
Embark on an enchanting journey into the world of crochet dolls! These adorable creations, crafted with intricate stitches and boundless creativity, captivate hearts and ignite imaginations. Whether you’re a seasoned crocheter seeking inspiration or a novice eager to master the art, this comprehensive guide will lead you effortlessly through the enchanting realm of doll-making. From selecting the perfect yarn to assembling the final masterpiece, each step is meticulously explained, ensuring that you create dolls that are both charming and enduring.
Transitioning from the basics to more advanced techniques, you’ll delve into the art of shaping delicate features, creating luscious hair, and designing captivating garments. Learn how to craft expressive eyes that seem to dance with life, rosy cheeks that evoke warmth, and adorable noses that beg for a tender boop. With each project you undertake, your skills will soar, and your dolls will become increasingly lifelike and captivating.
As you progress, you’ll discover the secrets of adding intricate embellishments that elevate your dolls to true works of art. Learn how to crochet tiny accessories, such as glasses, hats, and shoes, that add personality and charm to your creations. Embroider delicate details, such as freckles, dimples, and beauty marks, that bring your dolls to life. The possibilities are boundless, limited only by your imagination and the boundless joy of bringing these enchanting creatures into the world.
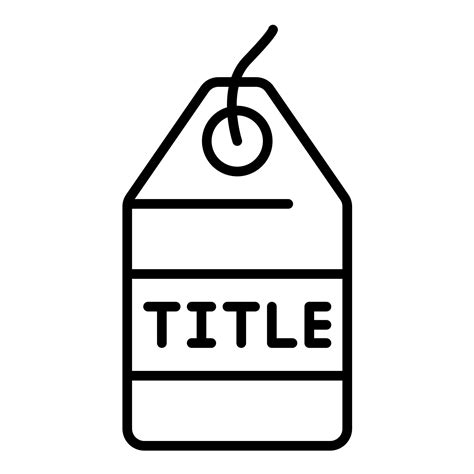
Selecting the Perfect Yarn for Crochet Dolls
Choosing the right yarn is crucial for creating beautiful and durable crochet dolls. Here’s a detailed guide to help you make an informed decision:
Fiber Content
Consider the fiber content of the yarn, as it will affect the softness, drape, and durability of your dolls. Here are some options:
Fiber |
Characteristics |
Cotton |
Strong, breathable, and easy to care for |
Wool |
Warm, insulating, and feltable for details |
Acrylic |
Soft, affordable, and available in a wide range of colors |
Mohair |
Luxurious, silky, and ideal for realistic hair |
Alpaca |
Soft, warm, and hypoallergenic |
Weight and Thickness
The weight of the yarn determines the thickness of your crocheted stitches. Consider the size and desired firmness of your dolls when selecting a weight:
Yarn Weight |
Suggested Doll Size |
Sport/Baby |
Small, delicate dolls |
Worsted |
Medium-sized, all-purpose dolls |
Aran |
Larger, sturdier dolls |
Bulky |
Oversized, plush dolls |
Texture and Sheen
The texture and sheen of the yarn can create different visual effects. Here are some options:
Texture |
Description |
Smooth |
Shiny, polished finish |
Textured |
Lumpy, nubbly, or fuzzy finish |
Metallic |
Sparkling, shiny finish |
Mastering Basic Crochet Stitches for Doll-Making
To embark on the enchanting world of crochet doll-making, it’s essential to conquer the fundamental building blocks: crochet stitches. These humble yet versatile stitches serve as the threads that weave life into your creations.
Single Crochet (sc)
Single crochet, the cornerstone of crochet, forms the backbone of countless crochet projects. Begin by holding the hook in your right hand and the yarn in your left. Insert the hook into the next stitch or space, yarn over the hook, hook the yarn, and draw it through the stitch or space. Again, yarn over the hook and draw it through both loops on the hook. You’ve now completed a single crochet stitch.
Double Crochet (dc)
Double crochet, a step up in size from single crochet, adds height and texture to your creations. Here’s a detailed breakdown:
- Yarn over the hook and insert it into the next stitch or space.
- Yarn over the hook, hook the yarn, and draw it through the stitch or space. You’ll have two loops on your hook.
- Yarn over the hook again and draw it through both loops on the hook. You’ll have two more loops on your hook.
- Yarn over the hook one last time and draw it through the remaining two loops on the hook. You’ve now completed a double crochet stitch.
Half Double Crochet (hdc)
Half double crochet, a hybrid between single crochet and double crochet, provides a balance of height and tightness. Follow these steps:
- Yarn over the hook and insert it into the next stitch or space.
- Yarn over the hook, hook the yarn, and draw it through the stitch or space. You’ll have two loops on your hook.
- Yarn over the hook and draw it through both loops on the hook. You’ve now completed a half double crochet stitch.
Stitch |
Description |
Single Crochet (sc) |
The foundation stitch, creating a compact fabric. |
Double Crochet (dc) |
Taller than single crochet, adding height and texture. |
Half Double Crochet (hdc) |
A balance between sc and dc, providing both height and tightness. |
Creating Realistic Eyes for Your Crochet Dolls
Giving your crochet dolls realistic eyes can greatly enhance their personality and bring them to life. Here’s a detailed guide on how to create stunning eyes for your crochet creations:
Using Safety Eyes
Safety eyes are a convenient and effective option for adding eyes to crochet dolls. They come in various sizes and colors, allowing you to customize the look of your dolls. Choose safety eyes that are appropriate for the size of your doll and the desired level of detail.
Creating Crochet Eyes
For a more intricate and personalized approach, you can create your own crochet eyes. Using fine yarn in desired colors, follow a crochet pattern or experiment with free-form techniques. Once you have crocheted the iris, pupil, and whites of the eyes, assemble them using a small amount of glue or felt.
Sculpting Realistic Irises
For truly lifelike eyes, consider sculpting realistic irises. Here’s a step-by-step guide:
Step 1: |
Roll out a small amount of white polymer clay into a thin sheet. |
Step 2: |
Cut out a circle for the sclera and flatten it slightly. |
Step 3: |
Create a smaller circle for the iris and color it using paint or pastels. |
Step 4: |
Position the iris on the sclera, slightly overlapping the edge. |
Step 5: |
Use a dotting tool or toothpick to create a pupil and add highlights with white clay. |
Step 6: |
Bake the clay according to manufacturer’s instructions. |
Once sculpted, attach the irises to your crochet eyes using glue and finish with a clear coat for shine.
Giving Your Dolls Personality with Hair and Clothing
Hair
The hair of your crochet doll can be made from a variety of materials, such as yarn, thread, or fabric scraps. You can choose the color and texture of the hair to match the personality of your doll. For example, a doll with long, flowing hair might be a gentle and kind-hearted soul, while a doll with short, spiky hair might be a feisty and independent spirit.
There are many different ways to crochet hair. You can use a simple single crochet stitch to create straight hair, or you can use more complex stitches to create curly hair, braids, or other hairstyles. You can also add beads or other embellishments to the hair to give it a unique look.
Clothing
The clothing of your crochet doll can also be used to express its personality. You can choose the colors and patterns of the clothing to match the doll’s hair and overall appearance. For example, a doll wearing a bright pink dress might be a cheerful and optimistic character, while a doll wearing a dark blue suit might be a more serious and sophisticated character.
There are many different ways to crochet clothing for dolls. You can use simple stitches to create basic garments, or you can use more complex stitches to create detailed and intricate clothing. You can also add embellishments to the clothing, such as buttons, ribbons, or lace, to give it a unique look.
Materials for Hair and Clothing
Material |
Uses |
Yarn |
Hair, clothing |
Thread |
Hair |
Fabric scraps |
Clothing |
Beads |
Hair embellishments |
Ribbons |
Clothing embellishments |
Lace |
Clothing embellishments |
Structuring the Body of a Crochet Doll
1. Head and Neck
The head and neck form the foundation of the doll. Start by crocheting a sphere for the head, then add stitches to create the neck.
2. Arms
Crochet two identical rectangles for the arms. Fold them in half and sew the sides together to create tubes. Stuff the tubes and sew them to the body.
3. Legs
Similar to the arms, crochet two identical shapes for the legs. Sew the sides together and stuff them. Attach them to the body.
4. Torso
Crochet a cylindrical shape for the torso. The length and width will vary depending on the desired size of the doll.
5. Assembly
The following steps provide detailed instructions for assembling the body:
Step |
Description |
1 |
Sew the head to the neck. |
2 |
Sew the arms to the torso at the shoulders. |
3 |
Sew the legs to the torso at the hips. |
4 |
Stuff the entire body through the opening at the bottom of the torso. |
5 |
Close the opening by sewing it shut. |
Crafting Hands and Feet for Lifelike Movement
Establishing a Solid Foundation
Begin by crocheting a chain, forming it into a circle, and closing it with a slip stitch. Increase stitches as you work around, creating a base for your hands or feet.
Creating Fingers and Toes
Chain a smaller number of stitches and secure it to the base with a slip stitch. Repeat this process for each finger or toe, shaping them with decreases as necessary.
Joining Fingers and Toes
Use a slip stitch to connect each finger or toe to the thumb or heel. Ensure that the joins are secure and do not create any gaps.
Sculpting for Naturalism
Stuff the hands and feet with a soft material, such as polyester fiberfill. Use a sculpting tool or your fingers to shape the limbs, creating details like knuckles and arches.
Adding Details
Embroider or stitch on fingernails, toenails, and any other necessary details. These finishing touches will enhance the realism of your creation.
Finishing Touches
Using a crochet hook or yarn needle, sew the limbs to the body of your doll. Position them carefully to allow for lifelike movement and articulation.
|
Crochet Dolls: Crafting Hands and Feet for Lifelike Movement |
Materials |
Yarn, crochet hook, stuffing, sculpting tool or fingers, embroidery needle or yarn |
Tips |
Use a variety of stitch sizes to create dimension and detail; Stuff lightly for flexibility and movement; Secure all joins for durability |
Adding Details to Bring Your Dolls to Life
Embroidery: A Touch of Whimsy
Embroider intricate patterns onto your dolls’ clothing or accessories for a charming and personalized touch. Use colorful threads and experiment with different stitches to create unique designs.
Beading: Eyes That Sparkle
Adorn your dolls’ eyes with tiny beads. Use different colors and shapes to create realistic or whimsical expressions. Beads can also be used to decorate clothing, hats, and other accessories.
Buttons: Embracing the Tactile
Sew buttons onto your dolls’ clothing for a playful and interactive element. Buttons can be used as closures, embellishments, or even as decorative details on hats and shoes.
Ribbons: A Touch of Elegance
Tie ribbons around your dolls’ necks, wrists, or ankles to add a feminine or elegant touch. Ribbons can be used to create bows, sashes, or even hair accessories.
Lace: A Delicate Finish
Embellish your dolls’ clothing with delicate lace. Lace can be used to trim edges, create ruffles, or add a touch of vintage charm to their outfits.
Fabric Paint: Unleashing Creativity
Use fabric paint to add intricate designs or personalized touches to your dolls. Paint faces, clothing, or accessories with a wide range of colors and patterns.
Yarn Hair: Giving Life to Your Creations
Materials:
Yarn |
Scissors |
Yarn Needle |
3-ply worsted weight yarn |
Sharp scissors |
Large-eyed yarn needle |
Steps:
- Cut strands of yarn to desired hair length (approximately 10-15 inches).
- Fold a strand of yarn in half and thread it through the yarn needle.
- Insert the needle into the doll’s head at the desired hair location and pull the yarn through.
- Repeat steps 2-3 until the hair is full and evenly distributed.
- Tie the ends of the yarn together to secure the hair.
- Cut and style the hair as desired.
Amigurumi Style: The Art of Creating Rounded Dolls
Amigurumi, a Japanese crocheting technique, is characterized by its ability to create adorable, round-shaped dolls. These dolls are typically made with single crochet stitches worked in a continuous spiral, giving them their distinctive rounded appearance.
Materials:
Amigurumi dolls require a few basic materials:
- Yarn: Worsted weight yarn is most commonly used, but other yarn weights can be used to create different sizes of dolls.
- Crochet hook: The hook size should be appropriate for the yarn weight being used.
- Stuffing: Polyester fiberfill is a common choice for stuffing amigurumi dolls.
- Embroidery needle: This is used to sew on the doll’s features and details.
Basic Shape:
Amigurumi dolls are essentially 3D forms created by increasing and decreasing stitches in a strategic manner. The basic shape of an amigurumi doll typically consists of a head, body, and limbs.
Eyes and Nose:
Amigurumi dolls’ eyes and noses are often created using embroidery floss or safety eyes. Embroidery floss allows for a variety of eye and nose shapes, while safety eyes are a pre-made option that is easy to attach.
Clothing:
Amigurumi dolls can be customized with a wide range of clothing and accessories. These can be made using simple crochet stitches or more advanced techniques such as knitting or sewing.
Hair:
Hair can be added to amigurumi dolls using a variety of methods, including yarn, roving, or even fabric scraps. This allows for a wide range of hairstyles and colors.
Variations:
Amigurumi is a versatile technique that allows for endless variations. Dolls can be made in any size, shape, or color, and can be used as toys, decorative items, or collectibles.
Planning and Sketching:
Before starting an amigurumi project, it’s helpful to plan and sketch out the desired design. This will help ensure that the doll turns out the way you want it.
Gauge:
Gauge is an important factor in amigurumi. It’s recommended to check the gauge of your work before starting on the actual doll. This will ensure that the stitches are the correct size and the doll will turn out the correct size.
Embellishing Your Crochet Dolls with Accessories
Adding accessories to your crochet dolls can bring them to life and create a personalized and charming look. Here are some ideas to inspire your creativity:
Jewelry
Add a touch of sparkle with earrings, necklaces, or bracelets. Use small beads, wire, or fabric scraps to create unique and delicate adornments.
Hats and Headwear
Create a variety of hats to match your doll’s style. Try crocheting beanies, berets, or sun hats from yarn or fabric.
Scarves and Wraps
Keep your doll warm with a cozy scarf or wrap. Use soft yarn or fabric to create a fashionable accessory that adds texture.
Shoes and Socks
Give your doll a pair of shoes or socks to complete their outfit. Crochet them from yarn or felt, and add details like laces or buttons.
Bags and Purses
Create a miniature purse or bag to carry your doll’s essentials. Use crochet stitches or fabric to create a cute and functional accessory.
Wings and Tails
For a touch of whimsy, add wings or a tail to your doll. Use wire or felt to create a lightweight and durable accessory.
Stuffed Animals and Dolls
Give your doll a companion by crocheting a miniature stuffed animal or doll. This will add an extra element of cuteness and personality to its collection.
Embroidery
Add intricate details to your doll’s clothes or accessories with embroidery. Use yarn or thread to create patterns, designs, or even facial features.
Fabric and Trims
Enhance your doll’s look with fabric scraps and trims. Use lace, ribbon, or buttons to create frills, embellishments, or decorative details.
Tips for Embellishing Crochet Dolls:
Tip |
Details |
Use a variety of materials |
Experiment with yarn, fabric, wire, and beads to create unique and interesting accessories. |
Secure embellishments securely |
Use glue, thread, or wire to ensure your accessories stay in place during play or display. |
Consider the scale |
Make sure your accessories are appropriately sized for your doll’s body and clothing. |
Troubleshooting Common Challenges in Crochet Doll-Making
Uneven Stitching
Varying stitch tension can result in uneven or irregular stitches. Focus on maintaining a consistent yarn tension and using the correct hook size for your yarn weight.
Loose, Gappy Stitches
This issue is often caused by using a hook size that is too large for the yarn weight. Make sure your hook size is appropriate and crochet the stitches tightly.
Tight, Stiff Stitches
Tight stitches can result from using a hook that is too small or from pulling the yarn too tightly. Use the correct hook size and relax your grip on the yarn.
Gaps Between Rounds
Gaps can occur if your stitches are not joined securely in the round. Make sure to insert the hook into both loops of each stitch when crocheting in the round.
Parts Falling Off
This issue can be caused by loose or broken stitches. Ensure your stitches are secure and do not overstuff the doll to prevent seams from stretching and breaking.
Droopy or Deformed Head/Body
Uneven stuffing or using too much stuffing can cause the head or body to become misshapen. Stuff it firmly but evenly, and consider using a shaping tool to achieve the desired shape.
Eyes or Other Embellishments Falling Out
Secure embellishments, such as eyes and buttons, by sewing them on tightly or using glue designed for fabric. Avoid using hot glue, as it can damage the doll’s material.
Mismatched or Inconsistent Features
Carefully count your stitches and follow the pattern closely to ensure the doll’s features are symmetrical and consistent. If necessary, use stitch markers to keep track of the stitch count.
Excess Yarn Tails
Leave sufficient yarn tails to secure the pieces together, but trim them neatly to avoid a messy appearance. Use a tapestry needle to weave in any loose ends.
Time and Effort Requirement
Crocheting dolls typically requires time and patience. Set realistic expectations, schedule breaks, and don’t get discouraged if it takes longer than anticipated.
Crochet Dolls: A Crafting Journey
Crochet dolls have captured the hearts of crafters and collectors alike, providing endless opportunities for creativity and self-expression. The art of crocheting dolls involves using a hook to manipulate yarn into intricate shapes, creating adorable and unique characters. Whether you’re a seasoned crafter or just starting out, the world of crochet dolls offers endless possibilities.
To embark on your crochet doll-making adventure, you’ll need basic crochet supplies: yarn, a crochet hook, a needle for sewing, and stuffing material. With practice, you can master fundamental crochet stitches such as the single crochet, double crochet, and slip stitch, which form the building blocks of your creations. Beginner-friendly patterns guide you through the process, allowing you to create your first doll step-by-step.
As you progress, you can experiment with different yarns and textures, personalizing your dolls to reflect your style. Choose soft and cuddly yarns for comforting dolls, or opt for metallic threads for a touch of glamour. Add intricate details such as embroidered faces, yarn hair, and crocheted accessories to bring your dolls to life.
People Also Ask About Crochet Dolls How To
Can I sell crochet dolls I make?
Yes, you can sell crochet dolls you make as long as you own the copyright to the pattern or have permission to use it. Ensure you comply with any applicable laws and regulations related to selling handmade products.
How do I price my crochet dolls?
Consider the time, materials, and skill involved in creating your dolls. Research similar products on the market and factor in your business expenses to determine a fair price that reflects the value of your work.
Where can I find crochet doll patterns?
Numerous online resources offer free and paid crochet doll patterns. Websites like Ravelry, Etsy, and Pinterest host a vast collection of patterns catering to all skill levels. You can also find inspiration in books, magazines, and crochet communities.