from the roll. Fold the top edge of the fringe over the raw edge of the sash and sew it in place. For a more finished look, serge or zigzag stitch the edges to prevent fraying.
Trim, such as ribbons or rickrack, can be added in a similar manner. Fold the edge of the trim over the raw edge of the sash and sew it in place. You can also use fabric glue to attach trim, but be sure to let it dry completely before handling the sash.
Fringe Materials |
Trim Materials |
Silk |
Ribbons |
Metallic |
Rickrack |
Feather |
Lace |
Beaded |
Sequins |
Get creative with your fringe and trim choices to create a sash that is uniquely yours. Experiment with different colors, textures, and styles to achieve the perfect look.
Remember, the most important thing is to have fun with it! Use your imagination and create a sash that you’re proud of.
Embellishing the Sash
Once you have the basic sash sewn, it’s time to embellish it to make it truly unique and eye-catching. Here are some ideas:
Adding Rhinestones or Beads
Rhinestones and beads can add a touch of sparkle and glamour to your sash. You can glue them on in any design you like, or use a hot glue gun to create more elaborate designs. If you’re using a hot glue gun, be careful not to burn yourself or the fabric of the sash.
Embroidery
Embroidery is another great way to add embellishment to your sash. You can embroider your name, a special message, or any other design you like. If you’re not skilled at embroidery, you can find someone who can do it for you.
Appliqués
Appliqués are a great way to add a pop of color and texture to your sash. You can find appliqués at most fabric stores, or you can make your own using scraps of fabric. To apply appliqués, simply glue them on to the sash using fabric glue.
Ribbons and Other Embellishments
Ribbons and other embellishments can also be used to add a touch of flair to your sash. You can use ribbons to create bows, streamers, or other designs. You can also use other embellishments such as feathers, sequins, or buttons to add a unique touch to your sash.
Attaching the Ends Together
Once you have the sash cut to the desired length, it’s time to attach the ends together. There are a few different ways to do this, but the most common method is to use a glue gun. This is a simple and effective way to attach the ends together, but it’s important to be careful not to use too much glue, as it can create a mess and make the sash difficult to work with.
Here are the steps on how to attach the ends of a sash together using a glue gun:
- Apply a thin line of glue to one end of the sash.
- Fold the other end of the sash over the glued end, making sure that the edges are lined up.
- Press the two ends together firmly for a few seconds, until the glue has set.
- Repeat steps 1-3 for the other end of the sash.
- Allow the glue to dry completely before using the sash.
If you don’t have a glue gun, you can also attach the ends of a sash together using fabric glue or needle and thread.
Using fabric glue:
- Apply a thin line of fabric glue to one end of the sash.
- Fold the other end of the sash over the glued end, making sure that the edges are lined up.
- Press the two ends together firmly for a few minutes, until the glue has set.
- Allow the glue to dry completely before using the sash.
Using needle and thread:
- Thread a needle with a strong thread.
- Tie a knot in one end of the thread.
- Sew the two ends of the sash together, using a small stitch.
- Tie a knot in the other end of the thread, and trim any excess thread.
Method |
Pros |
Cons |
Glue gun |
Quick and easy |
Can be messy |
Fabric glue |
Strong and durable |
Can take longer to set |
Needle and thread |
Secure and invisible |
Can be time-consuming |
Personalizing the Sash
Making a sash for a pageant can be a fun and creative way to express your individuality. Here are a few tips on how to personalize your sash:
Choose the right fabric and color
The fabric you choose for your sash should be sturdy enough to hold up during the pageant, but it should also be comfortable to wear. Some popular choices include satin, silk, or velvet. The color of your sash should complement your outfit and your overall look.
Add embellishments
Embellishments can add a touch of personality to your sash. You can add rhinestones, sequins, beads, or other decorations. Be sure to use embellishments that are securely attached so that they don’t fall off during the pageant.
Personalize the text
The text on your sash is a great way to express your personality and your goals. You can include your name, your pageant title, or a special message. The text should be easy to read and should be in a font that complements your sash.
Add a personal touch
There are many other ways to personalize your sash. You can add a photo of yourself, a special symbol, or a piece of fabric from a meaningful item. The more personal you make your sash, the more it will reflect your unique style.
Fonts for Sashes
There are many different fonts that you can use for the text on your sash. Here are a few popular choices:
Font |
Description |
Arial |
A classic font that is easy to read |
Times New Roman |
A traditional font that is often used for formal documents |
Courier New |
A typewriter-style font that is often used for code or text-based art |
Ironing and Finishing the Sash
Once you have sewn the sash, it’s time to give it a professional finish. Here are the steps involved:
Ironing the Sash
Lay the sash flat on an ironing board and iron it on a low heat setting. Iron in the direction of the grain of the fabric to avoid stretching or distorting it. Use a pressing cloth to protect the fabric from direct heat.
Applying Embellishments
If you desire, you can add embellishments such as beads, sequins, or embroidery to the sash. Use a fabric glue or sew them on securely.
Creating a Stiffener
To give the sash more structure, you can insert a stiffener such as buckram or interfacing. Cut the stiffener to the same size as the sash and place it inside the fabric, aligning the edges. Secure it in place with stitches or fabric glue.
Adding Fringe or Tassels
If you want to add fringe or tassels to the ends of the sash, now is the time to do so. Sew or glue them in place securely.
Rounding the Edges
For a more polished look, you can round the edges of the sash. Fold the raw edges over twice and stitch them down. Alternatively, you can use bias tape to create a neat and decorative finish.
Trimming Excess Fabric
Once you have finished ironing and embellishing the sash, trim any excess fabric around the edges. This will give it a clean and professional look.
Pressing the Final Product
Finally, give the sash a final press to set the seams and embellishments. Use a low heat setting and a pressing cloth to avoid damaging the fabric.
Materials
You will need the following materials to make a sash for a pageant:
- Fabric (satin, silk, or velvet)
- Scissors
- Measuring tape or ruler
- Iron and ironing board
- Thread
- Needle
- Optional: Embellishments (such as sequins, beads, or ribbon)
Instructions
1. Measure and cut the fabric to the desired length and width. The length of the sash will depend on the size of the person wearing it, and the width should be about 4 inches.
2. Fold the fabric in half lengthwise and press it with an iron. This will create a crease down the center of the fabric.
3. Open up the fabric and fold the raw edges of the fabric inward by about 1/2 inch. Press the fabric again to create a crease along the folded edges.
4. Fold the fabric in half again, bringing the folded edges together. Press the fabric again to create a crease along the folded edge.
5. Sew the folded edges together using a needle and thread or consider using a sewing machine instead.
6. Turn the sash right side out.
7. Press the sash again to give it a finished look.
8. Add any desired embellishments to the sash. You can sew on sequins, beads, or ribbon to create a unique and personalized look.
Proper Care and Storage
To ensure your sash remains looking its best, it is important to properly care and store it. Here are some care and storage tips:
- Hand-wash the sash in cold water with a mild detergent. Do not use bleach or harsh chemicals.
- Lay the sash flat to dry or hang it on a hanger in a well-ventilated area.
- Do not iron the sash directly. Instead, place a cloth over the sash and iron it on a low setting.
- Store the sash in a cool, dry place, away from direct sunlight.
- Avoid folding the sash, as this can cause creases and wrinkles.
Creative Design Ideas
Crafting a memorable sash for a pageant requires careful consideration and a touch of creativity. Here are some innovative ideas:
1. Intricate Embroidery
Adorn the sash with elegant embroidery featuring motifs that symbolize the pageant theme or the contestant’s personality.
2. Appliqué Embellishments
Create a unique design by adding fabric appliqués, such as flowers, butterflies, or stars, in vibrant colors.
3. Sequins and Beads
Elevate the sash with shimmering sequins and delicate beads, creating a dazzling effect that catches the light.
4. Fringe and Tassels
Add a touch of movement and flair with fringe or tassels along the sash’s edges.
5. Personalized Lettering
Inscribe the contestant’s name or a meaningful message into the sash, using stylish typography.
6. Ruffles and Pleats
Create a voluminous and eye-catching sash by incorporating ruffles or pleats into its design.
7. Photographic Embellishments
Print photographs onto the sash, displaying images of the contestant, their hobbies, or their aspirations.
8. Painted Silhouettes
Paint intricate silhouettes onto the sash, creating an elegant and artistic effect.
9. 3D Elements and Sculpture
Go beyond traditional fabrics by incorporating 3D elements, such as sculpted flowers or miniature replicas, to create a truly standout sash. These elements can add depth, texture, and visual interest, making the sash a focal point of the contestant’s ensemble. Utilize materials like wire, clay, or papier-mâché to craft these 3D embellishments, allowing for intricate detailing and customization. Consider the overall theme of the pageant and the contestant’s personality when designing these elements, ensuring they complement the sash and enhance the contestant’s presentation.
Tips for Competition Success
Participating in a pageant can be an enriching experience, but it also demands preparation and dedication. Here are some tips to help you achieve success in your pageant journey:
1. Embody Confidence and Positivity
Confidence radiates through your every move and word. Cultivate a positive mindset, believe in yourself, and exude an aura of enthusiasm that will captivate the audience.
2. Research and Understand the Pageant System
Familiarize yourself with the specific pageant you’re competing in. Learn its history, values, and judging criteria to tailor your performance accordingly.
3. Craft a Compelling Platform
Choose a social cause you’re passionate about and develop a well-articulated platform that showcases your advocacy and personal mission.
4. Practice Your Interview Skills
Interviews are crucial for judges to assess your intelligence, personality, and communication abilities. Prepare thoughtful answers, practice active listening, and maintain eye contact.
5. Develop a Strong Stage Presence
Master your poise, posture, and facial expressions to command the stage with confidence. Practice walking gracefully, smiling naturally, and engaging with the audience.
6. Prepare for Evening Wear
Choose an elegant and age-appropriate gown that flatters your figure and complements your overall presentation. Ensure it’s well-tailored, accessorized tastefully, and suits the pageant’s dress code.
7. Embrace Swimsuit with Confidence
Exude confidence and comfort in your swimsuit. Practice walking gracefully, maintain a composed posture, and avoid excessive posing.
8. Enchant with a Talent Presentation
Showcase your unique talent with enthusiasm and precision. Whether it’s singing, dancing, playing an instrument, or performing a skill, aim to impress with your artistry and stage presence.
9. Prepare Your Wardrobe and Accessories
Plan your wardrobe meticulously to ensure it’s cohesive and appropriate for each segment of the competition. Pack a variety of stylish options, comfortable shoes, and tasteful accessories.
10. Cultivate a Healthy Lifestyle and Appearance
Maintaining a healthy diet, exercising regularly, and getting adequate sleep will enhance your overall well-being and appearance. It will provide you with a vibrant glow and the stamina to endure the pageant’s demands.
Lifestyle Factor |
Benefits |
Healthy Diet |
Improved energy levels and skin health |
Regular Exercise |
Boosted confidence, improved posture, and reduced stress |
Adequate Sleep |
Reduced puffiness, increased alertness, and enhanced mental clarity |
How to Make a Sash for a Pageant
Creating a sash for a pageant is a fun and rewarding experience. With a few simple materials and a little bit of creativity, you can make a sash that will be both beautiful and memorable. Here are the steps on how to make a sash for a pageant:
- Gather your materials. You will need:
- A piece of fabric (the size will depend on the size of the sash you want to make)
- A sewing machine
- Thread
- Scissors
- Embroidery thread (optional)
- Embroidery needles (optional)
- Cut out the fabric. The size of the fabric will depend on the size of the sash you want to make. For a standard-sized sash, you will need a piece of fabric that is about 6 inches wide and 72 inches long.
- Fold the fabric in half lengthwise and press it. This will create a crease down the center of the fabric.
- Sew the edges of the fabric together. Starting at one end of the fabric, sew along the edge, using a 1/4-inch seam allowance. When you reach the end of the fabric, turn it around and sew back up the other side.
- Turn the sash right side out. Use a chopstick or a blunt object to help you turn the sash right side out. Once the sash is turned right side out, press it flat.
- Embroider the sash (optional). If you want to add embroidery to your sash, now is the time to do it. You can embroider the sash with the contestant’s name, title, or any other design you like.
- Attach the sash to the contestant. The sash can be attached to the contestant’s shoulder using a safety pin or a piece of hook and loop tape.
People Also Ask
What is the best fabric to use for a pageant sash?
The best fabric to use for a pageant sash is a lightweight fabric that drapes well. Some good options include satin, silk, or chiffon.
What size should a pageant sash be?
The size of a pageant sash will vary depending on the age and size of the contestant. A standard-sized sash for an adult is about 6 inches wide and 72 inches long.
How do you attach a sash to a contestant?
The sash can be attached to the contestant’s shoulder using a safety pin or a piece of hook and loop tape.
How do you make a sash for a pageant?
To make a sash for a pageant, you will need a piece of fabric, a sewing machine, thread, and scissors. You can also add embroidery to the sash if you like.