
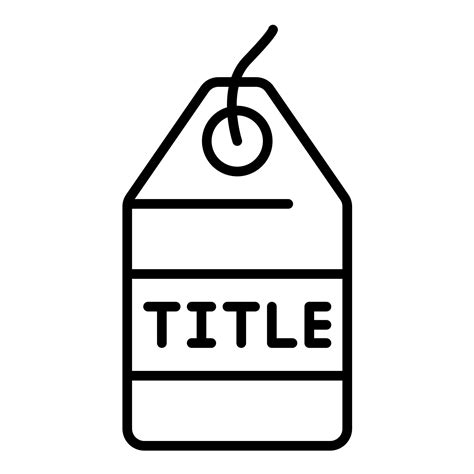
If you’re new to electrical wiring, the prospect of installing a volt gauge can seem daunting. However, with a little bit of preparation and the right tools, it’s a relatively straightforward process that can be completed in a few hours. In this guide, we’ll provide you with step-by-step instructions on how to wire a volt gauge, as well as some troubleshooting tips to help you get the job done right. Whether you’re looking to monitor the voltage of your car battery or troubleshooting an electrical system, a volt gauge is an essential tool that can help you stay on top of your electrical system’s health.
The first step in wiring a volt gauge is to choose the right location. You’ll want to find a spot that’s easy to access and visible while you’re driving. Once you’ve chosen a location, you’ll need to gather your tools. You’ll need a volt gauge, a wire cutter/stripper, electrical tape, and a drill. Once you have your tools, you can begin the wiring process. Start by drilling a small hole in the dash where you want to mount the volt gauge. Then, feed the wires from the volt gauge through the hole and connect them to the appropriate terminals on the back of the gauge.
Once the volt gauge is wired, you can test it by turning on the ignition. The volt gauge should read the voltage of the battery. If it doesn’t, check your connections to make sure they’re secure. Once you’re satisfied that the volt gauge is working properly, you can button everything up and enjoy the peace of mind that comes with knowing you can monitor your electrical system’s health.
Basics of Volt Gauge Wiring
A volt gauge is a measuring instrument used to measure the electrical potential difference (voltage) between two points in a circuit. It is typically connected in parallel with the circuit component whose voltage is being measured. Volt gauges are available in both analog and digital formats, and they can be used to measure AC or DC voltage. Before we get into the specifics of wiring a volt gauge, let’s first discuss some basic electrical concepts.
Voltage is the difference in electrical potential between two points in a circuit. It is measured in volts (V). Current is the flow of electrical charge through a circuit. It is measured in amperes (A). Resistance is the opposition to the flow of current through a circuit. It is measured in ohms (Ω).
Ohm’s Law
Ohm’s Law is a fundamental law of electricity that relates voltage, current, and resistance. It states that the current flowing through a conductor between two points is directly proportional to the voltage across the two points and inversely proportional to the resistance of the conductor. Mathematically, Ohm’s Law can be expressed as:
where:
- I is the current in amperes
- V is the voltage in volts
- R is the resistance in ohms
Understanding Voltage and Electrical Systems
Voltage
Voltage is a measure of the electrical potential difference between two points in a circuit or electrical system. It is often measured in volts (V). A simple analogy for understanding voltage is to think of it as the pressure of water flowing through a pipe. The higher the voltage, the more electrical pressure there is.
Electrical Systems
Electrical systems can be divided into two main types: AC (alternating current) and DC (direct current). AC systems are characterized by a voltage that alternates its polarity (i.e., it changes from positive to negative and back again) over time. DC systems, on the other hand, maintain a constant polarity.
In automotive applications, the electrical system is typically a DC system with a voltage of 12 or 24 volts. This system provides power to various components, such as lights, ignition systems, and engine control modules. Understanding voltage and electrical systems is important for diagnosing and repairing electrical problems in vehicles.
Types of Electrical Systems
There are two main types of electrical systems:
Type |
Description |
AC (alternating current) |
Voltage alternates its polarity (changes from positive to negative and back again) over time. |
DC (direct current) |
Voltage maintains a constant polarity. |
In automotive applications, the electrical system is typically a DC system with a voltage of 12 or 24 volts.
Safety Precautions for Electrical Work
Grounding and Insulation
- Ensure all electrical equipment is properly grounded to prevent electrical shock.
- Use insulated tools and wear electrical safety gear when working on electrical systems.
Disconnecting Power
- Always disconnect the power source before performing any electrical work.
- Use a lock-out/tag-out procedure to prevent accidental reconnection.
Testing and Troubleshooting
- Use a voltage tester to verify that the power is disconnected before proceeding.
- If a short circuit occurs, immediately disconnect the power and isolate the affected circuit.
- Use a multimeter to check voltage, resistance, and continuity as needed to troubleshoot electrical problems.
Additional Safety Tips
- Work in a well-lit and ventilated area.
- Avoid working on electrical systems during inclement weather or when fatigued.
- Seek professional help if you encounter any electrical issues beyond your expertise.
- Remember that electrical work can be dangerous, and it is essential to prioritize safety at all times.
Choosing the Right Volt Gauge
Selecting the appropriate volt gauge for your project is crucial. Consider the following factors when making your choice:
Type of Gauge
Volt gauges come in two main types: analog and digital.
- Analog gauges feature a needle that moves along a scale, providing a continuous readout.
- Digital gauges display the voltage value numerically on an LCD or LED screen.
Analog gauges are generally less expensive and more durable, while digital gauges offer greater accuracy and readability.
Voltage Range
The voltage range of the gauge should match the expected voltage levels in your system. Most automotive volt gauges have a range of 8-16 volts. For marine or industrial applications, gauges with higher ranges may be necessary.
Accuracy and Resolution
Accuracy refers to how closely the gauge’s readings match the actual voltage. Resolution indicates the smallest increment that the gauge can measure. Higher accuracy and resolution are desirable for applications where precise voltage monitoring is essential.
Connection Type
Volt gauges can be connected to your system using various methods:
Terminal Posts
Gauges with terminal posts have screw or spring-loaded terminals for direct wire connections. This is the most straightforward and secure method.
Ring Terminals and Spade Connectors
These connectors allow you to crimp wires to the gauge’s terminals for a semi-permanent connection. They provide a clean and insulated connection.
Wire Leads
Some gauges come with pre-attached wire leads for direct splicing into the electrical system. This method is convenient but may require additional insulation and protection.
Panel Mount
Panel-mount gauges are designed to be installed in a panel or dashboard. They typically have a bezel or housing that secures them in place.
Selecting the Appropriate Wire Gauge
Selecting the appropriate wire gauge for your volt gauge is crucial to ensure accurate readings and prevent electrical hazards. The wire gauge, measured in American Wire Gauge (AWG) units, indicates the thickness of the wire.
Factors Affecting Wire Gauge Selection
Several factors influence the appropriate wire gauge, including:
- Current draw: The amount of current flowing through the wire.
- Wire length: Longer wires require thicker gauges to minimize voltage drop.
- Voltage: Higher voltage applications require thicker gauges to handle the higher voltage.
- Ambient conditions: High temperatures, moisture, and chemicals can degrade the wire’s insulation, requiring thicker gauges.
Gauge Recommendations
As a general guideline, the following wire gauges are recommended for various applications:
Application |
Recommended Gauge |
Low current (less than 1 amp), short distance (less than 10 feet) |
18 AWG |
Moderate current (1-5 amps), medium distance (10-50 feet) |
16 AWG |
High current (5-10 amps), long distance (over 50 feet) |
14 AWG |
Tips for Selecting the Right Gauge
- Consider the maximum current draw of your volt gauge.
- Determine the length of the wire run.
- Account for any potential voltage drop or environmental factors.
- Choose a wire gauge that is at least one gauge size larger than the recommended minimum to provide a margin of safety.
- Use stranded wire for flexibility and durability.
Determining the Power Source and Ground
Identifying the correct power source and ground are crucial for accurate voltage readings. Here are the detailed steps to determine these:
1. Identifying the Power Source
Locate a suitable power source with sufficient voltage to power the volt gauge. Commonly, it is the positive terminal of the battery or an ignition-switched fuse in the fuse box.
2. Choosing the Wire Color
Select a wire color that differentiates it from other electrical wires in the vehicle. Red or yellow is typically used for power sources.
3. Determining the Gauge Size
Select a wire gauge appropriate for the current draw of the volt gauge. Refer to the gauge’s specifications for the recommended wire size.
4. Running the Power Wire
Run the power wire from the chosen power source to the volt gauge. Securely connect it to the gauge’s positive terminal.
5. Selecting the Ground Location
Identify a suitable ground point, typically a metal surface that is unpainted and connected to the vehicle’s chassis. Avoid using plastic or fiberglass surfaces.
6. Grounding the Volt Gauge
Run a wire from the ground point to the volt gauge’s negative terminal. Ensure a secure and clean connection. The following table provides additional insights into grounding:
Ground Type |
Advantages |
Disadvantages |
Chassis Ground |
Most common, easy to implement |
Can introduce noise and interference |
Battery Ground |
Provides clean and stable ground |
Requires special wiring and may be inconvenient |
Block Ground |
Reduces electrical noise |
Can be difficult to find a suitable location |
Wiring the Volt Gauge to the Power Source
Wiring the volt gauge to the power source is a crucial step in the process of installing a volt gauge. Here are the detailed steps involved:
1. Locate a suitable power source. This could be the battery terminals, a fuse box, or an ignition switch.
2. Determine the polarity of the power source. The positive terminal is typically red, and the negative terminal is black.
3. Connect the red wire from the volt gauge to the positive terminal of the power source.
4. Connect the black wire from the volt gauge to the negative terminal of the power source.
5. Secure the connections using electrical tape or wire nuts.
6. Turn on the power source and verify that the volt gauge is working properly.
7. **Protect the Circuit**: To protect the voltmeter and the electrical system, it’s recommended to install a fuse in line with the power wire. Choose a fuse value that is appropriate for the maximum current that will flow through the circuit. The table below provides typical fuse values for different wire gauges:
Wire Gauge |
Fuse Value |
16 AWG |
15 A |
14 AWG |
20 A |
12 AWG |
25 A |
10 AWG |
30 A |
Grounding the Volt Gauge
Grounding the volt gauge is an important step in the wiring process. A good ground connection will ensure that the gauge is accurate and will not be affected by electrical noise. There are a few different ways to ground the volt gauge, and the best method will depend on the specific application.
Methods of Grounding
One common method of grounding the volt gauge is to use a dedicated ground wire. This wire should be connected to a clean, bare metal surface on the vehicle’s chassis. The other end of the wire should be connected to the negative terminal of the volt gauge.
Another method of grounding the volt gauge is to use the vehicle’s chassis as the ground. This can be done by connecting the negative terminal of the volt gauge to a bolt or other metal surface on the chassis. It is important to make sure that the connection is clean and tight.
If the volt gauge is being installed in a boat, it is important to use a marine-grade ground wire. This type of wire is designed to resist corrosion and will help to ensure that the volt gauge is accurate.
The following table provides a summary of the different methods of grounding the volt gauge:
Grounding Method |
Description |
Dedicated Ground Wire |
A dedicated ground wire is connected to a clean, bare metal surface on the vehicle’s chassis and to the negative terminal of the volt gauge. |
Vehicle Chassis |
The negative terminal of the volt gauge is connected to a bolt or other metal surface on the vehicle’s chassis. |
Marine-Grade Ground Wire |
A marine-grade ground wire is used to connect the negative terminal of the volt gauge to a clean, bare metal surface on the boat’s hull. |
Verifying the Volt Gauge Functionality
After installing the volt gauge, it is crucial to ensure that it’s functioning correctly. Here is a step-by-step guide to verify the accuracy and functionality of your volt gauge:
1. Start the Engine:
Turn on the vehicle’s ignition to provide power to the volt gauge.
2. Observe Idle Voltage:
Pay attention to the voltmeter’s reading at idle. Generally, it should indicate a voltage between 13.5V to 14.5V. This range ensures that the battery is charging properly and the alternator is functioning.
3. Electrical Load Test:
With the engine running at idle, turn on electrical accessories like headlights, air conditioning, and the radio. Observe if the voltage reading drops significantly. A well-functioning volt gauge should show a minimal drop in voltage, indicating the alternator’s ability to handle the electrical load.
4. Voltage Drop Test:
Temporarily disconnect one of the battery terminals while the engine is running. The voltmeter reading should drop abruptly to around 0V. If it doesn’t, there may be a problem with the gauge, wiring, or battery.
5. Comparison with Multimeter:
For higher accuracy, use a multimeter to measure the voltage directly at the battery terminals. Compare the reading with the volt gauge reading. If there’s a significant difference, it indicates a problem with the gauge or installation.
6. Check for Loose Connections:
Ensure that all connections to the volt gauge are tight and secure. Loose wires can cause inaccurate readings.
7. Inspect the Gauge:
If the tests above indicate an issue, inspect the volt gauge itself. Look for any broken or dirty connections, damaged wires, or a faulty display.
8. Check Wiring Continuity:
Use a multimeter to check the wiring continuity between the volt gauge and the battery. Ensure that there are no breaks or shorts in the wiring.
9. Detailed Troubleshooting Table:
| Issue | Possible Cause | Solution |
|—|—|—|
| Gauge not reading | Not powered | Check power supply to gauge |
| Voltage reading always low | Wiring issue | Inspect wiring and connections |
| Voltage reading always high | Gauge faulty | Replace gauge |
| Voltage drops significantly under load | Weak alternator | Check alternator and replace if necessary |
| Voltage reading fluctuates erratically | Loose connections | Tighten all connections |
Troubleshooting Common Volt Gauge Wiring Issues
1. No Reading on Volt Gauge
Ensure the following:
- The power source is connected properly.
- The gauge is grounded.
- The wiring is not damaged or loose.
- The fuse is not blown.
2. Incorrect Reading on Volt Gauge
Check the following:
- The gauge is calibrated correctly.
- The wiring is not shorted to ground.
- The power source is stable.
- The gauge is not damaged.
3. Volt Gauge Fluctuates
Consider these factors:
- The power source is unstable.
- The wiring is loose or damaged.
- The gauge is defective.
- There is electrical interference from nearby devices.
4. Volt Gauge Reads Zero
Verify the following:
- The battery is connected correctly.
- The wiring is not broken or disconnected.
- The fuse is not blown.
- The gauge is not defective.
5. Volt Gauge Reads High
Investigate the following:
- The power source is overcharging.
- The wiring is shorted to a higher voltage source.
- The gauge is defective.
- There is electrical interference from nearby devices.
6. Volt Gauge Reads Low
Consider the following possibilities:
- The battery is discharged.
- The wiring is loose or damaged.
- The gauge is defective.
- There is electrical interference from nearby devices.
7. Volt Gauge Damage
The gauge may be damaged due to:
- Overvoltage
- Reverse polarity
- Excessive heat
- Mechanical shock
8. Gauge Not Working Properly
Inspect the following:
- The wiring is connected securely.
- The power source is stable.
- The fuse is not blown.
- The gauge is not faulty.
9. Gauge Readings Inaccurate
Consider these factors:
- The gauge is not calibrated correctly.
- The wiring is shorted or has excessive resistance.
- The power source is unstable.
- There is electrical interference from nearby devices.
10. Wrong Gauge Choice
Ensure the gauge selected is appropriate for the application by considering the following:
Parameter |
Considerations |
Voltage Range |
Must cover the expected voltage range of the system. |
Accuracy |
Should be sufficient for the intended purpose. |
Response Time |
Should be fast enough to capture voltage fluctuations. |
Display Type |
Choose analog or digital gauge based on preference and readability. |
Mounting Options |
Consider panel-mount or surface-mount gauges. |
How To Wire A Volt Gauge
Wiring a volt gauge is a relatively simple process that can be completed in a few minutes. However, it is important to follow the instructions carefully to ensure that the gauge is wired correctly and is functioning properly.
To wire a volt gauge, you will need the following materials:
- Volt gauge
- Wire strippers
- Electrical tape
- Crimp connectors
Once you have gathered your materials, follow these steps to wire the volt gauge:
- Strip the wires. Use the wire strippers to remove about 1/2 inch of insulation from the ends of the two wires that will be connected to the volt gauge.
- Connect the wires to the volt gauge. Twist the bare ends of the wires together and insert them into the appropriate terminals on the back of the volt gauge. The positive wire should be connected to the positive terminal and the negative wire should be connected to the negative terminal.
- Secure the connections. Use crimp connectors to secure the connections between the wires and the volt gauge. Crimp the connectors firmly with a crimping tool.
- Insulate the connections. Wrap electrical tape around the connections to insulate them and prevent them from shorting out.
- Mount the volt gauge. Mount the volt gauge in a convenient location on the dashboard or instrument panel.
Once the volt gauge is wired and mounted, it is important to test it to make sure that it is functioning properly. To test the volt gauge, start the engine and let it run for a few minutes. The volt gauge should read between 12 and 14 volts. If the volt gauge is not reading correctly, check the connections to make sure that they are secure and that the wires are not damaged.
People Also Ask About How To Wire A Volt Gauge
What is a volt gauge?
A volt gauge is a device that measures the electrical potential difference between two points in a circuit.
Why would I need to wire a volt gauge?
You may need to wire a volt gauge to monitor the voltage of your battery or electrical system.
How do I choose the right volt gauge?
When choosing a volt gauge, you need to consider the following factors: the voltage range that you need to measure, the accuracy that you need, and the size and style of the gauge.