
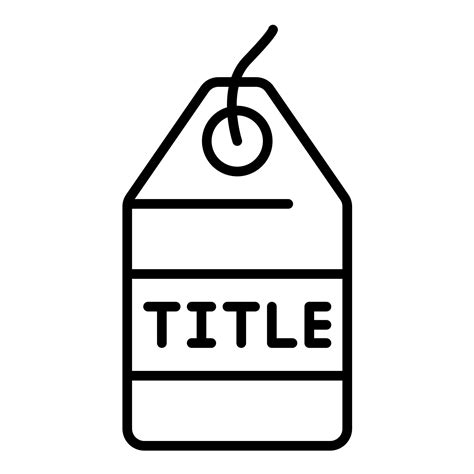
Halter tops are a summer staple, and they’re surprisingly easy to make. With just a few simple steps, you can create a halter top that’s perfect for a day at the beach or a night out on the town. The best part is, you don’t need to be a sewing expert to make one. Even beginners can follow these simple instructions to create a stylish and comfortable halter top.
To get started, you’ll need a few basic materials. You’ll need a piece of fabric that is at least 1 yard long and 45 inches wide. You’ll also need a pair of scissors, a measuring tape, a sewing machine, and thread. Once you have your materials gathered, you’re ready to start sewing. First, fold the fabric in half lengthwise, and then fold it in half again widthwise. This will create a square or rectangle. Cut out the square or rectangle, and you’ll have two pieces of fabric that are the same size.
Next, take one of the pieces of fabric and fold it in half again, so that the two long edges are touching. Sew the two long edges together, using a 1/2-inch seam allowance. This will create a tube of fabric. Turn the tube of fabric right side out, and then fold the top edge over by 1 inch. Press the fold, and then sew the fold down using a 1/2-inch seam allowance. This will create the neckline of the halter top.
Selecting the Right Fabric
Choosing the ideal fabric for your halter top is crucial to ensure both comfort and style. Consider the following factors when making your selection:
Fabric Weight and Drape
The weight of the fabric will determine the opacity and drape of your top. Lightweight fabrics like chiffon and silk create flowing, airy silhouettes, while heavier fabrics like denim and canvas provide more structure and coverage. Choose a fabric that suits your desired look and level of coverage.
Breathability and Comfort
For a top that you’ll be wearing for an extended period or in warm weather, breathability is essential. Natural fibers like cotton, linen, and hemp allow air to circulate, keeping you cool and comfortable. Synthetic fibers may be less breathable, so consider alternatives if breathability is a priority.
Fabric Stretch and Flexibility
Consider the amount of stretch you desire in your halter top. Stretch fabrics like jersey or spandex provide a more comfortable, form-fitting look. Non-stretch fabrics offer a structured, tailored appearance. Choose a fabric that aligns with your fit preferences and the intended use of the top.
Opacity and Texture
The opacity of the fabric will affect the level of coverage. Sheer fabrics like lace or mesh create a more revealing look, while opaque fabrics like canvas or denim provide full coverage. The texture of the fabric can also contribute to the overall aesthetic, with fabrics like velvet adding a touch of luxury or lace adding a delicate touch.
Care and Maintenance
Consider the care and maintenance requirements of the fabric you choose. Some fabrics may require delicate handwashing, while others can be machine-washed. Check the fabric care instructions to ensure that the fabric you select aligns with your preferred laundry routine.
Fabric Type |
Weight |
Drape |
Breathability |
Chiffon |
Lightweight |
Flowing |
High |
Silk |
Lightweight |
Drapey |
Moderate |
Denim |
Heavyweight |
Structured |
Low |
Cotton |
Medium-weight |
Versatile |
High |
Linen |
Lightweight |
Crinkled |
High |
Measuring for a Perfect Fit
To ensure a well-fitting halter top, accurate measurements are crucial. Here’s a detailed guide to taking the necessary measurements:
Bust Measurement
Wrap a measuring tape around the fullest part of your bust, ensuring it lies flat and parallel to the floor. Record the measurement in inches or centimeters.
Underbust Measurement
Measure directly under your bust, where the band of a bra would typically rest. The tape should remain parallel to the floor. Note down this measurement as well.
Strap Measurement(Shoulder To Nipple)
Find the point where your shoulder strap would naturally rest on your body, typically at the edge of your shoulder. Measure from this point to the center of your nipple. Take the measurement for both the left and right sides, as they may differ slightly.
Neck Measurement
Place the measuring tape around your neck, just below the base of your skull. Hold it snugly but not too tightly. Record the measurement in inches or centimeters.
Body Length Measurement
Measure from the base of your neck, where the halter top strap would connect, down to your desired hemline. This measurement determines the length of the top.
Measurement |
Description |
Bust Measurement |
Circumference of the fullest part of the bust |
Underbust Measurement |
Circumference directly under the bust |
Strap Measurement |
Distance from shoulder to nipple |
Neck Measurement |
Circumference of the neck |
Body Length Measurement |
Length from base of neck to desired hemline |
Cutting the Fabric
Once you have chosen your fabric and created a pattern, it’s time to cut the fabric. Follow these steps for accurate cutting:
1. Prepare your workstation.
Ensure you have a clean and well-lit workspace. Gather all necessary tools, including sharp scissors, measuring tape, fabric pins, and a pattern.
2. Pin the pattern to the fabric.
Align the pattern pieces on the fabric, ensuring the grainlines match. Pin the pieces securely, leaving enough seam allowance around the edges.
3. Cut the fabric pieces.
Using sharp scissors, carefully cut out the fabric pieces along the pinned lines. Hold the scissors perpendicular to the fabric and avoid pulling or distorting the material. For curved edges, use smaller scissors or a curved blade to achieve precise cuts.
Tips for Cutting Fabric Precisely: |
Use a sharp rotary cutter with a new blade for clean cuts.
|
Cut on a firm surface with a dedicated cutting mat.
|
Hold the scissors perpendicular to the fabric and cut in one smooth stroke.
|
Trim away any excess fabric after cutting to reduce bulk.
|
Creating the Shoulders
To create the halter top’s shoulders, you’ll need the following materials:
- 2 pieces of fabric, each measuring 10 inches by 4 inches
- 1 piece of fabric, measuring 20 inches by 4 inches
- Sewing machine
- Thread
Once you have your materials, follow these steps:
- Fold each of the smaller pieces of fabric in half lengthwise, wrong sides together. Stitch the long edges together to create two loops. These will become the shoulder straps.
- Fold the larger piece of fabric in half lengthwise, wrong sides together. Stitch the long edges together to create a tube. This will become the top of the halter.
- Turn the top right side out. Insert the ends of the shoulder straps into the top of the halter, about 2 inches apart. Stitch the shoulder straps in place.
- Finishing the Shoulders
To finish the shoulders, you can either leave them raw or fold them over and stitch them down. If you choose to fold them over, fold the raw edges over by about 1/4 inch and topstitch them down. This will give the shoulders a more finished look.
Halter tops are a great way to show off your shoulders and back, and they’re also very easy to make. With a few simple steps, you can create a halter top that’s perfect for your unique style.
Attaching the Ties
Once you have finished stitching the top of the halter, it’s time to attach the ties. Each tie is simply a long strip of fabric that is folded in half and sewn onto the top of the halter. The ties will be used to secure the halter around your neck and back.
To make the ties, cut two strips of fabric that are 2 inches wide and 18 inches long. Fold each strip in half lengthwise and press the fold. Then, sew a straight stitch along the folded edge of each strip, close to the edge.
Now, you can attach the ties to the top of the halter. Fold the top edge of the halter down by 1 inch and press the fold. Then, pin the ties to the folded edge, with the raw edges of the ties lined up with the raw edges of the halter. Sew the ties in place using a straight stitch.
Fabric Length |
Fabric Width |
18 inches |
2 inches |
Once the ties are attached, you can try on the halter to make sure it fits properly. If the ties are too long, you can trim them to the desired length. If the ties are too short, you can simply add more fabric to the ends.
Finishing the Hem
Once your halter top is complete, it’s time to finish the hem. This will give your top a neat and polished look. There are a few different ways to hem a halter top, but the most common method is to use a blind stitch.
To blind stitch a hem, you will need a needle and thread that matches the color of your fabric. You will also need a pair of scissors and an iron.
Instructions:
1. Fold the hem up by about 1/2 inch and press it with an iron.
2. Fold the hem up again by 1/2 inch and press it again.
3. Thread your needle and knot the end of the thread.
4. Insert the needle into the hem, just below the fold. Take one small stitch and then bring the needle back up through the hem, just above the fold.
5. Repeat steps 4 and 5 all the way around the hem.
6. When you reach the end of the hem, knot the thread and trim the excess. To ensure a secure and invisible hem, follow these additional tips:
Tips |
Use a thread that matches the color of the fabric to make the stitches less visible. |
Take small, even stitches to create a neat and professional finish. |
Press the hem after each fold to make it crisp and flat. |
If you are having trouble seeing the stitches, use a magnifying glass or a lightbox. |
Adding Embellishments
Once the basic halter top is complete, you can add embellishments to personalize it. Here are a few ideas:
- Lace: Sew or glue lace trim along the neckline, straps, or hem.
- Beads or Sequins: Hand-stitch beads or sequins onto the top in a design or pattern.
- Fringe: Add fringe to the bottom of the top or the ends of the straps for a bohemian touch.
- Ribbons: Tie ribbons around the neckline, straps, or waist for a feminine detail.
- Embroidery: Embroider a design or initials onto the top using embroidery thread or yarn.
- Cutouts: Create cutouts in the top for a unique and edgy look.
- Studs or Spikes: Add studs or spikes to the top for a more edgy or punk-inspired aesthetic.
Other embellishment options include buttons, tassels, jewels, and feathers. Get creative and use your imagination to customize your halter top.
Embellishment Type |
Materials |
Techniques |
Lace Trim |
Lace trim, needle and thread |
Sew or glue lace along neckline, straps, or hem |
Beads or Sequins |
Beads or sequins, needle and thread |
Hand-stitch beads in design or pattern |
Troubleshooting Common Problems
Difficulty Tying the Halter
If you’re struggling to tie the halter behind your neck, try tying it loosely at the front and then twisting it around and securing it behind your neck. You can also use a hair clip or bobby pin to hold the tie in place.
The Top is Too Loose
If the halter top is too loose, you can adjust the ties to make it tighter. Start by shortening the tie that goes around your neck. If that’s not enough, you can also shorten the tie that goes around your waist.
The Top is Too Tight
If the halter top is too tight, you can adjust the ties to make it looser. Start by loosening the tie that goes around your waist. If that’s not enough, you can also loosen the tie that goes around your neck.
The Bust Darts Don’t Fit Properly
If the bust darts don’t fit properly, you can adjust them by moving them in or out. Start by pinning the darts in the desired location. Then, try on the top and adjust the pins until the darts fit snugly against your bust.
The Neckline is Too High or Low
If the neckline is too high or low, you can adjust the straps to change its position. To lower the neckline, shorten the straps. To raise the neckline, lengthen the straps.
The Top Doesn’t Stay in Place
If the halter top doesn’t stay in place, you can add some elastic to the straps. This will help to keep the top from slipping off your shoulders.
The Fabric is Too Sheer
If the fabric is too sheer, you can wear a camisole or bralette underneath the top.
The Top is Too Short or Long
If the top is too short or long, you can adjust the length by cutting or adding fabric. To shorten the top, cut off the excess fabric from the bottom hem. To lengthen the top, sew on a piece of coordinating fabric to the bottom hem.
Wearing and Styling Your Halter Top
Accessorizing Your Halter Top
Halter tops provide a unique opportunity to showcase your neckline and shoulders. Enhance your look with delicate necklaces or statement earrings that complement the neckline. For a more bohemian vibe, add a chunky necklace or beads. If you opt for earrings, choose drop or chandelier-style ones that draw attention to your décolletage.
Choosing the Right Bottoms
The bottom you pair with your halter top depends on the occasion and desired style. For a casual look, consider denim shorts or a flowy skirt. Dress it up with wide-leg pants or a maxi skirt. Avoid high-waisted bottoms, as they can cut off the halter neckline.
Layering Your Halter Top
Layer your halter top with a cardigan or jacket to extend its wearability. Choose a lightweight material for warmer weather or a thicker fabric for cooler temperatures. A cropped cardigan or denim jacket can add a touch of edginess, while a flowy kimono or blazer can create a more elegant look.
Playing with Patterns and Textures
Halter tops come in a wide range of patterns and textures. Experiment with different fabrics, such as lace, silk, or velvet, to create a unique style. If you have a solid-colored halter top, add visual interest by pairing it with patterned bottoms or a textured jacket.
Emphasizing Your Waist
To accentuate your waist, try tucking your halter top into high-waisted bottoms or adding a belt. A belt not only defines your waist but also adds a touch of sophistication to your outfit.
Dressy Occasions
Halter tops can be dressed up for formal events. Opt for a silky or lace halter top and pair it with a long skirt or tailored pants. Add some sparkle with jewelry and complete the look with heels or sandals.
Bohemian Style
For a bohemian vibe, choose a halter top with ethnic patterns or embellishments. Pair it with flowy pants or a long skirt. Accessorize with chunky jewelry, headbands, and sandals to complete the look.
Evening Glam
Create an evening-glam look by wearing a halter top made of a luxurious fabric, such as silk or velvet. Pair it with a long, flowing skirt or tailored pants. Accessorize with statement jewelry and heels for a polished and sophisticated ensemble.
Tips and Tricks
Tips |
Tricks |
Use a bra with clear straps or a bandeau bra. |
Conceal underarm hair with a razor or hair removal cream. |
Apply self-tanner to avoid tan lines. |
Wear a cardigan or jacket if the weather turns chilly. |
Accessorize with a hat or scarf to add a touch of flair. |
Experiment with different hairstyles to complement the halter neckline. |
Caring for Your Halter Top
To prolong the life and quality of your halter top, it’s crucial to follow these care instructions:
Washing
Hand wash the top gently in cold water using a mild detergent. Avoid using chlorine bleach or harsh detergents.
Drying
Lay the top flat to air dry. Avoid using a dryer, as high heat can damage the fabric.
Ironing
If necessary, iron the top using a low heat setting with a protective cloth over the fabric.
Storage
Store the halter top in a cool, dry place, preferably folded and placed in a drawer or hung neatly on a hanger.
Special Care for Delicate Fabrics
If your halter top is made from delicate fabrics such as silk, lace, or sheer materials, take extra precautions when washing and drying. Use a delicate cycle or hand wash, and avoid wringing or twisting the fabric.
Stain Removal
Attend to stains promptly by pre-treating them with a gentle stain remover. Test the stain remover on an inconspicuous area of the fabric first to ensure it does not cause discoloration or damage.
Stain Type |
Removal Method |
Blood |
Soak in cold water with salt, then wash as usual. |
Grass |
Rinse with cold water, then apply a mixture of baking soda and water. |
Oil |
Sprinkle baking soda or cornstarch on the stain, let sit for a few hours, then wash as usual. |
How To Make A Halter Top
A halter top is a type of top that is held up by straps that tie around the neck. There are many styles of halter tops, from simple to more elaborate designs.
To make a halter top, you can follow these steps:
- Measure the circumference of your neck and add 2 inches (5 cm) for overlap.
- Measure from the center of your neck to where you want the top to end. This measurement will determine the length of the straps.
- Cut two pieces of fabric that are the width of your neck measurement and the length of your strap measurement.
- Fold the fabric in half lengthwise and sew the raw edges together, leaving a small opening at the end for turning.
- Turn the fabric right side out and topstitch around the edges to close the opening.
- Fold the straps in half and sew the raw edges together, leaving a small opening at the end for turning.
- Turn the straps right side out and topstitch around the edges to close the opening.
- Thread the straps through the loops at the top of the fabric and tie them around your neck.
People Also Ask About How To Make A Halter Top
What kind of fabric is best for a halter top?
Lighter fabrics such as cotton, linen, or rayon are best for halter tops because they are breathable and will keep you cool in the summer.
What size hook and eye closure do I need for a halter top?
The size of the hook and eye closure you need will depend on the weight of the fabric and the size of the halter top. A general rule of thumb is to use a 1/2 inch (1.3 cm) hook and eye closure for lightweight fabrics and a 3/4 inch (2 cm) hook and eye closure for heavier fabrics.
How do I finish the edges of a halter top?
There are several ways to finish the edges of a halter top, including serging, hemming, or using bias tape.