
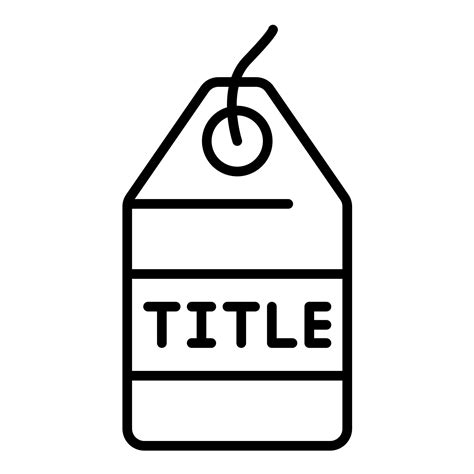
Electrical problems in your vehicle can be a real pain, especially when they’re caused by a parasitic draw. A parasitic draw is when your car’s battery is being drained by something even when the car is turned off. This can be caused by a number of things, such as a faulty alternator, a bad battery, or a short circuit. If you’re experiencing electrical problems in your vehicle, it’s important to test for a parasitic draw so you can find and fix the problem.
There are a few different ways to test for a parasitic draw. One way is to use a multimeter. To do this, you’ll need to disconnect the negative battery terminal from your car’s battery. Then, connect the multimeter’s positive lead to the negative battery terminal and the multimeter’s negative lead to a ground. If the multimeter reads anything other than 0, then you have a parasitic draw. Another way to test for a parasitic draw is to use a clamp-on ammeter. To do this, you’ll need to clamp the ammeter around the negative battery cable. If the ammeter reads anything other than 0, then you have a parasitic draw.
Once you’ve confirmed that you have a parasitic draw, you’ll need to find the source of the problem. To do this, you’ll need to start by removing fuses one at a time until the parasitic draw goes away. Once you’ve found the fuse that’s causing the problem, you’ll need to determine which circuit that fuse is responsible for. You can do this by referring to your vehicle’s owner’s manual. Once you know which circuit is causing the problem, you can start to troubleshoot the problem and find the source of the parasitic draw.
The Basics of Parasitic Draw
Parasitic draw is a condition where an electrical component or system continues to draw power from the battery even when the vehicle is turned off. This can lead to a drained battery and, in some cases, can even cause the vehicle to not start. Parasitic draw can be caused by a variety of factors, including:
Electrical accessories: Electrical accessories, such as lights, radios, and power outlets, can continue to draw power from the battery even when they are turned off. This is because these accessories are often connected to the battery through a constant power source, which allows them to receive power even when the ignition is off.
Electrical faults: Electrical faults, such as short circuits and faulty wiring, can also cause parasitic draw. Short circuits occur when two wires come into contact with each other, allowing electricity to flow through them uncontrolled. Faulty wiring can also cause parasitic draw, as it can allow electricity to leak from wires.
Aftermarket electrical devices: Aftermarket electrical devices, such as remote starters and security systems, can also cause parasitic draw. These devices are often connected to the battery through a constant power source, which allows them to receive power even when the ignition is off. If these devices are not installed properly, they can draw power from the battery and lead to a drained battery.
Cause |
Symptoms |
Diagnosis |
Electrical accessories |
Battery drain, lights or radio staying on |
Disconnect accessories and test for draw |
Electrical faults |
Battery drain, wires getting hot |
Inspect wiring for damage or shorts |
Aftermarket electrical devices |
Battery drain, remote starter staying on |
Disconnect aftermarket devices and test for draw |
Identifying Potential Parasitic Draw Symptoms
Electrical System Malfunctions
Parasitic draw can manifest through various electrical system issues. Following are a few common symptoms:
–
Slow or difficult engine cranking
–
Battery draining or going flat even when the vehicle is parked
–
Sudden battery discharge after sitting for a while
–
Headlights or interior lights dimming or flickering
–
Unusual battery heat or bloating
Unusual Electronic Behavior
Beyond electrical system issues, parasitic draw can lead to strange electronic behavior, including:
–
Random activation of electrical components, such as headlights or wipers
–
Difficulty starting the vehicle even after jump-starting
–
Malfunctioning or erratic gauges or displays
–
Unusual noises coming from electrical components
Other Signs of Parasitic Draw
In addition to the electrical and electronic symptoms, parasitic draw can also cause other observable issues:
–
A parasitic draw can cause the engine to run rough or stall
–
The vehicle may experience reduced fuel efficiency
–
The vehicle’s performance may be affected, such as acceleration or braking
Utilizing an Amp Clamp for Draw Measurement
Measuring parasitic draw with an amp clamp involves placing the clamp around the battery’s negative terminal wire. The clamp should be positioned as close to the battery as possible, ensuring that no other wires pass through its opening. Once secured, set the clamp to the appropriate amperage range, typically 10 amps or higher.
With the clamp in place, activate the vehicle’s parasitic draw mode by putting it in sleep mode. Refer to the vehicle’s service manual for specific instructions on how to enter this mode. Once in sleep mode, wait a few minutes for the vehicle’s systems to fully power down.
Now, read the amp clamp display. A normal parasitic draw value ranges from 20 to 50 milliamps (mA) for most vehicles. Any reading consistently above this threshold indicates a parasitic draw issue that should be investigated further.
To isolate the source of the parasitic draw, consult a wiring diagram for the vehicle and start by disconnecting fuses one at a time while monitoring the amp clamp reading. The fuse that causes the amp clamp reading to drop significantly when removed identifies the circuit containing the parasitic draw source.
Below is a table summarizing the steps involved in using an amp clamp for parasitic draw measurement:
Step |
Description |
1 |
Connect the amp clamp around the battery’s negative terminal wire. |
2 |
Set the clamp to the appropriate amperage range. |
3 |
Activate the vehicle’s parasitic draw mode and wait for systems to power down. |
4 |
Read the amp clamp display and compare the value to known normal ranges. |
5 |
Disconnect fuses to isolate the circuit causing the parasitic draw. |
Step-by-Step Parasitic Draw Testing
Before diving into the testing process, gather the necessary equipment: a multimeter, a 12-volt test light, and a jumper wire.
1. Disconnect the Negative Battery Terminal
With the engine turned off, pop the hood and locate the negative battery terminal. Use a wrench to loosen the nut and remove the negative battery cable.
2. Set Up the Multimeter
Turn the multimeter to the DC current (amps) setting. Connect the positive (red) lead to the negative battery post, and the negative (black) lead to the disconnected battery cable.
3. Connect the Test Light
Clip the alligator clip of the test light to the negative battery post. Hold the pointed end of the test light probe in the loop of the jumper wire.
4. Systematic Testing
This part of the test involves systematically checking each fuse location for a parasitic draw. Here’s a detailed guide:
Step |
Procedure |
a. |
Insert the jumper wire into the fuse slot for the first circuit. |
b. |
Observe the multimeter reading. If the reading drops below 0.05 amps, that circuit may have a parasitic draw. |
c. |
Remove the jumper wire and insert it into the next fuse slot. |
d. |
Repeat steps b and c for each fuse location until a significant parasitic draw is identified. |
Isolate Circuit Suspects with Fuse Pull Method
With the systematic fuse pull method, you methodically disconnect potential sources of parasitic draw by removing fuses one at a time. Here’s how it works:
- Gather Tools: You’ll need a multimeter, fuses of the correct amperage, and a fuse puller.
- Prepare Multimeter: Set the multimeter to DC milliamp (mA) mode. Connect the red lead to the positive terminal and the black lead to the negative terminal.
- Disconnect Negative Battery Terminal: Remove the negative battery terminal to prevent any electrical shocks.
- Connect Multimeter to Battery: Connect the multimeter leads to the negative battery terminal and a good ground on the chassis.
- Test Current Draw: Turn off all lights and accessories and wait for the parasitic draw to stabilize (usually around 30 minutes). Record the current draw displayed on the multimeter.
- Pull Fuses Individually: With the multimeter still connected, start pulling fuses one at a time, beginning with non-essential circuits.
- Monitor Current Draw: As you pull each fuse, observe the current draw on the multimeter. If the current draw drops significantly, you have likely isolated the circuit responsible for the parasitic draw.
- Identify Suspect Circuit: Once you’ve identified the circuit, refer to the fuse box diagram to determine the components or modules connected to that circuit.
- Inspect Suspect Circuit: Physically inspect the suspect circuit for damaged or faulty components, loose connections, or any other issues that may be causing the parasitic draw.
- Confirm Diagnosis: Reinsert the pulled fuse and check the current draw again. If the current draw rises, your diagnosis is confirmed.
Fuse Number |
Circuit Description |
Current Draw (mA) |
5 |
Radio |
15 |
10 |
Clock |
5 |
15 |
Power Windows |
30 |
20 |
Security System |
1 |
Apply the Voltage Drop Test for Corroded Connections
Corroded connections are a common cause of parasitic draw. To test for a corroded connection, perform a voltage drop test.
Materials Required
- Digital multimeter
- Wire probes
Procedure
- Ensure the vehicle is in the "OFF" position and all accessories are turned off.
- Connect the positive lead of the multimeter to the battery positive terminal.
- Connect the negative lead of the multimeter to the bolt, nut, or other connection point of the component being tested.
- Set the multimeter to the DC voltage setting.
- Observe the voltage reading.
Interpretation of Results
- Voltage drop of 0.5 volts or less: No significant corrosion is present.
- Voltage drop of 0.5 to 1.0 volt: Minor corrosion is present, requiring attention.
- Voltage drop of more than 1.0 volt: Severe corrosion is present, potentially causing parasitic draw.
Voltage Drop |
Corrosion Level |
0.5 volts or less |
No significant corrosion |
0.5 to 1.0 volt |
Minor corrosion |
More than 1.0 volt |
Severe corrosion |
Additional Considerations
- If a voltage drop is detected, visually inspect the connection for signs of corrosion.
- Clean and repair any corroded connections by removing the corrosion and applying anti-corrosion lubricant.
- Repeat the voltage drop test to verify the effectiveness of the repair.
Uncover Latent Parasitic Draw with Battery Disconnect
7. Identifying Specific Drain Sources
To pinpoint the exact component responsible for the parasitic draw, you can use a digital multimeter to measure the current draw from individual components. Start by disconnecting all aftermarket accessories and then reconnect them one at a time, measuring the current draw each time.
Another effective technique is to use a circuit tester with a parasitic draw mode. This device can identify the offending component by injecting a known current into the circuit and measuring the resulting voltage drop. The component with the highest voltage drop is likely the source of the parasitic draw.
If you are unable to locate the parasitic draw using these methods, you may need to consult with a qualified automotive electrician. They may have access to more advanced diagnostic tools and experience in troubleshooting electrical issues.
Step |
Description |
1 |
Disconnect battery |
2 |
Connect multimeter in series |
3 |
Measure current draw |
4 |
Reconnect components individually |
5 |
Use circuit tester with parasitic draw mode |
6 |
Identify component with highest voltage drop |
7 |
Consult with electrician if needed |
Calibrate Battery Disconnect Reading for Accuracy
To ensure accurate readings, it’s crucial to calibrate the battery disconnect meter. Here are the detailed steps:
1. Disconnect the Battery
Disconnect the negative terminal of the battery using a wrench. Wait a few minutes to allow the electrical systems to discharge.
2. Connect the Ammeter
Connect the digital ammeter in series between the disconnected battery terminal and the battery cable. Ensure a secure connection with good conductivity.
3. Set Ammeter to DC Range
Select the DC range on the ammeter that accommodates the anticipated current draw. Start with a higher range and adjust to a lower range if needed.
4. Measure Ambient Temperature
Record the ambient temperature using a thermometer. This information is essential for compensating for temperature variations in the reading.
5. Reset Ammeter to Zero
With the ammeter connected, hold down the “Zero” button on the meter until the display reads zero. This eliminates any offset or baseline error.
6. Reconnect Battery Terminal
Reconnect the negative battery terminal. The ammeter should display a negative reading, indicating the current draw from the parasitic systems.
7. Allow Systems to Stabilize
Wait a few minutes for the electrical systems to stabilize after reconnecting the battery. This allows any modules or systems that may have initially drawn excessive current to settle down.
8. Record and Adjust for Temperature
Record the current draw reading from the ammeter. To adjust for temperature variations, multiply the reading by the appropriate temperature compensation factor provided in the following table:
Temperature Range (°C) |
Compensation Factor |
-10 to 0 |
1.2 |
0 to 10 |
1.1 |
10 to 20 |
1.0 |
20 to 30 |
0.9 |
30 to 40 |
0.8 |
Identifying Ground Faults and Short Circuits
A ground fault occurs when the electrical current escapes from a wire and flows through an unintended path, such as the ground or a metal frame. This can be caused by damaged insulation, loose connections, or faulty wiring. Ground faults can be dangerous, as they can cause electrical shocks and fires.
A short circuit occurs when the electrical current takes a shortcut through a low-resistance path, such as a wire or a metal object. This can cause the circuit to overload and trip the breaker or fuse. Short circuits can also be dangerous, as they can cause overheating and fires.
There are a few ways to test for ground faults and short circuits. One way is to use a multimeter to measure the resistance between the electrical wire and the ground. If the resistance is low, it indicates a ground fault. Another way to test for ground faults is to use a ground fault circuit interrupter (GFCI). A GFCI is a device that detects ground faults and trips the circuit to prevent electrical shocks.
To test for short circuits, you can use a multimeter to measure the voltage and current in the circuit. If the voltage is low and the current is high, it indicates a short circuit. You can also use a continuity tester to check for short circuits. A continuity tester is a device that checks for complete circuits. If there is a short circuit, the continuity tester will beep.
Troubleshooting Ground Faults and Short Circuits
If you find a ground fault or short circuit, it is important to fix it as soon as possible. Ground faults and short circuits can be dangerous, and they can also damage your electrical system. To fix a ground fault, you may need to replace the damaged wire or insulation. To fix a short circuit, you may need to replace the damaged wire or fuse.
Here are some tips for troubleshooting ground faults and short circuits:
- Turn off the power to the circuit.
- Check for any visible damage to the wires or insulation.
- Use a multimeter to test for ground faults and short circuits.
- Fix the problem by replacing the damaged wire or insulation.
- Turn the power back on to the circuit.
Ground Faults |
Short Circuits |
Electrical current escapes from a wire and flows through an unintended path.
|
Electrical current takes a shortcut through a low-resistance path.
|
Can cause electrical shocks and fires.
|
Can cause circuit overloads and fires.
|
Tested using a multimeter or a GFCI.
|
Tested using a multimeter or a continuity tester.
|
Fixed by replacing the damaged wire or insulation.
|
Fixed by replacing the damaged wire or fuse.
|
Essential Safety Considerations for Parasitic Draw Testing
1. Disconnect Negative Battery Terminal
Before starting any parasitic draw testing, always disconnect the negative battery terminal. This will prevent any electrical shocks or damage to the vehicle’s electrical system.
2. Wear Eye Protection
When using a multimeter to test for parasitic draw, it is important to wear eye protection. Multimeters can produce high voltages, and if they come into contact with your eyes, they can cause serious injury.
3. Use Insulated Tools
Always use insulated tools when working on the vehicle’s electrical system. This will protect you from electrical shocks.
4. Be Aware of Your Surroundings
When testing for parasitic draw, be aware of your surroundings. Make sure there are no flammable materials or liquids nearby.
5. Use a Multimeter with a Low Amperage Range
When testing for parasitic draw, it is important to use a multimeter with a low amperage range. This will help you to accurately measure the amount of current that is being drawn from the battery.
6. Connect the Multimeter Correctly
When connecting the multimeter to the vehicle’s electrical system, it is important to connect the positive lead of the multimeter to the positive terminal of the battery and the negative lead of the multimeter to the negative terminal of the battery.
7. Set the Multimeter to the Correct Function
When testing for parasitic draw, it is important to set the multimeter to the correct function. The multimeter should be set to the DC current function.
8. Zero the Multimeter
Before starting to test for parasitic draw, it is important to zero the multimeter. This will ensure that the multimeter is giving you accurate readings.
9. Take Measurements
Once the multimeter is set up correctly, you can start to take measurements. To take a measurement, simply place the positive lead of the multimeter on the positive terminal of the battery and the negative lead of the multimeter on the negative terminal of the battery.
10. Interpret the Results
The multimeter will display the amount of current that is being drawn from the battery. If the current draw is more than 50 milliamps, then there is likely a parasitic draw on the vehicle’s electrical system. The following table lists some common causes of parasitic draw:
Cause |
Typical Current Draw |
Interior lights left on |
5-10 amps |
Trunk light left on |
1-2 amps |
Faulty alternator |
1-5 amps |
Faulty ignition switch |
0.5-1 amp |
Faulty relay |
0.1-0.5 amps |
How to Test for Parasitic Draw
Step 1: Turn Off All Accessories
The first step in testing for parasitic draw is to turn off all accessories, including lights, radio, and air conditioning. This will ensure that the only power draw is from the vehicle’s essential systems.
Step 2: Disconnect Negative Battery Terminal
Next, disconnect the negative battery terminal. This will break the circuit and prevent any current from flowing.
Step 3: Connect Multimeter in Series
Connect a multimeter in series between the negative battery terminal and the battery. The multimeter should be set to measure DC current.
Step 4: Wait 30 Minutes
Wait 30 minutes for the vehicle’s systems to settle down. This will give any parasitic draw time to manifest.
Step 5: Read Multimeter
Read the multimeter to determine the parasitic draw. A normal parasitic draw is typically less than 50 milliamps (mA). Anything above this level may indicate a parasitic draw issue.
Troubleshooting Tips
If you detect a parasitic draw, you can use the following tips to troubleshoot the source:
-
Use a fuse puller to remove fuses one at a time. When you find the fuse that stops the parasitic draw, it is likely that the circuit associated with that fuse has a problem.
-
Inspect the wiring harness for any damage or loose connections. Look for any frayed wires, melted insulation, or loose connectors.
-
Check the alternator for any signs of damage or malfunction. A faulty alternator can cause a parasitic draw.
People Also Ask About How to Test Parasitic Draw:
What are the symptoms of a parasitic draw?
Symptoms of a parasitic draw can include:
– Difficulty starting the vehicle
– Rapid battery discharge
– Dimming headlights
– Malfunctioning electrical components
What are the most common causes of parasitic draw?
Common causes of parasitic draw include:
– Faulty alternator
– Damaged wiring harness
– Accessories left on
– Aftermarket electrical devices
How can I prevent parasitic draw?
To prevent parasitic draw, you can:
– Turn off all accessories when not in use
– Inspect the wiring harness regularly for damage or loose connections
– Have the alternator tested and replaced if necessary
– Avoid installing aftermarket electrical devices that could draw excessive current