
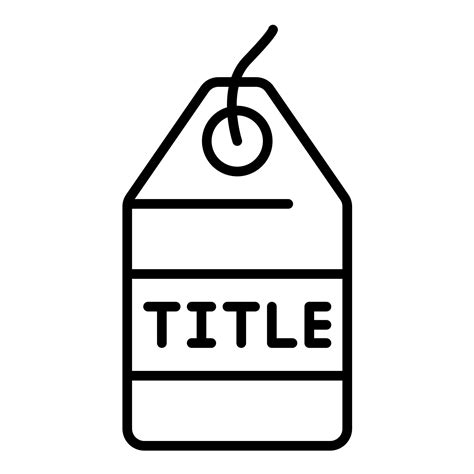
Holes in plastic can be a nuisance. They can let in water, dust, and insects. They can also make your plastic items look unsightly. Fortunately, repairing a hole in plastic is a relatively easy task. With the right materials and a little bit of time, you can fix that hole and restore your plastic item to its former glory.
The first step is to clean the area around the hole. This will help the adhesive bond better. Once the area is clean, you can apply the adhesive. There are a variety of adhesives that can be used to repair plastic, so choose one that is appropriate for the type of plastic you are working with. Once the adhesive is applied, you can press the two pieces of plastic together and hold them in place until the adhesive has dried. Depending on the type of adhesive you are using, this may take anywhere from a few minutes to a few hours.
Once the adhesive has dried, the hole will be repaired. You can now use your plastic item as normal. If the hole is in a visible location, you may want to sand the area around the repair to make it less noticeable. You can also paint the area to match the rest of the plastic item.
Identifying the Type of Plastic
Recognizing the specific type of plastic you’re working with is crucial for implementing the most effective repair strategy. Identifying the plastic type enables you to select the appropriate adhesive, filler, or welding technique. Here are some identifiers that can help you distinguish between common plastic types:
Physical Properties
Observe the plastic’s appearance, texture, and flexibility. For instance, polyethylene (PE) is typically milky or translucent, while polypropylene (PP) has a harder, more rigid texture. Polyvinyl chloride (PVC) is known for its firm and durable nature, while polyethylene terephthalate (PET) is often associated with food containers and beverage bottles.
Melting Behavior
Heat a small, inconspicuous area of the plastic using a lighter or heat gun. Different plastics exhibit distinct melting behaviors that provide clues to their identity. For example, PE melts smoothly and easily, while PP melts with a higher viscosity and forms long, stringy strands. PVC melts slowly with a pungent odor, and PET curls and shrinks.
Density
Compare the weight of the plastic to water by placing a piece in a container of water. Plastics like PE and PP float, whereas denser plastics such as PVC and PET sink. This information can help you narrow down the possible material types.
Plastic Type |
Physical Properties |
Melting Behavior |
Density |
Polyethylene (PE) |
Milky or translucent, soft and flexible |
Melts smoothly |
Floats in water |
Polypropylene (PP) |
Harder, more rigid texture |
Melts with high viscosity, forming strands |
Floats in water |
Polyvinyl Chloride (PVC) |
Firm and durable |
Melts slowly with a pungent odor |
Sinks in water |
Polyethylene Terephthalate (PET) |
Clear or colored, stiff and flexible |
Curls and shrinks when heated |
Sinks in water |
Gathering the Necessary Materials
To ensure a successful plastic repair, it’s crucial to gather the appropriate materials. Here’s a detailed list of everything you’ll need:
Plastic Welders
Heat Gun: A heat gun, also known as a hot air gun, is the primary tool for welding plastic. It emits hot air that softens the plastic, allowing it to be manipulated and fused together.
Welding Rod: Welding rods are made of plastic and come in various forms, such as rods, sticks, or tubes. They’re used as filler material to bridge gaps and create a strong bond.
Smoothing Tool: A smoothing tool, typically a small spatula or spoon-shaped object, is used to smooth and shape the molten plastic after welding.
Abrasive Paper: Abrasive paper, such as sandpaper or emery paper, is used to smoothen the repaired area and remove any excess plastic.
Safety Gear: Working with heat requires safety gear such as gloves, safety glasses, and a respirator or dust mask to protect yourself from fumes and debris.
Adhesives
Plastic Adhesives: Plastic adhesives come in various types, including epoxies, super glues, and contact cements. They’re used to bond plastic pieces or fill small gaps without the need for welding.
Other Tools
Cleaning Supplies: Isopropyl alcohol or acetone is used to clean the plastic surfaces before bonding.
Clamps: Clamps are helpful for holding plastic pieces in place while the adhesive sets or the plastic cools after welding.
Cleaning and Preparing the Area
1. Remove Loose Debris
Use a sharp knife or razor blade to carefully remove any loose plastic shards or debris around the hole. Be cautious not to enlarge the hole further.
2. Clean the Area with Alcohol
Dampen a clean cloth or cotton swab with rubbing alcohol. Gently wipe the surface around the hole to remove dirt, grease, or residue that could interfere with the repair.
3. Dry the Surface
Allow the alcohol to evaporate completely. You can speed up the drying process using a hair dryer on a low heat setting or by gently dabbing the area with a clean paper towel. Ensure the surface is completely dry before proceeding to the next step.
4. Sand the Edges (Optional)
(For large or uneven holes only) If the edges of the hole are rough or uneven, carefully sand them using fine-grit sandpaper (220+). Sanding the edges will create a smoother surface for the patch to adhere to.
5. Mark the Repair Area
If you’re using a patch or mesh to cover the hole, mark its outline around the hole using a pencil or marker. This will help you align the patch precisely during application.
Applying Adhesive to the Edges
To ensure a strong bond between the patch and the plastic, it’s crucial to apply adhesive properly to the edges of the hole and the patch material. Here are detailed steps:
Thoroughly Clean the Edges
Before applying adhesive, make sure the edges of the hole and the patch are free from dirt, grease, or any other contaminants that could weaken the bond. Use a clean cloth and rubbing alcohol to thoroughly wipe down both surfaces.
Apply Adhesive to the Edges of the Hole
Using a precision applicator or a small brush, apply a thin layer of the chosen adhesive along the edges of the hole. Choose an adhesive that is suitable for the type of plastic and provides strong adhesion. Allow the adhesive to set for a few minutes before applying the patch.
Apply Adhesive to the Patch Material
Next, apply a thin layer of adhesive to the edges of the patch material. Make sure to align the edges of the patch with the edges of the hole, ensuring a precise fit. Allow the adhesive to set for a few minutes before placing the patch over the hole.
Press the Patch into Place
Carefully align the patch over the hole and press down firmly around the edges to ensure a good contact between the adhesive surfaces. Use a rolling pin or a flat, heavy object to evenly distribute pressure and remove any air bubbles. Hold the patch in place for several minutes, following the manufacturer’s recommended curing time, to allow the adhesive to fully set.
Inserting a Patch or Mesh
For larger holes or tears, using a patch or mesh can provide additional reinforcement and durability to the repair. Here’s a step-by-step guide for inserting a patch or mesh:
1. Prepare the Surface
Clean and dry the area around the hole. Sand or roughen the edges of the hole slightly to create a better surface for adhesion.
2. Cut the Patch or Mesh
Cut a patch or mesh that is approximately 2 inches larger than the hole on all sides. Choose a patch or mesh material that is compatible with the type of plastic being repaired.
3. Apply Adhesive
Apply a thin layer of adhesive to the back of the patch or mesh. Use an adhesive that is suitable for the type of plastic being repaired, such as epoxy or plastic adhesive.
4. Insert the Patch or Mesh
Carefully insert the patch or mesh into the hole and align it properly. Press down firmly to ensure good contact between the adhesive and the surface.
5. Reinforce the Patch or Mesh
To reinforce the patch or mesh and prevent it from tearing, apply additional adhesive around the edges. You can also use clamps or weights to hold the patch in place while the adhesive dries.
Tip: For larger holes or tears, you can use multiple layers of mesh or patches for added strength.
Adhesive Type |
Plastic Type |
Epoxy |
Most plastics |
Plastic Adhesive |
PVC, ABS, Polycarbonate |
Super Glue |
Small plastic parts |
Hot Glue |
Temporary repairs |
Curing and Bonding the Fix
Once the epoxy or plastic welding compound has been applied to the hole, it is important to allow it to cure and bond properly. The curing time will vary depending on the type of epoxy or plastic welding compound used. It is important to follow the manufacturer’s instructions carefully. In general, the following steps should be followed:
1. Apply a small amount of epoxy or plastic welding compound to the center of the hole.
2. Use a cotton swab or toothpick to spread the epoxy or plastic welding compound around the edges of the hole.
3. Allow the epoxy or plastic welding compound to cure for the amount of time specified by the manufacturer.
4. Once the epoxy or plastic welding compound has cured, sand it down until it is flush with the surface of the plastic.
5. Clean the area around the hole with a mild detergent and water.
6. If desired, apply a coat of paint or clear sealant to the repaired area to protect it from further damage.
Sanding and Smoothing the Surface
Once the hole has been filled and allowed to cure, it’s time to sand and smooth the surface. This will help to blend the repair seamlessly with the rest of the plastic.
Here are the steps for sanding and smoothing the surface:
- Start with a coarse-grit sandpaper (around 100-120 grit) and lightly sand around the repair area.
- Move to a medium-grit sandpaper (around 180-220 grit) and continue sanding until the surface is smooth and even.
- Finish with a fine-grit sandpaper (around 320-400 grit) to create a smooth, polished finish.
- If you’re working on a glossy plastic surface, you can use a polishing compound to restore the shine.
- To determine whether the repair is completely smooth, run your fingers over the surface and feel for any bumps or depressions.
- If necessary, use a wet/dry sandpaper and water to further smooth and polish the surface.
- Once you’re satisfied with the smoothness of the surface, you can clean the area with a damp cloth and let it dry completely.
Tips for Sanding and Smoothing
Here are some additional tips for sanding and smoothing the surface:
- Use a sanding block to ensure even sanding and prevent the sandpaper from tearing or folding.
- Sand in circular motions to avoid creating scratches in the plastic.
- Don’t press too hard when sanding, as this can damage the plastic.
- Be patient and take your time to achieve a smooth, professional-looking finish.
Waterproofing the Repair
Inspect the Hole
Before attempting to waterproof the repair, thoroughly inspect the hole to assess its size, shape, and location. Determine if there are any cracks or tears that extend beyond the visible hole.
Clean and Dry the Area
Use a clean cloth or paper towel to remove any dirt, debris, or moisture from the area around the hole. Allow the surface to dry completely before proceeding with the repair.
Apply a Waterproof Adhesive
Apply a generous amount of waterproof adhesive, such as marine-grade epoxy or silicone sealant, to the edges of the hole. Use a small brush or applicator to spread the adhesive evenly.
Insert a Patch
If the hole is large, insert a patch over the opening. Cut a piece of waterproof fabric or plastic larger than the hole and center it over the opening. Apply pressure to secure the patch.
Apply More Adhesive
Cover the patch with additional waterproof adhesive to seal it in place. Use a putty knife or similar tool to smooth the adhesive and eliminate any air bubbles.
Clamp the Repair
Apply pressure to the repair using clamps or weights. This will help bond the adhesive and ensure a secure waterproof seal.
Allow Time to Cure
Allow the adhesive to cure completely according to the manufacturer’s instructions. This may take several hours or even days, depending on the type of adhesive used.
Additional Waterproofing Measures
For added waterproofing, you can apply a waterproofing spray or sealant over the repaired area. This will create an additional layer of protection against moisture.
Testing the Repair’s Durability
Once you have applied the repair, it is important to test its durability to ensure that it will hold up under normal use. Here are some methods you can use:
-
Visual Inspection:
Examine the repaired area carefully for any signs of weakness or cracking. If there are any visible defects, the repair may not be strong enough and you may need to reinforce it or try a different method.
-
Stress Test:
Apply pressure or force to the repaired area to simulate normal use. You can do this by bending, twisting, or pressing on the area gently. If the repair holds up well under stress, it is likely to be durable.
-
Heat Test:
For repairs made with heat-resistant materials, you can test their durability by exposing them to heat. Place the repaired item in an oven or heat it up with a heat gun. If the repair remains intact after heating, it is likely to withstand high temperatures.
-
Water Test:
If the repaired item is likely to come into contact with water, perform a water test to ensure that the repair is waterproof. Submerge the item in water for a period of time and then remove it to check for any leaks or moisture penetration.
-
Impact Test:
For repairs that may be subjected to impact, drop the repaired item from a small height and observe the results. If the repair holds up well and does not sustain any damage, it is likely to be impact-resistant.
-
Chemical Exposure Test:
If the repaired item may come into contact with chemicals, perform a chemical exposure test. Expose the repair to the chemical in a controlled environment and observe the results. If the repair remains intact and does not show any signs of degradation, it is likely to be resistant to the chemical.
-
Abrasion Test:
For repairs that will experience friction or abrasion, perform an abrasion test. Rub the repaired area with a coarse material or sandpaper to simulate everyday use. If the repair remains smooth and undamaged, it is likely to be resistant to abrasion.
-
Fatigue Test:
For repairs that will be subjected to repeated stress or motion, perform a fatigue test. Subject the repaired area to repetitive force or movement and observe the results. If the repair remains intact and does not show any signs of failure, it is likely to withstand fatigue.
-
Field Test:
The most comprehensive test of a repair is a field test. Use the repaired item in its intended application and monitor its performance. If the repair holds up well under real-world conditions, it is likely to be durable.
Materials You’ll Need:
– Plastic welding kit or epoxy
– Sandpaper
– Cleaning solution
– Plastic sheet or scrap (for patching)
– Clamps or weights
Tips for a Successful Plastic Hole Repair
1. Clean the Area:
Thoroughly clean the area around the hole with a cleaning solution and a soft cloth. Remove any debris or dirt that could interfere with the repair.
2. Prepare the Hole:
Sand the edges of the hole smoothly to create a clean surface for bonding. If the hole is large, create a bevel on the inside edge to allow for a stronger bond.
3. Choose the Repair Method:
For small holes, epoxy or plastic welding can be used. For larger holes, a patch may be necessary.
4. Apply the Adhesive:
If using epoxy, apply it to both the hole and the patch (if used). For plastic welding, heat the welding rod and melt it into the hole.
5. Insert the Patch (if needed):
For larger holes, cut a plastic patch to size and insert it into the hole. Use clamps or weights to hold the patch in place while it bonds.
6. Cure the Adhesive:
Allow the adhesive to cure according to the manufacturer’s instructions. This may take several hours or overnight.
7. Remove Excess Adhesive:
Once the adhesive is cured, use a sharp knife or razor blade to remove any excess that may have seeped out.
8. Sand and Smooth the Surface:
Sand the repaired area smooth using fine-grit sandpaper. This will create a seamless transition between the patch and the surrounding plastic.
9. Protect the Repair (Optional):
If the repaired area will be exposed to harsh conditions, apply a clear sealant or paint to protect it from UV rays and moisture.
10. Troubleshooting Common Issues:
Problem |
Solution |
Hole is too large |
Use a patch or consult a professional |
Adhesive doesn’t bond |
Clean the area better, check the adhesive type |
Surface is not smooth |
Sanding and smoothing more |
Repair is weak |
Use more adhesive or a patch |
How To Repair A Hole In Plastic
If you have a hole in a plastic item, there are a few different ways to repair it. The best method for you will depend on the size and location of the hole, as well as the type of plastic. However, here are some general steps that you can follow for most plastic repairs:
- Clean the area around the hole with rubbing alcohol or a mild detergent. This will help to remove any dirt or debris that could interfere with the repair.
- If the hole is small, you can try using a toothpick or a small piece of wire to push the edges of the hole together. You can also apply a small amount of cyanoacrylate glue to the edges of the hole and then press them together. Hold the pieces together for a few minutes until the glue has set.
- If the hole is larger, you can use a plastic patch to repair it. Cut a piece of plastic that is slightly larger than the hole and then apply a small amount of cyanoacrylate glue to the edges of the patch. Press the patch over the hole and hold it in place for a few minutes until the glue has set.
- If the hole is in a difficult to reach location, you can use a soldering iron to repair it. Heat the soldering iron and then touch it to the edges of the hole. The heat will melt the plastic and fuse the edges together.
Once the repair is complete, allow the plastic to cool and harden completely before using it again.
People Also Ask
How do you fix a small hole in plastic?
You can use a toothpick or a small piece of wire to push the edges of the hole together. You can also apply a small amount of cyanoacrylate glue to the edges of the hole and then press them together. Hold the pieces together for a few minutes until the glue has set.
How do you fix a large hole in plastic?
You can use a plastic patch to repair a large hole in plastic. Cut a piece of plastic that is slightly larger than the hole and then apply a small amount of cyanoacrylate glue to the edges of the patch. Press the patch over the hole and hold it in place for a few minutes until the glue has set.
How do you fix a hole in plastic without glue?
You can use a soldering iron to repair a hole in plastic without glue. Heat the soldering iron and then touch it to the edges of the hole. The heat will melt the plastic and fuse the edges together.