
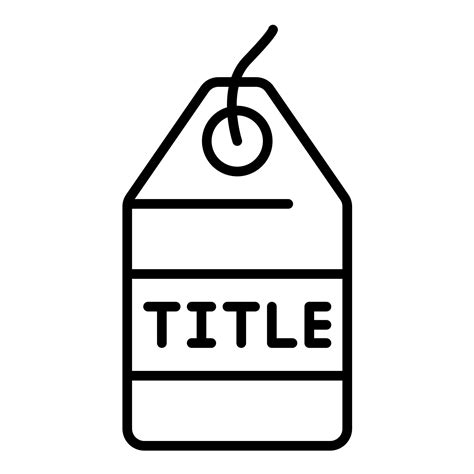
In the realm of home décor and DIY projects, the fusion of fabric and wood holds endless possibilities for transforming spaces and creating unique pieces. Whether you’re embellishing furniture, reupholstering surfaces, or crafting custom décor, knowing how to seamlessly bond these two materials is essential. In this article, we will guide you through the process of gluing fabric to wood with precision and durability. Discover the methods, tools, and techniques involved in achieving a крепкое bond that will withstand the test of time.
When choosing the right adhesive for gluing fabric to wood, the type of fabric and the intended use of the item play a crucial role. For general applications, a water-based adhesive such as Mod Podge or Elmer’s Glue-All will suffice. These adhesives provide a крепкое, flexible bond that dries clear and is resistant to moisture. For heavier fabrics or surfaces that will experience significant wear and tear, a stronger adhesive such as epoxy or contact cement is recommended. These adhesives create a permanent bond that is water-resistant and can withstand high stress. Additionally, you may want to consider using a fabric stiffener, such as starch or a fabric stiffener spray, if your fabric tends to fray or wrinkle easily.
Before applying the adhesive, it’s essential to prepare both the fabric and the wood surface. Ensure the wood surface is clean, dry, and free of any dirt or debris. Sanding the surface lightly can help create a better bond. Similarly, the fabric should be clean and free of any wrinkles or creases. Ironing the fabric before gluing can help achieve a smoother finish. Once the preparation is complete, spread a thin, even layer of adhesive onto the wood surface using a brush or roller, avoiding any air bubbles. Carefully place the fabric onto the adhesive-covered surface, smoothing it out gently to remove any wrinkles or folds. Weight the fabric down with heavy objects or clamps to ensure a крепкое bond. Allow the glue to dry completely, which may take several hours or even overnight, depending on the type of adhesive and the thickness of the fabric.
Materials and Preparation
Materials
Before embarking on this project, it is essential to gather the appropriate materials. The primary component is a suitable adhesive specifically formulated for bonding fabric to wood.
Fabric glue is a specialized type of adhesive designed to adhere fabric to various surfaces, including wood. It is vital to select a high-quality glue that provides a strong and durable bond. Look for adhesives that are clear or translucent, as this will minimize visibility after application.
Additional materials required include:
- Clean paintbrush or sponge for applying the glue
- Scissors or rotary cutter for precise fabric cutting
- Measuring tape or ruler for accurate fabric placement
- Weight or clamps for firmly holding the fabric in place during the bonding process
- Soft, clean cloth or paper towels for wiping away excess glue
It is also worth considering the following:
Optional Tools |
Purpose |
Iron and ironing board |
Help smooth out fabric and eliminate wrinkles before gluing |
Masking tape |
Protect areas of wood that should not receive glue |
Craft knife |
Trim excess fabric after gluing |
Preparation
Adequate preparation ensures a successful bonding experience. Begin by thoroughly cleaning both the fabric and the wood surface. Removing any dirt, dust, or oils will enhance the adhesive’s performance.
Next, measure and cut the fabric to the desired size and shape. If necessary, iron the fabric to remove wrinkles.
Position the fabric on the wood surface and secure it in place using weights or clamps. This prevents the fabric from shifting during the gluing process.
Applying Fabric To Wood
The initial step is to gather the necessary materials: fabric, wood, glue, a paintbrush or sponge, weights or clamps, and scissors. Ensure the wood surface is clean and dry before applying the fabric. Cut the fabric to the desired size and shape, ensuring it is slightly larger than the wood surface to allow for folding over the edges. Apply a thin layer of glue to the wood surface using a paintbrush or sponge.
Tips for Applying Fabric to Wood
When applying fabric to wood, there are a few key tips to ensure a strong and durable bond.
- Choose the right fabric. Not all fabrics are suitable for gluing to wood. Some fabrics, such as those with a high pile or stretch, may not adhere well to the wood surface and may wrinkle or bubble over time. It is best to use a fabric that is relatively thin and has a smooth texture.
- Prepare the wood surface. Before applying the fabric, it is important to prepare the wood surface properly. This involves sanding the surface smooth to remove any splinters or unevenness and cleaning the surface with a damp cloth to remove any dust or debris.
- Apply the glue evenly. When applying the glue to the wood surface, it is important to do so evenly. This will help to ensure a strong bond between the fabric and the wood and will prevent the fabric from bubbling or peeling over time.
- Press the fabric firmly. Once the glue has been applied to the wood surface, the fabric should be pressed firmly into place. This will help to remove any air bubbles and will ensure that the fabric adheres to the wood properly.
- Allow the glue to dry completely. Once the fabric has been pressed into place, it is important to allow the glue to dry completely before using the item. This will help to ensure that the bond between the fabric and the wood is strong and durable.
Ensuring Secure Bonding
Properly adhering fabric to wood requires careful preparation and adhesive selection. Here are some essential tips to ensure a strong and lasting bond:
Surface Preparation
- Sand the wooden surface lightly to create a rougher texture for better adhesion.
- Clean both the fabric and the wood with a damp cloth to remove any dust or debris that could interfere with bonding.
- Allow both surfaces to dry completely before applying any adhesive.
Adhesive Selection
Choosing the right adhesive is crucial for achieving a secure bond. Consider the following factors:
- Type of fabric: Some adhesives are specifically designed for delicate fabrics or heavy-duty materials.
- Wood surface: The type of wood, whether it is porous or non-porous, will influence the adhesive’s performance.
- Intended use: The bond’s strength and durability requirements will determine the best adhesive option.
Common adhesives for gluing fabric to wood include:
Adhesive Type |
Pros |
Cons |
Wood Glue |
Strong, durable, dries clear |
Can be difficult to spread evenly |
Fabric Glue |
Easy to use, flexible |
May not be as strong as other adhesives |
Epoxy |
Very strong, waterproof |
Can be messy and difficult to apply |
Applying the Adhesive
- Apply a thin, even layer of adhesive to both the fabric and the wood surface.
- Spread the adhesive using a brush, roller, or spatula.
- Allow the adhesive to become tacky before pressing the fabric onto the wood.
Follow the manufacturer’s instructions for cure time and any necessary clamping or heat setting.
Choosing the Right Adhesive
Selecting the appropriate adhesive is crucial for a strong and durable bond between fabric and wood. Different types of adhesives are available, each with unique properties and applications. Here’s an overview of the most commonly used adhesives:
Permanent adhesives provide a strong and lasting bond that is resistant to heat, moisture, and solvents. However, they are difficult to remove once applied.
Type |
Characteristics |
Applications |
Epoxy |
High strength, waterproof, solvent-resistant |
Structural bonding, repairs |
Cyanoacrylate (Super Glue) |
Fast-acting, low viscosity |
Small repairs, delicate fabrics |
Solvent-Based Contact Cement |
Strong bond, requires clamping |
Automotive trim, upholstery |
Removable adhesives allow for repositioning or removal of the fabric without damaging the wood. They are often used for temporary or non-critical applications.
Type |
Characteristics |
Applications |
Water-Soluble Adhesives |
Bond washes out with water |
Temporary bonding, basting |
Double-Sided Tape |
Pre-applied adhesive, easy to use |
Non-critical bonding, photo mounting |
Adhesive Sprays |
Temporary hold, repositionable |
Drafting, design work |
Specialized adhesives are designed for specific applications, such as working with delicate fabrics or outdoor projects.
Type |
Characteristics |
Applications |
Fabric Glue |
Clear, flexible, designed for fabrics |
Appliqué, hem bonding |
Marine Adhesive |
Waterproof, UV-resistant |
Outdoor furniture, boat upholstery |
Heat-Activated Adhesive Sheets |
Bond with heat, no liquid adhesive |
Apparel bonding, crafts |
When choosing an adhesive, consider the following factors:
- Type of Fabric: Delicate fabrics may require specialized adhesives, while heavy-duty fabrics can withstand stronger adhesives.
- Surface Area: Larger surface areas require more adhesive or a stronger adhesive.
- Load: The weight or force that will be placed on the bond determines the adhesive’s strength.
- Environment: Consider the temperature, humidity, and sunlight exposure to which the bond will be subjected.
- Reversibility: Determine if the bond needs to be permanent or removable.
Preparing the Wood Surface
Before gluing fabric to wood, it is essential to prepare the wood surface to ensure a strong and durable bond. Follow these steps to prepare the wood adecuadamente:
1. Clean the Surface
Begin by thoroughly cleaning the wood surface to remove any dirt, dust, or oil. Use a damp cloth or sponge with a mild detergent. Once cleaned, allow the surface to dry completely.
2. Sand the Surface
Sanding the wood surface creates a rougher texture that helps the glue adhere better. Use sandpaper with a grit of 150-220 and gently sand the surface in the direction of the wood grain. Avoid sanding too aggressively, as this can damage the wood.
3. Remove Sanding Dust
Once sanding is complete, use a vacuum cleaner or a damp cloth to remove the sanding dust thoroughly. Any remaining dust can prevent the glue from bonding properly.
Method |
Tools |
Steps |
Manual Brushing |
Brush |
Dip the brush into the glue and apply it evenly to the wood surface. |
Roller Application |
Paint Roller |
Pour the glue into a paint tray and use a roller to spread it onto the wood surface. |
Spreading with a Spatula |
Spatula or Trowel |
Apply glue directly onto the wood surface and use a spatula or trowel to spread it evenly. |
4. Apply a Thin Layer of Glue
Using a brush, roller, or spatula, apply a thin, even layer of glue to the wood surface. Choose a glue specifically designed for bonding fabric to wood, such as wood glue or fabric glue. Avoid applying too much glue, as this can weaken the bond.
5. Allow the Glue to Dry Slightly
After applying the glue, allow it to dry for a few minutes until it becomes tacky to the touch. This will help prevent the fabric from slipping when you apply it. The drying time may vary depending on the type of glue used. Refer to the glue manufacturer’s instructions for specific drying times.
Techniques for Fabric Application
Surface Preparation
Before gluing the fabric to the wood, ensure both surfaces are clean and dry. Sand the wood lightly to create a slightly rough surface for better adhesion.
Fabric Selection and Cutting
Choose a fabric with a suitable texture and thickness for your project. Cut the fabric according to the desired shape and size.
Glue Application
Apply a thin, even layer of wood glue to the prepared wood surface. Avoid using too much glue, as it can seep through the fabric or cause wrinkles.
Fabric Placement
Position the fabric on the glued wood surface, smoothing it out to remove any air bubbles. Gently press down on the fabric to ensure it adheres evenly.
Adhesive Techniques
- Contact Cement: Provides a strong, permanent bond when applied to both surfaces and allowed to dry partially before bonding. Use a thin layer and apply pressure evenly.
- Fabric Glue: Specifically formulated for fabric bonding, creating a flexible yet durable hold. Apply it directly to the fabric and press it onto the wood surface.
- Mod Podge: A versatile adhesive and sealant that can also embellish the fabric. Apply a layer of Mod Podge to the fabric and attach it to the wood.
- Iron-On Adhesive: A heat-activated adhesive that requires ironing the fabric onto the wood. Follow the specific instructions on the adhesive packaging.
- Spray Adhesive: Creates a quick and temporary bond, allowing for adjustments before the adhesive fully dries. Use it for lightweight fabrics on small areas.
- Stapling or Tacking: A mechanical method of securing the fabric to the wood using staples or tacks. Use a short spacing between staples or tacks.
Curing and Finishing
Allow the glue to dry thoroughly according to the manufacturer’s instructions. For contact cement, it may require longer curing time. Once dry, you can trim any excess fabric and add any necessary embellishments.
Finishing Touches
After the glue has dried completely, you can add finishing touches to enhance the appearance of your project.
9. Enhancing the Surface
To protect and enhance the fabric-covered wood surface, you can apply a variety of finishes:
Finish |
Properties |
Polyurethane |
Clear, durable protective coating that resists UV fading and moisture |
Acrylic Sealer |
Water-based, non-yellowing sealant that dries clear to maintain the fabric’s original color |
Decoupage Medium |
Transparent adhesive that seals and protects the fabric, creating a glossy finish |
Mod Podge |
Versatile adhesive that can be used as a sealant, glue, or decoupage medium, available in matte, glossy, and dimensional finishes |
Apply the chosen finish evenly over the fabric surface using a brush or sponge. Allow it to dry thoroughly according to the manufacturer’s instructions.
Tips and Tricks
1. Choose the Right Glue
The type of glue you use will depend on the type of fabric and wood you are gluing. For example, wood glue is a good choice for gluing wood to wood, but it is not as effective on fabric. Fabric glue, on the other hand, is designed to bond fabric to fabric, but it can also be used to glue fabric to wood.
2. Prepare the Surfaces
Before you begin gluing, it is important to prepare the surfaces of the fabric and wood. This means cleaning them with a damp cloth to remove any dirt or debris. You may also want to sand the wood lightly to create a rougher surface for the glue to bond to.
3. Apply the Glue
Once the surfaces are prepared, you can apply the glue. Be sure to apply a thin, even layer of glue to both the fabric and the wood. You can use a brush, a sponge, or even your fingers to apply the glue.
4. Press the Surfaces Together
Once the glue has been applied, press the surfaces of the fabric and wood together. Be sure to apply even pressure over the entire surface. You may want to use a clamp or a weight to hold the surfaces together while the glue dries.
5. Allow the Glue to Dry
The drying time for glue will vary depending on the type of glue you are using. Be sure to read the manufacturer’s instructions carefully. Once the glue has dried, the fabric and wood will be permanently bonded together.
6. Trim the Excess Fabric
Once the glue has dried, you may need to trim any excess fabric. You can use a sharp knife or a pair of scissors to do this.
7. Sand the Edges
If the edges of the fabric are rough, you may want to sand them smooth. This will help to prevent the fabric from fraying.
8. Stain or Paint the Wood
If you want to stain or paint the wood, you can do so once the glue has dried. Be sure to use a light touch when applying the stain or paint, so that you do not damage the fabric.
9. Protect the Fabric
If you are using the fabric-glued object outdoors, you may want to protect the fabric from the elements. You can do this by applying a sealant to the fabric.
10. Other Tips and Tricks
- Use a small amount of glue at first and add more as needed.
- If the glue is too thick, you can thin it with a little water.
- If the glue is too thin, you can thicken it with a little cornstarch.
- If you are gluing a large piece of fabric, you may want to apply the glue in sections.
- If you are gluing a delicate fabric, you may want to use a fabric adhesive instead of glue.
- If you are not sure how to glue fabric to wood, you can consult a professional.
How to Glue Fabric to Wood
Gluing fabric to wood can be a tricky task, but it is possible to achieve a strong and lasting bond with the right materials and techniques.
-
Choose the right glue. Not all glues are suitable for bonding fabric to wood. Some of the best options include wood glue, fabric glue, and epoxy.
-
Prepare the surfaces. The surfaces of the fabric and wood should be clean and dry before applying the glue. This will help the glue to adhere better.
-
Apply the glue. Apply a thin layer of glue to the surface of the wood. Then, press the fabric onto the glue and smooth it out.
-
Clamp the fabric in place. Use clamps to hold the fabric in place while the glue dries. This will help to ensure a strong bond.
-
Allow the glue to dry completely. The drying time will vary depending on the type of glue used. Once the glue is dry, the fabric will be securely attached to the wood.
People Also Ask About How to Glue Fabric to Wood
What is the best glue for gluing fabric to wood?
The best glue for gluing fabric to wood is a wood glue, fabric glue, or epoxy. These glues are strong and durable, and they will create a lasting bond between the fabric and the wood.
How do I prepare the surfaces before gluing fabric to wood?
The surfaces of the fabric and wood should be clean and dry before applying the glue. This will help the glue to adhere better. To clean the surfaces, you can use a damp cloth or a rubbing alcohol.
How long does it take for the glue to dry?
The drying time will vary depending on the type of glue used. Most wood glues will dry in about 24 hours, while fabric glues and epoxies will take longer to dry. It is important to allow the glue to dry completely before using the fabric item.