
Delving into the intricate art of metal casting requires meticulous preparation, and one of the most crucial steps is crafting a mold that will shape the molten metal into your desired form. Whether you’re an experienced artisan or just starting your casting journey, understanding how to make a mold for metal casting is essential for successful outcomes. In this comprehensive guide, we will delve into the materials, techniques, and step-by-step instructions to help you create precise and durable molds that will elevate your casting endeavors to new heights.
Before embarking on the mold-making process, it’s important to gather the necessary materials. High-quality molding sand, such as silica sand or Zircon sand, is the foundation of a sturdy mold. A pattern, which serves as the shape model for your casting, will be used to create an impression in the sand. Furthermore, binder agents like bentonite or molasses will enhance the sand’s cohesive properties. Finally, a flask, typically made of wood or metal, will secure the sand and pattern during the molding process.
With the materials assembled, you can begin the mold-making process. First, prepare the molding sand by mixing it with the binder agent. The proper ratio of sand to binder depends on the specific materials you’re using, so refer to the manufacturer’s instructions for optimal results. Once the sand is ready, place the pattern on the base of the flask and pack the sand around it tightly. Use a jolting machine or hand-ramming techniques to remove any air pockets that could weaken the mold. Then, carefully separate the two halves of the flask, leaving a void in the shape of the pattern. This void will serve as the mold cavity for the molten metal to fill. The next step involves creating a sprue and gates, which are channels that allow the molten metal to enter and fill the mold cavity.
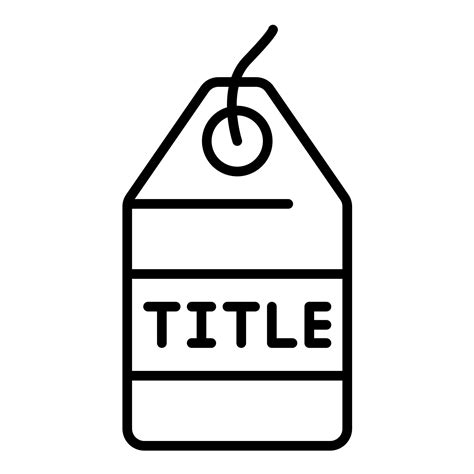
Preparing the Master Pattern
The Master Pattern is the initial physical representation of the object you intend to cast. It is essential to create a high-quality master pattern to ensure accurate and successful casting. The master pattern can be made from various materials like wood, metal, plastic, or wax. The choice of material depends on the desired details, durability, and ease of working.
Creating the Master Pattern from Wood
Wood is a readily available and workable material for creating master patterns. Here’s a step-by-step guide to carving a master pattern from wood:
- Select the wood: Choose a hardwood like oak, maple, or walnut for its durability and fine grain.
- Rough cut the shape: Use a band saw or scroll saw to cut the wood into an approximate shape of the final pattern.
- Shape the pattern: Use a variety of carving tools such as chisels, gouges, and rasps to refine the shape and details of the pattern.
- Sand and finish: Smooth the surface of the pattern using sandpaper or a sanding block. You can apply a sealant or finish to protect the wood.
|
Wood Type |
Advantages |
Disadvantages |
Hardwoods: Oak, Maple, Walnut |
Durable, fine grain |
Can be difficult to carve |
Softwoods: Pine, Fir |
Easy to carve |
Less durable, more prone to warping |
Plywood: Layered wood sheets |
Smooth surface, easy to work with |
Less durable, can delaminate |
Fabricating the Mould Box
Materials Required:
- Wood (pine or similar)
- Nails or screws
- Hammer or screwdriver
- Measuring tape or ruler
- Pencil or chalk
Steps:
1. Determine the dimensions of the mould box based on the size of the metal casting you want to make. The box should be large enough to accommodate the pattern and allow for a sufficient amount of molten metal to be poured in.
2. Cut the wood into pieces according to the required dimensions. Use nails or screws to assemble the pieces into a rectangular box with an open top. Ensure that the joints are secure and there are no gaps or leaks.
3. Line the inside of the mould box with a release agent, such as talcum powder or oil, to prevent the casting from sticking to the wood.
4. Place the pattern in the center of the mould box and secure it in place with clamps or weights.
5. Fill the mould box with the mould material (e.g., sand or plaster) and pack it tightly around the pattern. Use a trowel or spatula to smooth the surface and remove any air pockets.
6. Allow the mould material to cure or set before removing the pattern.
Creating the Mould Cavity
The most important step in making a mould for metal casting is creating the mould cavity—the space that will hold the molten metal to form the desired shape. A precise and well-crafted mould cavity will produce a clean and high-quality casting. The process requires careful attention to detail and consideration of the following factors:
Pattern Design
The pattern, which defines the shape of the final casting, must be designed with proper dimensions taking into account shrinkage that occurs during cooling. Two patterns, master and counterpart, are typically created. The master pattern forms the outer surface, while the counterpart creates the inner contours.
Moulding Materials
Moulding materials range from sand to plaster, each with its own properties and limitations. Sand moulds are commonly used due to their ease of packing and low cost, while plaster moulds offer higher precision and are suitable for smaller and more intricate castings.
Creating the Mould
To create the mould, the two patterns are placed into a flask—a frame that holds the sand or plaster. The master pattern is positioned first, and then covered with sand or plaster. The counterpart pattern is then placed onto the filled flask, creating a cavity that matches the shape of the pattern. The patterns are carefully removed, leaving behind the mould cavity for metal casting.
Moulding Material |
Properties |
Applications |
Sand |
Low cost, easy to pack, porous |
Large and simple castings |
Plaster |
High precision, smooth surface |
Smaller and intricate castings |
Setting Up the Mould
Now that you have your master mould, it’s time to create the actual mould that you’ll use for casting. This process is relatively simple, but there are a few things you need to keep in mind in order to get good results.
The first thing you need to do is create a parting line. This is the line where the two halves of the mould will meet. It’s important to make sure that the parting line is straight and level, or the two halves of the mould won’t fit together properly.
Once you have created the parting line, you need to build up the mould around the master. You can do this using a variety of materials, such as plaster, clay, or silicone. It’s important to use a material that is strong enough to withstand the casting process, but also flexible enough to allow you to remove the master mould later.
Once you have built up the mould, you need to let it dry thoroughly. This can take several hours or even days, depending on the material you used.
Step 4: Creating the mould
To create the mould, you will need to apply a release agent to the master mould. This will help to prevent the mould from sticking to the metal when you cast it. Once you have applied the release agent, you can begin to build up the mould around the master. You can use a variety of materials for this, such as plaster, clay, or silicone. It is important to use a material that is strong enough to withstand the casting process, but also flexible enough to allow you to remove the master mould later.
Once you have built up the mould, you need to let it dry thoroughly. This can take several hours or even days, depending on the material you used. Once the mould is dry, you can remove the master mould and begin casting.
Here is a table summarizing the steps involved in creating a mould for metal casting:
Step |
Description |
1 |
Create a parting line. |
2 |
Build up the mould around the master. |
3 |
Let the mould dry thoroughly. |
4 |
Remove the master mould. |
Mixing and Pouring the Mould Material
Preparing the Materials
Gather the following materials:
- Mould material (e.g., plaster, silicone, sand)
- Mixing container
- Water
- Stirring tool
- Measuring cups and spoons
Mixing the Mould Material
Follow the manufacturer’s instructions for mixing the mould material. Generally, this involves adding water to the powder in a specific ratio and stirring thoroughly until a smooth, lump-free consistency is achieved. The viscosity of the mixture should be similar to that of pancake batter.
Pouring the Mould Material
- Prepare the casting flask: Apply release agent to the interior of the casting flask and allow it to dry. This will help in releasing the mould after it sets.
- Pour the mould material: Slowly and carefully pour the mixed mould material into the casting flask. Fill the flask to the top, avoiding any air bubbles.
- Tamp the mould: Gently tap the casting flask on a table or work surface to remove any air pockets and ensure proper compaction.
- Level the mould: Smooth the top of the mould using a straight edge or trowel to create a flat surface for casting.
- Degas the mould (optional): To minimize air bubbles in the final cast, degas the mould by placing it in a vacuum chamber or applying a vacuum pump. This process removes any entrapped air, resulting in a cleaner and more accurate casting.
Setting Time
Allow the mould material to set according to the manufacturer’s instructions. This can take several hours or even days, depending on the type of material used. Once fully set, the mould can be removed from the casting flask and used for metal casting.
Curing the Mould
The curing process is crucial for ensuring the mould’s stability and strength before casting metal. Here are the detailed steps to follow:
1. Initial Cure at Room Temperature
Leave the mould undisturbed at room temperature for 24-48 hours. This allows the plaster or sand binder to set and gain initial strength.
2. Heat Curing
Place the mould in an oven or on a hot plate. Gradually increase the temperature according to the manufacturer’s instructions, typically 10-20°C per hour. Maintain the target temperature (usually around 200-400°C) for several hours.
3. Cool Slowly
After heat curing, allow the mould to cool slowly in the oven or on the hot plate. This prevents rapid cooling that could cause cracking or warping.
4. Remove Pattern
Once the mould is cool, carefully remove the pattern. If it is still stuck, gently tap it with a mallet or use a release agent to loosen it.
5. Dry the Mould
Place the mould in a warm, dry place for further drying. This removes any remaining moisture and ensures the mould is dry enough for casting.
6. Inspect and Prepare the Mould
Inspect the mould for any cracks or imperfections. If necessary, repair them with a suitable material such as epoxy or plaster. Apply a parting agent or lubricant to the mould surfaces to prevent the molten metal from sticking.
Curing Method |
Temperature Range |
Duration |
Initial (room temperature) |
Ambient |
24-48 hours |
Heat curing (oven/hot plate) |
200-400°C |
Several hours |
Cooling |
Gradual |
As per manufacturer’s instructions |
Removing the Master Pattern
Once the plaster has completely set, it’s time to remove the master pattern. This must be done carefully to avoid damaging either the mold or the pattern. Here are the steps:
-
Gently tap around the edges of the mold. This will help to loosen the plaster’s grip on the pattern.
-
Use a thin knife or spatula to carefully pry the pattern away from the mold. Start at one corner and work your way around, being careful not to apply too much pressure.
-
Once the pattern is loose, gently lift it out of the mold.
-
Inspect the mold to make sure there are no cracks or damage. If there are any, you can repair them with plaster of Paris.
-
Allow the mold to dry completely before using it for casting.
**Tips for Removing the Master Pattern:**
-
Use a sharp knife or spatula to make clean cuts.
-
Be patient and take your time to avoid damaging the mold or pattern.
-
If the pattern is particularly difficult to remove, you can try using a heat gun to soften the plaster slightly.
-
Once the pattern is removed, be sure to clean the mold thoroughly to remove any remaining plaster or debris.
-
Store the mold in a dry place until you are ready to use it.
Baking the Mould
The next step in the metal casting process is to bake the mould. This process removes any moisture from the mould and hardens the material, making it strong enough to withstand the molten metal being poured into it.
The baking process can be done in a variety of ways, but the most common method is to place the mould in an oven and heat it to a specific temperature for a set period of time. The temperature and time will depend on the type of mould material being used.
Here are the steps on how to bake the mould:
- Place the mould in an oven that has been preheated to the desired temperature.
- Bake the mould for two hours.
- Turn off the oven and let the mould cool slowly inside.
- Once the mould is cool, remove it from the oven and let it air dry completely.
It is important to follow the baking instructions carefully to ensure that the mould is properly cured. If the mould is not baked long enough, it may not be strong enough to withstand the molten metal and could break, resulting in a failed casting.
The following table provides a summary of the baking temperatures and times for different types of mould materials:
Material |
Temperature |
Time |
Plaster of Paris |
120-150°C |
2 hours |
Ceramics |
900-1000°C |
6 hours |
Metal |
1200-1400°C |
4 hours |
Pouring the Molten Metal
After the mold is prepared, the next step is to pour the molten metal into the mold. This step should be carried out with caution and care to ensure that the molten metal does not spill or come into contact with anything that could cause a fire or injury.
Here are the steps for pouring the molten metal:
- Gather your materials. You will need a ladle or crucible, tongs, safety glasses, gloves, and a heat-resistant surface.
- Heat the molten metal. Heat the metal in a furnace or crucible until it is liquid.
- Prepare the mold. Check that the mold is secure and ready to receive the molten metal.
- Pour the molten metal into the mold. Slowly pour the molten metal into the mold, avoiding spills or splashes.
- Fill the mold completely. Continue pouring the molten metal until the mold is completely filled.
- Allow the metal to cool. Allow the metal to cool slowly to prevent cracking or warping.
- Remove the casting from the mold. Once the metal has cooled, remove the casting from the mold.
- Clean the casting. Clean the casting to remove any slag or debris.
- Inspect the casting. Inspect the casting for any defects or imperfections.
**Tips for Pouring Molten Metal:**
- Wear appropriate safety gear. Always wear safety glasses, gloves, and heat-resistant clothing when pouring molten metal.
- Have a fire extinguisher nearby. In case of a fire, having a fire extinguisher nearby can help prevent serious injury or damage.
- Pour slowly and carefully. Avoid pouring the molten metal too quickly or splashing it around.
- Allow the metal to cool slowly. Cooling the metal too quickly can cause it to crack or warp.
- Inspect the casting thoroughly. Before using the casting, inspect it for any defects or imperfections that could affect its performance.
Cooling and Solidifying the Casting
Once the molten metal has been poured into the mold and cooled, it will begin to solidify. The rate at which the metal solidifies will depend on a number of factors, including the type of metal, the thickness of the casting, and the temperature of the mold.
In general, thicker castings will take longer to cool and solidify than thinner castings. This is because the heat from the molten metal has to travel a greater distance to reach the surface of the mold.
The temperature of the mold will also affect the rate at which the casting solidifies. Molds that are at a higher temperature will cause the metal to cool and solidify more slowly than molds that are at a lower temperature.
The cooling and solidification process can be controlled by using a variety of techniques. These techniques include:
Technique |
Description |
Chilling |
Chilling is a process of rapidly cooling the casting by pouring cold water or air over it. |
Annealing |
Annealing is a process of heating the casting to a high temperature and then slowly cooling it. |
Tempering |
Tempering is a process of heating the casting to a high temperature and then cooling it quickly. |
By using these techniques, it is possible to control the properties of the casting, such as its hardness, strength, and toughness.
How to Make a Mould for Metal Casting
Creating a mould for metal casting is a crucial step in the metalworking process. A well-made mould ensures that the molten metal fills the desired shape and solidifies into a precise and functional component. Here’s a detailed guide on how to make a mould for metal casting:
Materials you’ll need:
- A pattern or master model of the desired casting
- Moulding sand or investment powder
- Moulding flask
- Mould release agent
- Sprue and riser pins
- Gates and runners
People Also Ask:
What are the different types of moulds used in metal casting?
There are two main types of moulds used in metal casting: sand moulds and investment moulds. Sand moulds are made from a mixture of sand, clay, and water, while investment moulds are made from a ceramic material.
What is the purpose of a sprue and riser in metal casting?
A sprue is a channel through which the molten metal enters the mould, while a riser is a reservoir that helps to feed molten metal into the mould as it solidifies and shrinks.
How do you ensure that the molten metal completely fills the mould?
To ensure that the molten metal completely fills the mould, it’s important to use a gating system that allows the metal to flow smoothly into the mould cavity. Additionally, using a vacuum or centrifugal casting process can help to draw the molten metal into the mould.