
Featured Image: 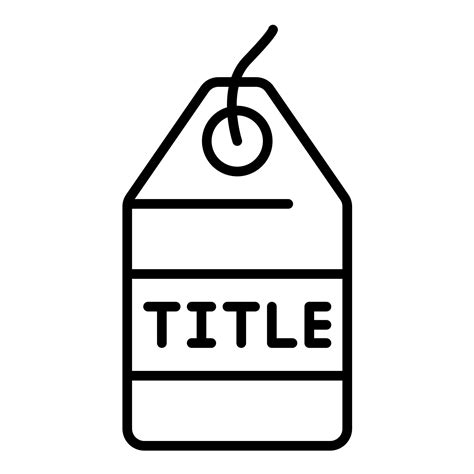
Experiencing a bumpy or unstable ride in your A90 Supra? Chassis stabilization issues can significantly hinder your driving experience and compromise safety. Identifying and resolving these problems is crucial for optimal performance and peace of mind. This guide will provide a comprehensive overview of common chassis stabilization issues affecting the A90 Supra, offering practical solutions to restore stability and enhance your driving experience.
One potential cause of chassis instability lies in worn or damaged suspension components. The Supra’s sophisticated suspension system relies on various interconnected parts, including springs, shock absorbers, control arms, and bushings. Over time, these components can deteriorate due to wear and tear, leading to reduced damping and impaired handling. Inspecting and replacing worn suspension parts can significantly improve stability and restore a more controlled ride.
Another common factor contributing to chassis instability is incorrect wheel alignment. Proper wheel alignment ensures that the tires make even contact with the road, distributing weight evenly and improving steering response. Misalignment can cause the car to pull to one side, exhibit uneven tire wear, and compromise stability. Regular wheel alignment checks and adjustments are essential to maintain chassis stability, ensuring optimal handling and tire longevity.
Calibrating the Alignment
A crucial step in addressing chassis stabilization issues with the A90 Supra is to ensure proper alignment. Here’s a detailed guide to guide you through the calibration process:
1. Inspect for Damage
Before any adjustments, thoroughly examine the chassis, suspension components, and tires for signs of damage, bending, or looseness. Address any issues promptly to avoid compromising the alignment process.
2. Gather Tools
You’ll need specialized alignment equipment, such as a four-wheel alignment machine, a spirit level, measuring rods, and a torque wrench. Ensure your tools are calibrated and in good working order.
3. Lift the Vehicle
Safely lift the vehicle onto a flat, stable surface using a hydraulic lift or jack stands. Allow ample space for proper access to the wheels.
4. Mount Measuring Equipment
Following the manufacturer’s guidelines, mount the four-wheel alignment machine’s sensors onto the appropriate reference points on each wheel. Connect the sensors to the main unit and initiate the measurement process.
Alignment Parameters |
Ideal Settings |
Front Toe |
0.05 degrees ± 0.15 degrees |
Rear Toe |
0.10 degrees ± 0.15 degrees |
Front Camber |
-0.5 degrees ± 0.25 degrees |
Rear Camber |
-0.5 degrees ± 0.25 degrees |
Front Caster |
6.5 degrees ± 1.0 degrees |
Rear Caster |
Not Adjustable |
Using the machine’s display, compare the measured parameters with the ideal settings for the A90 Supra as shown in the table above. Note any deviations from the specifications.
Continue to the next subsection to learn about adjusting the alignment settings.
Balancing the Tires
When tires are out of balance, they can cause vibrations in the chassis, which can lead to instability. To balance tires, you will need a tire balancing machine. Once the tires are mounted on the machine, it will rotate them and measure the amount of imbalance. The machine will then add weights to the tires to correct the imbalance.
There are two types of tire balancing: static balancing and dynamic balancing. Static balancing corrects the imbalance that occurs when the tire is not rotating. Dynamic balancing corrects the imbalance that occurs when the tire is rotating.
It is important to have your tires balanced regularly, especially if you notice any vibrations in the chassis. Unbalanced tires can cause premature wear on the tires and suspension components, and can also lead to instability.
Symptoms of Unbalanced Tires
Vibration in the steering wheel, seat, or floorboard |
Uneven tire wear |
Reduced fuel efficiency |
Difficulty steering |
Increased noise from the tires |
Upgrading to Performance-Oriented Suspension
To further enhance the chassis stability of the A90 Supra, consider upgrading to performance-oriented suspension components. These upgrades provide increased stiffness, control, and responsiveness to improve handling and cornering performance.
Coilover Suspensions
Coilover suspensions replace the factory struts and springs with independently adjustable coilover units. They allow for customization of ride height, spring rates, and damping, optimizing the suspension for specific driving conditions and track applications.
Adjustable Sway Bars
Adjustable sway bars control lateral body roll during cornering. Upgrading to thicker sway bars reduces body lean, improves cornering grip, and enhances vehicle stability under high-load situations.
Strut Tower Braces
Strut tower braces connect the strut towers on either side of the engine bay. They stiffen the front of the chassis, reducing flex and enhancing steering response and cornering precision.
Lowering Springs
Lowering springs lower the vehicle’s ride height, improving aerodynamics and reducing center of gravity. They also enhance cornering stability by reducing body roll and increasing mechanical grip.
Adjustable Control Arms
Adjustable control arms allow for fine-tuning of suspension geometry. They can optimize camber and toe settings, improving tire contact patch and enhancing overall handling and cornering performance.
Performance Dampers
Performance dampers, such as monotube shocks, provide increased damping force compared to factory shocks. They enhance ride quality, improve body control, and reduce dive and squat under acceleration and braking.
Suspension Component |
Benefits |
Coilover Suspensions |
Adjustable ride height, spring rates, and damping |
Adjustable Sway Bars |
Reduced body roll and improved cornering grip |
Strut Tower Braces |
Stiffened front chassis and enhanced steering response |
Lowering Springs |
Improved aerodynamics, reduced center of gravity, and reduced body roll |
Adjustable Control Arms |
Optimized suspension geometry and enhanced handling |
Performance Dampers |
Enhanced ride quality, body control, and reduced dive and squat |
Adjusting Brake Bias
Brake bias plays a critical role in stabilizing the A90 Supra’s chassis. By adjusting the bias, you can alter the distribution of braking force between the front and rear wheels, affecting the car’s handling and stability.
To adjust brake bias, you’ll need a brake bias adjuster. These devices can be purchased at most auto parts stores. Once you have an adjuster, follow these steps:
- Raise the rear of the Supra high enough so that the tires are off the ground.
- Connect the brake bias adjuster to the brake system.
- Start the engine and pump the brake pedal several times to build pressure.
- Adjust the bias knob to the desired setting. The lower the number, the more bias is applied to the rear wheels. The higher the number, the more bias is applied to the front wheels.
- Test the bias by applying moderate pressure to the brake pedal. The car should stop without pulling to one side or the other.
- Make small adjustments to the bias knob as needed until the car stops straight and true.
- Repeat the test several times to ensure the bias is correct.
Recommended Brake Bias Settings
The recommended brake bias settings for the A90 Supra vary depending on track conditions and driver preference. However, a good starting point is to set the bias to 50/50. This setting provides a good balance of front and rear braking power.
If the car is pulling to the left under braking, you can increase the rear bias to 60/40 or 70/30. This will help to stabilize the car under braking.
If the car is pulling to the right under braking, you can decrease the rear bias to 40/60 or 30/70. This will help to reduce the tendency for the car to pull to the right.
Track Conditions |
Recommended Brake Bias |
Dry |
50/50 |
Wet |
60/40 |
Snow/Ice |
70/30 |
Stiffening the Structural Reinforcement
Reinforcement in the Front End
Additional stiffening elements in the front end, such as strut tower braces, can significantly improve rigidity and handling. Front sway bars, anti-roll bars, and stiffer springs can further enhance stability.
Strengthening the Chassis
Undercarriage bracing, such as subframe connectors and chassis reinforcements, help reduce chassis flex and improve handling precision. These can be made from various materials, including steel, aluminum, or carbon fiber.
Roll Cage Installation
A properly designed roll cage can dramatically increase chassis stiffness and provide additional occupant protection in the event of a rollover. It creates a structural backbone for the car, stiffening the entire body and improving handling.
Types of Roll Cages
Type |
Purpose |
Bolt-In |
Convenient and easy to install, but less rigid than welded cages. |
Welded-In |
Provides maximum rigidity, but requires professional installation and modifies the car’s structure. |
Reinforcing the Suspension
Upgraded suspension components, such as stiffer sway bars, performance shocks, and adjustable coilovers, contribute to improved stability and handling. These components optimize suspension geometry and reduce body roll.
Enhanced Sway Bars
Sway bars, also known as anti-roll bars, resist body roll during cornering. Thicker or adjustable sway bars can significantly reduce body lean and improve cornering ability.
Enhancing Aerodynamics for Increased Stability
Aerodynamic improvements play a crucial role in enhancing the stability of the A90 Supra. By refining the vehicle’s airflow, it is possible to optimize downforce and reduce drag, resulting in improved handling and cornering capabilities.
Here are key aerodynamic enhancements that can further stabilize the A90 Supra:
Front Splitter
A front splitter can be installed beneath the front bumper to deflect incoming air beneath the vehicle. This creates a Venturi effect, which draws air under the car and increases downforce on the front axle. It leads to enhanced grip, steering response, and reduced understeer.
Rear Wing
A rear wing mounted on the trunk lid helps to generate downforce on the rear axle. By creating a high-pressure zone above the wing and a low-pressure zone below, it improves rear grip, reduces oversteer, and enhances cornering stability.
Side Skirts
Side skirts can be installed along the sides of the vehicle to reduce side-to-side airflow and improve the car’s overall aerodynamic efficiency. This reduces drag, enhances lateral stability, and minimizes the risk of body roll during cornering.
Underbody Diffuser
An underbody diffuser can be fitted to the rear of the vehicle to accelerate airflow beneath the car and reduce drag. It further increases downforce on the rear axle, improving traction and stability during high-speed maneuvering.
Canards
Canards, small vertical fins located at the front corners of the car, help to direct airflow around the vehicle. They reduce turbulence and generate vortices which enhance cornering stability and reduce drag.
Gurney Flap
A Gurney flap, a small airfoil-shaped lip attached to the trailing edge of a rear wing or spoiler, can be employed to increase downforce without drastically increasing drag. It helps to maintain stability and improve cornering capabilities.
Aerodynamic Improvement |
Benefits |
Front Splitter |
Increased downforce on front axle, Enhanced grip and steering response |
Rear Wing |
Increased downforce on rear axle, Reduced oversteer and improved cornering stability |
Side Skirts |
Improved aerodynamic efficiency, Reduced drag and enhanced lateral stability |
Underbody Diffuser |
Increased downforce on rear axle, Improved traction and stability during high-speed maneuvering |
Canards |
Reduced turbulence and enhanced cornering stability |
Gurney Flap |
Increased downforce without significantly increasing drag |
Tire Inspection and Maintenance
Regular tire inspections and maintenance are crucial. Check for uneven tread wear, proper tire pressure, and any signs of damage. Correct any issues promptly to ensure optimal road grip and stability.
Wheel Alignment
Misaligned wheels can significantly impact chassis stability. Have a mechanic perform a wheel alignment to ensure that all wheels are properly aligned with each other and with the vehicle’s suspension.
Suspension Component Inspection
Inspect suspension components, such as struts, shocks, and control arms, for wear or damage. Replace any worn or damaged components to restore optimal suspension function and chassis stability.
Brake System Inspection
A properly functioning brake system is essential for controlling the vehicle and maintaining stability. Check brake pads and rotors for wear, and ensure brake lines and calipers are in good condition.
Steering System Inspection
Inspect the steering system, including the steering rack, tie rods, and ball joints, for any signs of wear or play. Loose or damaged components can compromise steering stability.
Chassis Stiffening Modifications
Aftermarket modifications, such as strut bars or sway bars, can increase chassis rigidity and improve handling stability. However, these modifications should be performed by experienced professionals to ensure proper installation.
Weight Distribution Optimization
Uneven weight distribution can affect chassis stability. Adjust weight placement, such as by relocating heavy items to the center of the vehicle, to improve balance and stability.
Traction Control System Optimization
Traction control systems assist in maintaining stability by controlling wheel spin. Have a mechanic optimize the system settings to ensure it operates effectively and does not hinder performance.
Seeking Professional Assistance If Necessary
If you encounter persistent chassis stability issues or lack the necessary expertise or tools to perform repairs, do not hesitate to seek professional assistance from a reputable mechanic or automotive repair shop. They have the specialized knowledge and equipment to accurately diagnose and resolve chassis stability problems.
How to Fix Chassis Stabilization on A90 Supra
The A90 Supra is a high-performance sports car that is known for its handling and stability. However, some owners have reported experiencing issues with chassis stabilization, which can lead to the car feeling unstable or unpredictable at high speeds.
There are a few different things that can cause chassis stabilization issues on the A90 Supra. One common problem is with the car’s suspension. If the suspension is not properly aligned or if the components are worn or damaged, it can cause the car to feel unstable.
Another potential cause of chassis stabilization issues is with the car’s tires. If the tires are not properly inflated or if they are worn or damaged, it can also cause the car to feel unstable. Additionally, if the car is lowered or modified, it can also affect the chassis stabilization.
If you are experiencing chassis stabilization issues with your A90 Supra, there are a few things that you can do to fix the problem. First, you should check the car’s suspension and tires. Make sure that the suspension is properly aligned and that the components are in good condition. You should also check the tires to make sure that they are properly inflated and that they are not worn or damaged.
If you have checked the suspension and tires and you are still experiencing chassis stabilization issues, you may need to take the car to a mechanic. The mechanic will be able to diagnose the problem and recommend the best course of action.
People Also Ask
How do I know if my A90 Supra has chassis stabilization issues?
There are a few signs that may indicate that your A90 Supra has chassis stabilization issues. These signs include:
- The car feels unstable or unpredictable at high speeds.
- The car wanders or drifts on the road.
- The car feels like it is floating or not properly connected to the road.
What are the most common causes of chassis stabilization issues on the A90 Supra?
The most common causes of chassis stabilization issues on the A90 Supra include:
- Improperly aligned suspension
- Worn or damaged suspension components
- Improperly inflated tires
- Worn or damaged tires
- Lowered or modified suspension
How can I fix chassis stabilization issues on the A90 Supra?
There are a few things that you can do to fix chassis stabilization issues on the A90 Supra. These steps include:
- Check the suspension and tires.
- Make sure that the suspension is properly aligned and that the components are in good condition.
- Check the tires to make sure that they are properly inflated and that they are not worn or damaged.
- If you have checked the suspension and tires and you are still experiencing chassis stabilization issues, you may need to take the car to a mechanic.