
Delve into the captivating realm of bronze, an enigmatic alloy that has captivated artisans and metalworkers for centuries. Its allure lies in its exceptional durability, malleability, and the captivating hues it imparts, ranging from gleaming gold to rich cocoa. Casting bronze, an ancient art form, empowers you to transform molten metal into exquisite sculptures, intricate jewelry, and enduring objects that transcend time. Embark on a journey of discovery as we unravel the secrets of bronze casting, empowering you to create captivating works of art that will endure for generations to come. 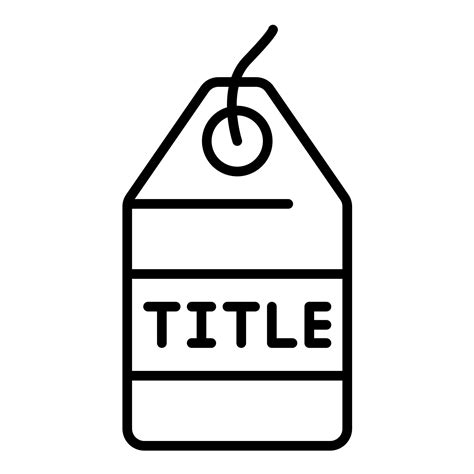
To embark on this enchanting journey, you will require a dedicated workspace, essential tools, and an unwavering commitment to safety. Your workspace should boast adequate ventilation, a sturdy workbench, and ample storage for materials. Invest in high-quality tools such as crucibles, tongs, and protective gear to ensure a seamless and secure casting experience. Prioritizing safety is paramount; always wear appropriate protective gear, including gloves, safety glasses, and a respirator, to safeguard yourself from potential hazards. With your workspace meticulously prepared and safety measures in place, you are now poised to unravel the secrets of bronze casting.
The essence of bronze casting lies in the harmonious fusion of copper and tin. By carefully manipulating the proportions of these metals, you can tailor the resulting alloy to suit your specific artistic vision. Experiment with different ratios to achieve a spectrum of hues, from the warm glow of gold to the deep patina of chocolate. The casting process itself is a delicate dance of heat and precision. Molten metal, brimming with incandescent energy, is poured into meticulously crafted molds, allowing it to solidify and take on the intricate shapes you desire. Through this transformative process, you will witness the birth of exquisite bronze sculptures, shimmering jewelry, and functional objects imbued with timeless beauty and durability.
The Metallurgy of Bronze
Materials and Proportions
Bronze is an alloy primarily composed of copper and tin. The ratio of these metals determines the properties and applications of the bronze. Traditional bronze is commonly made with 88% copper and 12% tin, known as “88/12 bronze.” Bronze can also be alloyed with other metals, such as aluminum, nickel, manganese, or silicon, to enhance specific characteristics, such as strength, corrosion resistance, or castability.
The discovery of bronze marked a significant advancement in human civilization, enabling the creation of tools, weapons, and decorative objects with superior strength and durability compared to their stone and wood predecessors. Bronze’s unique properties, including its high strength, corrosion resistance, and ease of casting, have made it a vital material in various industries and applications over the centuries.
Bronze is created through a process called smelting, which involves heating the copper and tin ores in a furnace to separate the metals from the impurities. The molten metals are then poured into molds to create desired shapes. The cooling and solidification process results in the formation of bronze, which can be further worked and shaped through casting, forging, or rolling techniques.
The development and widespread use of bronze during the Bronze Age ushered in a period of technological advancements and cultural transformations. It led to the emergence of specialized craftspeople and artisans, who played a crucial role in shaping societies, promoting trade, and facilitating cultural exchanges.
Properties of Bronze
Bronze exhibits a range of properties that make it suitable for various applications. It is harder and stronger than copper and has excellent wear resistance. Bronze is also corrosion-resistant, making it ideal for marine and outdoor use. Moreover, it has good acoustic properties, making it suitable for musical instruments and bells.
Applications of Bronze
Bronze has been extensively used in numerous applications throughout history. It was primarily employed for creating tools, weapons, armor, and sculptures in ancient times. In modern times, bronze is widely utilized in industrial machinery, architectural components, marine fittings, musical instruments, and artistic castings.
Property |
Value |
Density |
8.96 g/cm³ |
Melting point |
933–1,083 °C (1,711–1,983 °F) |
Tensile strength |
300–700 MPa |
Hardness |
Brinell 120–250 |
Corrosion resistance |
Excellent |
Alloying Copper and Tin
To create bronze, copper and tin are combined in a process called alloying. The proportions of each metal in the alloy determine the specific properties of the resulting bronze. Typically, bronze is composed of approximately 88% copper and 12% tin, although variations in these percentages can produce different alloys with unique characteristics.
The process of alloying copper and tin involves heating the metals together until they melt and form a homogeneous mixture. This molten alloy is then poured into a mold to create the desired shape. As the alloy cools, it solidifies and forms bronze.
Refining the Alloy
Once the copper and tin have been alloyed, the resulting mixture may contain impurities or unwanted elements. To remove these impurities, the alloy can be refined through a process called smelting. In smelting, the alloy is heated in the presence of a flux, which is a chemical substance that reacts with the impurities and causes them to separate from the alloy. The molten alloy is then poured off, leaving behind the impurities in the slag.
The refining process can be repeated multiple times to further purify the alloy. The number of times the alloy is refined will depend on the desired level of purity.
Casting Bronze Objects
Casting bronze objects is a complex but rewarding process. The first step is to create a mold of the object you want to cast. This can be done using a variety of materials, including wax, rubber, or plaster.
Once the mold is made, it is filled with molten bronze. The bronze is then allowed to cool and solidify, and the mold is removed to reveal the finished object.
There are many different techniques for casting bronze objects, but the most common is the lost-wax method. In this method, a wax model of the object is created and then covered with a layer of plaster. The plaster is then heated until the wax melts and flows out, leaving a hollow mold. The mold is then filled with molten bronze, and the bronze is allowed to cool and solidify. Once the bronze has cooled, the plaster mold is broken away to reveal the finished object.
Lost-Wax Casting Process
The lost-wax casting process is a complex one that requires a great deal of skill and experience. The following are the steps involved in the lost-wax casting process:
- Create a wax model: The first step is to create a wax model of the object you want to cast. This can be done by carving the wax or by using a mold.
- Create a mold: Once the wax model is created, it is covered with a layer of plaster. The plaster is then heated until the wax melts and flows out, leaving a hollow mold.
- Fill the mold with molten bronze: The mold is then filled with molten bronze, and the bronze is allowed to cool and solidify.
- Break away the plaster mold: Once the bronze has cooled, the plaster mold is broken away to reveal the finished object.
The lost-wax casting process is a versatile one that can be used to create a wide variety of bronze objects. From small pieces of jewelry to large sculptures, the lost-wax casting process can be used to create beautiful and unique works of art.
Lost-Wax Casting Techniques
Lost-wax casting, also known as investment casting, is an ancient technique used to create bronze sculptures and other metal objects. It involves creating a wax model of the desired object, which is then covered in a refractory material to create a mold. The wax is then melted out, leaving a hollow cavity that is filled with molten bronze.
The lost-wax casting process typically involves the following steps:
1. Creating a Wax Model:
The first step is to create a wax model of the desired object. This can be done by carving the wax, using a mold, or casting it from another model.
2. Building the Mold:
Once the wax model is complete, it is covered in a refractory material to create a mold. The mold is made of a material that can withstand the heat of the molten bronze, such as plaster or ceramic.
3. Removing the Wax:
The wax is then melted out of the mold, leaving a hollow cavity. This can be done by heating the mold in a kiln or by using a hot water bath.
4. Casting the Bronze:
Once the wax has been removed, the mold is filled with molten bronze. The bronze is poured into the mold through a sprue, which is a small hole in the top of the mold. The bronze fills the cavity and solidifies, creating a metal replica of the wax model.
Here are some of the advantages of lost-wax casting:
Advantages |
Can produce highly detailed and intricate objects |
Can be used to cast objects of various sizes and shapes |
Is a relatively precise casting technique |
Allows for multiple castings from a single mold |
The Art of Bronze Sculpture
Materials for Bronze Sculpture
Bronze is an alloy of copper and tin, with other metals sometimes added to enhance its properties and give it a distinctive color. The most common type of bronze used for sculpture is 85% copper and 5% tin, with the remaining 10% being a mix of nickel, aluminum, manganese, or zinc.
Creating a Bronze Sculpture
The process of creating a bronze sculpture involves several steps, including modeling, casting, and finishing.
lost-wax casting
Lost-wax casting is a technique of casting metal sculptures using a wax model. The model is made from wax and then covered with a mold. The mold is then heated until the wax melts and runs out, leaving a cavity in the mold that is the same shape as the original model. Molten metal is then poured into the cavity, and once it cools and solidifies, the mold is broken away, leaving behind the metal sculpture.
Modern Techniques for Creating Bronze Sculpture
In addition to traditional techniques, there are several modern techniques that can be used to create bronze sculptures. These techniques include sand casting, centrifugal casting, and electroforming.
Finishing Bronze Sculpture
Once the bronze sculpture has been cast, it needs to be finished. The finishing process can involve sanding, polishing, and patination. Sanding smooths the surface of the sculpture, while polishing gives it a lustrous finish. Patination is the process of applying a chemical solution to the sculpture to change its color.
There are many different types of patinas that can be applied to bronze sculptures, and the type of patina used will depend on the desired effect. Some of the most common types of patinas include:
Patina |
Color |
Natural |
Brownish-black |
Oxidized |
Deep black |
Green |
Greenish-blue |
Red |
Reddish-brown |
Bleached |
Pale yellowish-white |
The Role of Bronze in History
For thousands of years, bronze played a pivotal role in human history. Its unique properties made it an indispensable material for civilizations around the globe, shaping technological advancements and influencing cultural development.
From Tools to Weapons
Bronze’s exceptional strength and durability made it an ideal material for a wide range of tools and weapons. Bronze weapons, such as swords, spears, and axes, gave armies a significant advantage in combat. Bronze tools, including axes, hammers, and chisels, enabled civilizations to build complex structures and develop sophisticated crafts.
Bronze Age Civilizations
The development of bronze metallurgy marked the beginning of the Bronze Age in different regions of the world. These civilizations, such as the Babylonians, Egyptians, and Indus Valley civilization, experienced a period of rapid technological and cultural advancement spurred by bronze’s availability.
Cultural Symbolism
Beyond its practical applications, bronze also held deep cultural significance. In many ancient civilizations, bronze objects were associated with power, wealth, and prestige. Bronze statues, figurines, and jewelry were often used to depict gods, rulers, and other important figures.
Alloy Composition and Properties
Bronze is an alloy composed primarily of copper and tin. The ratio of copper to tin in the alloy determines its specific properties. High-tin bronze is harder and more brittle, while low-tin bronze is softer and more ductile.
Bronze Composition |
Properties |
High-tin (15-20% tin) |
Hard, brittle, suitable for weapons |
Medium-tin (10-12% tin) |
Strong, durable, suitable for tools |
Low-tin (5-8% tin) |
Soft, ductile, suitable for castings |
Bronze as a Decorative Material
Bronze has been used for centuries to create decorative objects, from sculptures to furniture. Its rich, warm color and durability make it an ideal material for both indoor and outdoor use.
Bronze Sculptures
Bronze sculptures are some of the most iconic and recognizable works of art in the world. From the ancient Greek statue of Zeus to the modern works of Henry Moore, bronze sculptures have captured the imagination of people for centuries.
Bronze Furniture
Bronze furniture is also highly prized for its beauty and durability. Bronze tables, chairs, and other pieces of furniture can add a touch of luxury and elegance to any room.
Bronze Mirrors
Bronze mirrors have been used for centuries to reflect one’s image. They are often decorated with intricate designs and can be found in a variety of shapes and sizes.
Bronze Candlesticks
Bronze candlesticks are a beautiful and functional way to add light to any room. They are available in a variety of styles, from simple to ornate.
Bronze Vases
Bronze vases are a popular choice for displaying flowers. They are available in a variety of shapes and sizes, and can be found in both traditional and contemporary designs.
Bronze Plaques
Bronze plaques are often used to commemorate special events or to honor individuals. They are typically inscribed with text or images, and can be mounted on walls or other surfaces.
| Bronze Plaques |
| ———– |
| Use | Commemorate special events or honor individuals |
| Materials | Bronze |
| Features | Typically inscribed with text or images |
| Mounting | Mounted on walls or other surfaces |
Bronze in Architecture and Engineering
Bronze is an alloy of copper and tin, and is known for its strength and durability. Bronze has been used in architecture and engineering for centuries, from the ancient Greeks to the present day.
Bronze in Ancient Architecture
Bronze was used for weapons, tools, and armor in the ancient world. It was also used to make statues, sculptures, and decorative objects. Some of the most famous ancient bronze sculptures include the Statue of Zeus at Olympia and the Winged Victory of Samothrace.
Bronze in Modern Architecture
Bronze continues to be used in modern architecture and engineering, but it is now more often used for decorative purposes. Bronze can be used to make doors, windows, railings, and other architectural elements. It is also used for sculptures and other works of art.
Engineering Applications of Bronze
Bronze is also used in a variety of engineering applications. It is used to make electrical contacts, bearings, and other components. Bronze is also used in the automotive and shipbuilding industries.
Advantages of Bronze in Architecture and Engineering
There are several advantages to using bronze in architecture and engineering:
- Strength and durability
- Resistance to corrosion
- Low maintenance
- Aesthetic appeal
Disadvantages of Bronze in Architecture and Engineering
There are also some disadvantages to using bronze in architecture and engineering:
- High cost
- Weight
- Can be difficult to work with
Bronze Alloys
There are many different alloys of bronze, each with its own unique properties. The most common type of bronze is copper-tin bronze, which contains between 88% and 92% copper and 8% to 12% tin.
Alloy |
Composition |
Uses |
Copper-tin bronze |
88-92% copper, 8-12% tin |
General purpose bronze, used for castings, statues, and other applications |
Copper-aluminum bronze |
80-90% copper, 10-20% aluminum |
High strength and hardness, used for marine applications, springs, and electrical contacts |
Copper-silicon bronze |
92-98% copper, 3-8% silicon |
High strength and corrosion resistance, used for springs, electrical contacts, and chemical processing equipment |
Modern Applications of Bronze
Bronze is an alloy composed primarily of copper and tin. It has been used for centuries in a wide variety of applications, both decorative and functional. In recent years, bronze has seen a resurgence in popularity due to its unique properties. It is strong, durable, and corrosion-resistant, and it has a beautiful, warm color that makes it ideal for use in both indoor and outdoor applications.
Here are some of the most common modern applications of bronze:
Sculptures and art objects
Bronze is a popular choice for sculptures and art objects because of its strength, durability, and ability to capture fine detail. Some of the most famous bronze sculptures in the world include the Statue of Liberty, the Winged Victory of Samothrace, and the Discobolus.
Building materials
Bronze is used in a variety of building materials, including roofing, siding, and window frames. It is also used in interior design elements, such as doorknobs, light fixtures, and furniture.
Musical instruments
Bronze is used in the manufacture of a variety of musical instruments, including cymbals, gongs, and trumpets. It is also used in the strings of some guitars and violins.
Automotive parts
Bronze is used in a variety of automotive parts, including bearings, bushings, and gears. It is also used in brake pads and clutch plates.
Electrical components
Bronze is used in a variety of electrical components, including connectors, switches, and contacts. It is also used in the windings of electric motors.
Jewelry
Bronze is used in a variety of jewelry, including rings, bracelets, and necklaces. It is also used in the manufacture of watches and other timepieces.
Medals and awards
Bronze is used in the manufacture of medals and awards, such as the Olympic medals and the Nobel Prize medals.
Other applications
Bronze is also used in a variety of other applications, including:
Bearing bronze is used for bearings and bushings, offering excellent wear resistance and conformability. Here are some of the chemical composition details of bearing bronze:
Element |
Composition |
Copper |
75-95% |
Tin |
5-15% |
Nickel |
2-5% |
Lead |
0-5% |
Antimony |
0-1% |
Caring for and Preserving Bronze
Bronze is a durable, low-maintenance material that can last for centuries with proper care. Here are some tips for keeping your bronze items looking their best:
Cleaning Bronze
To remove dirt and dust, wipe down bronze objects with a soft, damp cloth. For more stubborn dirt, use a mild dish soap and water solution. Rinse thoroughly and dry with a clean cloth.
Polishing Bronze
Over time, bronze can develop a patina, a natural protective coating that can give it a unique character. If you prefer a brighter finish, you can polish bronze with a soft cloth and a mild metal polish. Test the polish on an inconspicuous area first to ensure it does not damage the bronze.
Protecting Bronze from Wear and Tear
To prevent scratches and dents, store bronze items in a cool, dry place away from direct sunlight. Avoid using harsh chemicals or abrasive cleaners on bronze.
Repairing Bronze
If your bronze object becomes damaged, it can be repaired by a professional metalworker. Depending on the extent of the damage, the repair may involve welding, brazing, or casting.
Environmental Considerations
Bronze is a corrosion-resistant material, but it can still be affected by certain environmental factors. Avoid exposing bronze to high levels of moisture, salt, or pollution.
Table: Environmental Factors and Bronze Corrosion
Environmental Factor |
Effect on Bronze |
Moisture |
Can cause pitting and corrosion |
Salt |
Can cause accelerated corrosion |
Pollution |
Can form a dull patina that makes bronze appear tarnished |
Storage Considerations
To prevent damage during storage, wrap bronze objects in acid-free tissue paper and store them in a cool, dry place. Avoid using plastic or rubber containers, as these can trap moisture and promote corrosion.
Display Considerations
When displaying bronze objects, choose a location that is protected from direct sunlight, heat, and moisture. Use a soft cloth or dusting brush to remove dust and fingerprints regularly.
Regular Maintenance
To maintain the beauty of your bronze objects, inspect them regularly for signs of wear or damage. Clean and polish them as needed to prevent corrosion and preserve their original appearance.
How To Create Bronze
Bronze is an alloy, which is a metal made by combining two or more different metals. Bronze is made by combining copper and tin. The proportions of copper and tin in bronze can vary, but the most common type of bronze is 88% copper and 12% tin. Bronze is a strong and durable metal that has been used for centuries to make a variety of objects, including weapons, armor, and sculptures.
To create bronze, the first step is to melt the copper. This can be done in a furnace or a crucible. Once the copper is melted, the tin is added. The copper and tin are then stirred together until they are completely mixed. The molten bronze is then poured into a mold. The mold is made of a material that will not react with the bronze, such as sand or plaster.
Once the bronze has cooled, it can be removed from the mold. The bronze object can then be finished by polishing, sanding, or hammering. Bronze is a versatile metal that can be used to create a wide variety of objects. It is a strong and durable metal that can last for centuries.
People Also Ask
What is the difference between bronze and brass?
Bronze is an alloy of copper and tin, while brass is an alloy of copper and zinc. Bronze is stronger and more durable than brass, but brass is more malleable and easier to work with.
What are some of the uses of bronze?
Bronze has been used for centuries to make a variety of objects, including weapons, armor, sculptures, and musical instruments. Bronze is also used in modern applications, such as bearings, gears, and springs.
How can I tell if an object is made of bronze?
Bronze is a reddish-brown metal. It is harder than steel, but softer than iron. Bronze objects often have a green patina, which is caused by the oxidation of the copper in the bronze.