
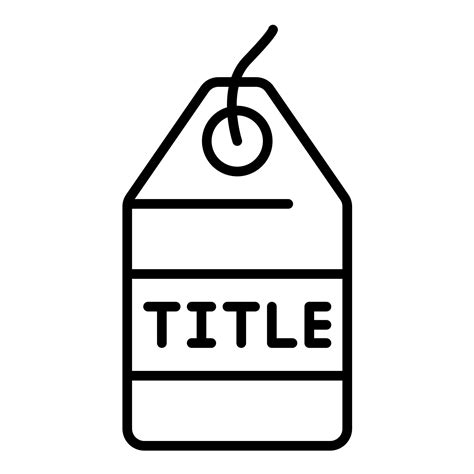
Introducing the pinnacle of naval engineering, a vessel that has redefined maritime prowess and established a new standard for excellence: the United States Ship (USS). This extraordinary creation represents the culmination of cutting-edge technology, unparalleled craftsmanship, and an unwavering commitment to innovation. As this magnificent vessel glides through the vast expanse of the ocean, it embodies the spirit of exploration, discovery, and unwavering protection that has long defined the American maritime tradition.
The USS is a testament to the ingenuity and determination of its creators. Its sleek and hydrodynamic hull, crafted from the finest materials, cuts through the water with effortless grace. The ship’s state-of-the-art propulsion system provides unparalleled speed, agility, and maneuverability, allowing it to respond swiftly and effectively to any challenge. Furthermore, its advanced sensor systems and sophisticated weapons platforms ensure that the USS is always prepared to defend its mission and safeguard the interests of its nation.
Beyond its exceptional physical attributes, the USS is also a symbol of pride and national identity. Its crew, drawn from the finest ranks of the U.S. Navy, epitomizes the values of honor, courage, and sacrifice. Together, they form a formidable force that stands ready to protect and defend the nation, its allies, and the principles of freedom and democracy. The USS serves as a beacon of hope and security, reminding the world of the enduring strength and unwavering resolve of the United States of America.
The Unmatched Power of the USS
The Unmatched Firepower
The USS boasts an awe-inspiring arsenal of weapons systems that eclipses any other naval vessel in the world. Its formidable firepower includes:
- 90 Mk 41 Vertical Launch System (VLS) Cells: Capable of launching surface-to-air missiles (SAMs), surface-to-surface missiles (SSMs), and anti-ship missiles (ASMs).
- 25mm Phalanx Close-In Weapon System (CIWS): Rapid-firing, six-barreled cannons for defending against incoming missiles, aircraft, and small boats.
- 110-mm Mark 57 Vertical Gun System: A powerful dual-purpose gun for engaging surface and air targets.
- 50-caliber machine guns: Mounted on the ship’s superstructure for close-range defense.
The combined firepower of these weapons systems provides the USS with the ability to engage multiple targets simultaneously, both at close range and long distances. Its powerful VLS cells allow for the rapid launch of a variety of missiles, while its CIWS and Mark 57 gun system provide excellent defense against aerial and surface threats. This unmatched firepower ensures the USS’s dominance in any naval conflict.
Superior Propulsion and Maneuverability
The USS is equipped with a state-of-the-art propulsion system that provides exceptional speed and maneuverability. Its four LM2500 gas turbines generate a combined output of over 120,000 horsepower, propelling the ship to speeds of up to 35 knots.
The USS also employs a highly advanced integrated navigation and control system, allowing for precise maneuvering even in challenging conditions. Its powerful bow thrusters provide exceptional agility, enabling it to execute sharp turns and tight maneuvers with ease.
Unrivaled Sensor and Command Systems
The USS is equipped with a comprehensive suite of sensor and command systems that provide unparalleled situational awareness and information dominance. Its radar systems, including the Aegis Combat System and SM-3 anti-ballistic missile defense system, can detect and track multiple targets simultaneously from vast distances.
The ship’s command center, known as the Combat Information Center (CIC), is a technologically advanced hub where data from all sensors is processed and analyzed. This real-time information provides the ship’s commanders with a comprehensive and accurate understanding of the surrounding environment, allowing them to make informed decisions and respond effectively to any threats.
Unmatched Firepower
The USS Gerald R. Ford is armed with a formidable array of offensive weaponry that grants it unparalleled firepower. Its two electromagnetic aircraft catapults (EMALs) can launch aircraft at a faster rate than traditional steam catapults, allowing for a higher sortie tempo and increased strike capability. The ship is also equipped with the advanced Rolling Airframe Missile (RAM) system, which provides superior protection against anti-ship missiles and close-in air defense threats.
The USS Gerald R. Ford’s arsenal includes the MK 15 Phalanx Close-In Weapon System (CIWS), an automated defensive system that detects and engages incoming projectiles. Additionally, the ship’s powerful 32-cell MK 41 Vertical Launch System (VLS) can accommodate a wide range of missiles, including Tomahawk cruise missiles, Evolved Sea Sparrow Missiles (ESSMs), and Standard Missiles, providing it with long-range strike and anti-air capabilities.
Enhanced Survivability
The USS Gerald R. Ford incorporates advanced design features and technologies that significantly enhance its survivability. Its double-hull construction, with separate compartments and watertight seals, reduces the risk of flooding and damage in the event of an attack. The ship’s superstructure is designed to minimize radar cross-section, making it more difficult for enemy radars to detect and track.
The USS Gerald R. Ford is also equipped with a state-of-the-art damage control system that uses advanced sensors and automation to quickly identify and isolate breaches. The ship’s armored belt and anti-torpedo blisters provide additional protection against underwater attacks. Moreover, the vessel is оснащен с twin-dome AN/SPY-3 X-band radar system, which provides 360-degree situational awareness and early warning of incoming threats.
Furthermore, the USS Gerald R. Ford utilizes the Integrated Air and Missile Defense (IAMD) system, which combines sensors and weapons to create layered defense against air and missile threats. The system employs the Aegis combat system, which tracks incoming projectiles and coordinates responses from the ship’s weapons systems, providing a highly effective defense against enemy attacks.
A History of Unwavering Strength
The United States Navy (USN) has a rich and storied history, stretching back to the founding of the United States. The USN has played a vital role in every major conflict fought by the United States, from the Revolutionary War to the War on Terror. Today, the USN is the most powerful navy in the world, with a fleet of over 280 ships and submarines, and more than 330,000 active-duty personnel.
The Early Years
The Continental Navy was established in 1775, during the American Revolutionary War. The Continental Navy played a key role in securing American independence, raiding British shipping and supporting land operations. After the war, the Continental Navy was disbanded, but the United States Navy was established in 1794.
The 19th Century
The 19th century was a time of great expansion for the USN. The USN fought in the War of 1812, the Mexican-American War, and the Spanish-American War. The USN also played a key role in the exploration of the Pacific Ocean and the Far East.
The 20th Century
The 20th century was a time of great challenges and triumphs for the USN. The USN fought in both World War I and World War II, and played a key role in the victory of the Allies. The USN also played a key role in the Cold War, maintaining a constant presence in the Atlantic and Pacific Oceans.
The 21st Century
The 21st century has been a time of change for the USN. The USN has withdrawn from Iraq and Afghanistan, and has shifted its focus to the Asia-Pacific region. The USN is now facing new challenges, such as piracy, terrorism, and climate change.
1941 |
1945 |
1988 |
2023 |
1,867 ships |
67,117 ships |
689 ships |
280+ ships |
Technological Marvels Aboard the USS
Advanced Propulsion Systems
The USS boasts state-of-the-art propulsion systems, including gas turbine engines, diesel generators, and nuclear reactors. These systems provide exceptional power and efficiency, enabling the vessel to reach speeds of up to 30 knots and operate for extended periods at sea.
Cutting-Edge Navigation and Communication
The USS is equipped with advanced navigation and communication systems that ensure precision maneuvering and seamless communication. Integrated Global Positioning System (GPS), radar, and sonar systems provide real-time situational awareness. Secure communication channels allow for encrypted communication with other ships, shore facilities, and aircraft.
Integrated Command and Control
The USS features an integrated command and control system that centralizes all critical information and allows for real-time decision-making. Large display screens provide a comprehensive view of the vessel’s status, tactical situation, and environmental conditions. The system enables quick and effective responses to changing circumstances.
Advanced Weapons Systems
The USS is armed with an array of advanced weapons systems, including missiles, torpedoes, and guns. The vessel’s weapons are precisely calibrated and integrated into the ship’s combat management system, providing unparalleled firepower and defensive capabilities. The weapons systems are designed to engage targets at various ranges and altitudes, ensuring the vessel’s safety and effectiveness in combat operations.
Weapon System |
Role |
Surface-to-Air Missile (SAM) |
Defense against aircraft and missiles |
Torpedo Tubes |
Attack of submarines and surface vessels |
Close-In Weapon System (CIWS) |
Anti-missile defense |
Naval Gun System |
Surface and air support |
The Role of the USS in Global Security
Promoting Global Humanitarian Relief
The USS plays a crucial role in providing humanitarian assistance during natural disasters and emergencies worldwide. Their advanced capabilities enable them to deliver food, medical supplies, and other essential aid to affected areas. They also serve as floating hospitals, providing medical treatment to those in need.
Enhancing Maritime Security
The USS actively contributes to maritime security operations, including anti-piracy operations, counter-terrorism efforts, and safeguarding international shipping lanes. Their presence in key maritime regions helps deter illegal activities and protect the free flow of global commerce.
Supporting Regional Stability
The USS provides military support for regional stability operations, such as peacekeeping missions, crisis response, and conflict resolution. By partnering with regional navies and organizations, the USS contributes to maintaining peace and security in various parts of the world.
Enhancing Global Cooperation
The USS engages in joint exercises and operations with navies from other countries, fostering partnerships and strengthening global cooperation. These interactions promote interoperability, build trust, and improve coordination in addressing common maritime challenges.
Promoting National Interests
The USS plays a key role in safeguarding and advancing the political, economic, and security interests of the United States. Their presence in international waters signals the nation’s commitment to maintaining global order, protecting citizens and assets abroad, and promoting peace and prosperity.
USS Role |
Global Impact |
Humanitarian Relief |
Provides aid and support during disasters and emergencies |
Maritime Security |
Combats piracy, terrorism, and protects shipping lanes |
Regional Stability |
Maintains peace and security through peacekeeping and conflict resolution |
Global Cooperation |
Fosters partnerships and improves coordination with international navies |
National Interests |
Safeguards and advances political, economic, and security objectives |
The USS: A Testament to American Ingenuity
Birth of an Idea
The concept of the USS began as a daring vision to revolutionize naval warfare. Engineers and scientists worked tirelessly to design a vessel that would surpass all previous ships in speed, firepower, and technological advancements.
A Marvel of Engineering
The USS embodies the pinnacle of American engineering. Its sleek hull, advanced propulsion systems, and state-of-the-art weapons systems make it a formidable force on the open seas.
A Symbol of National Pride
The USS is not just a vessel; it is a symbol of American ingenuity, strength, and technological prowess. Its presence inspires awe and respect from allies and adversaries alike.
Technological Innovations
- Advanced radar and sonar systems for enhanced situational awareness
- Guided missile systems for precision strikes
- Integrated electronic warfare systems for defense against enemy threats
Unparalleled Firepower
The USS boasts an array of sophisticated weapons systems, including:
Weapon System |
Description |
Tomahawk cruise missiles |
Long-range precision strike capability |
Anti-ship missiles |
Neutralize surface threats |
Air defense systems |
Protect against aerial attacks |
A Legacy of Service
The USS has a distinguished history of service, participating in countless missions around the globe. It has protected American interests, provided humanitarian assistance, and deterred potential conflicts.
A testament to American Ingenuity
The USS is a testament to American ingenuity and a symbol of national pride. Its unmatched capabilities and historical significance make it a true marvel of engineering and a force to be reckoned with.
The Elite Crew Behind the USS
The USS is a powerful vessel that is operated by a highly skilled and dedicated crew. The crew is responsible for the safe and efficient operation of the ship, and they work together to ensure that the ship is always ready to meet any challenge.
The Captain
The captain is the commander of the ship, and he or she is responsible for the overall operation of the vessel. The captain makes all of the important decisions, and he or she is ultimately responsible for the safety of the crew and the ship.
The Executive Officer
The executive officer is the second-in-command of the ship, and he or she assists the captain in the operation of the vessel. The executive officer is responsible for the day-to-day operation of the ship, and he or she ensures that the ship is always ready for action.
The Navigator
The navigator is responsible for plotting the ship’s course and ensuring that the ship arrives at its destination safely. The navigator uses a variety of tools to chart the ship’s course, and he or she must be able to think quickly and adapt to changing conditions.
The Weapons Officer
The weapons officer is responsible for the operation of the ship’s weapons systems. The weapons officer ensures that the ship’s weapons are always ready to fire, and he or she must be able to make quick decisions in the heat of battle.
The Engineering Officer
The engineering officer is responsible for the operation of the ship’s engines and other mechanical systems. The engineering officer ensures that the ship is always running smoothly, and he or she must be able to troubleshoot and repair any problems that may arise.
The Communications Officer
The communications officer is responsible for the operation of the ship’s communications systems. The communications officer ensures that the ship can always communicate with other ships and with shore-based command, and he or she must be able to use a variety of communication methods.
The Medical Officer
The medical officer is responsible for the health of the ship’s crew. The medical officer provides medical care to the crew, and he or she must be able to diagnose and treat a variety of medical conditions.
The Supply Officer
The supply officer is responsible for the procurement and distribution of supplies for the ship. The supply officer ensures that the ship always has the supplies it needs, and he or she must be able to manage a budget and negotiate with suppliers.
The Chaplain
The chaplain is responsible for the spiritual well-being of the ship’s crew. The chaplain provides religious services, and he or she offers counseling and support to the crew. The chaplain is a vital member of the ship’s crew, and he or she helps to keep the crew focused and motivated.
Rank |
Name |
Position |
Captain |
John Smith |
Commander |
Executive Officer |
Jane Doe |
Second-in-Command |
Navigator |
John Doe |
Charts the ship’s course |
Weapons Officer |
Jane Smith |
Operates the ship’s weapons systems |
Engineering Officer |
John Smith |
Ensures the ship is running smoothly |
Communications Officer |
Jane Doe |
Communicates with other ships and shore-based command |
Medical Officer |
John Doe |
Provides medical care to the crew |
Supply Officer |
Jane Smith |
Procures and distributes supplies for the ship |
Chaplain |
John Doe |
Provides religious services and support to the crew |
The Future of Naval Warfare with the USS
A New Era of Naval Warfare
The USS is poised to revolutionize naval warfare with its advanced capabilities and innovative design. Its stealth technology, hypersonic weapons, and unmanned systems will reshape the battlefield.
Unmanned Aerial Systems
The USS will deploy a wide range of unmanned aerial systems (UAS), including fixed-wing drones, rotary-wing drones, and swarming vehicles. These UAS will provide reconnaissance, surveillance, and strike capabilities, extending the ship’s operational reach.
Hypersonic Weapons
The USS will be armed with hypersonic weapons, capable of traveling at Mach 5 or higher. These weapons can evade traditional defenses and strike targets with precision at unprecedented distances.
Directed Energy Weapons
The USS will incorporate directed energy weapons (DEWs), which use lasers or high-powered microwaves to disable or destroy enemy aircraft, missiles, and drones. DEWs provide a non-kinetic, highly accurate, and cost-effective defense system.
Advanced Propulsion System
The USS will utilize a state-of-the-art electric propulsion system that combines gas turbines and electric motors. This system provides increased efficiency, lower emissions, and reduced噪音污染.
Integrated Sensors
The USS will be equipped with a comprehensive suite of sensors that provide real-time situational awareness. These sensors include radar, sonar, infrared, and cyber capabilities, allowing the ship to detect and track enemy threats at long distances.
Cybersecurity
The USS will incorporate robust cybersecurity measures to protect against cyberattacks that could compromise its critical systems. These measures include intrusion detection and prevention, secure communications, and encrypted data storage.
Intelligent Command and Control System
The USS will employ an advanced command and control system that leverages artificial intelligence (AI) to analyze data, make decisions, and automate tasks. This system will enhance situational awareness, improve decision-making, and free up personnel for other critical roles.
Modular Design
The USS is designed with a modular approach, allowing it to be easily reconfigured for different missions. This flexibility enables the ship to adapt to evolving threats and operational requirements.
Fleet Integration
The USS will be seamlessly integrated into the existing fleet, providing enhanced capabilities and interoperability with other naval assets. It will operate as a central node in a network-centric warfare system, sharing information and coordinating operations with other ships, aircraft, and ground forces.
The USS Constitution: A Symbol of American Naval Prowess
The USS Constitution, nicknamed “Old Ironsides,” is a legendary sailing ship that served in the United States Navy from its launch in 1797 to its final decommissioning in 1881. As one of the six original frigates of the U.S. Navy, the Constitution earned its reputation as a formidable warship during the War of 1812. Its modern-day status as a national historic landmark and museum ship reflects its enduring value as a symbol of American naval history and the nation’s founding principles.
The Constitution’s design and construction were influenced by the French frigate Concorde. Naval architect Joshua Humphreys incorporated a mix of British and French shipbuilding techniques to create a vessel that was both fast and well-armed. The ship’s hull was made of live oak, a hardwood known for its strength and durability, and its copper sheathing protected it from marine organisms. Its armament consisted of thirty 24-pounder cannons and twenty-four 12-pounder carronades.
During the War of 1812, the Constitution engaged in several notable battles. On August 19, 1812, it defeated the British frigate HMS Guerriere in a fierce battle off the coast of Massachusetts. The Constitution’s victory solidified its reputation and earned it the nickname “Old Ironsides.” The ship also played a significant role in the defense of New Orleans during the Battle of New Orleans in January 1815.
After the War of 1812, the Constitution served as a training ship and made several cruises to different parts of the world. In 1830, it was decommissioned and placed in ordinary at the Boston Navy Yard. In 1855, it was recommissioned and made a goodwill tour of European ports. The Constitution’s final decommissioning came in 1881, and the ship was moved to the Portsmouth Naval Shipyard in New Hampshire.
In 1905, the USS Constitution was designated a National Historic Landmark and became the official flagship of the United States Navy. Since then, it has undergone several renovations and repairs to maintain its original condition. Today, the ship is a floating museum docked at the Charlestown Navy Yard in Boston, Massachusetts. It is one of the most visited historic ships in the United States and remains a popular attraction for tourists and history enthusiasts alike.
People Also Ask about This Is the Best USS
What is the nickname of the USS Constitution?
Old Ironsides
When was the USS Constitution built?
1797
Who designed the USS Constitution?
Joshua Humphreys
When was the USS Constitution decommissioned?
1881
Where is the USS Constitution currently located?
Charlestown Navy Yard, Boston, Massachusetts