
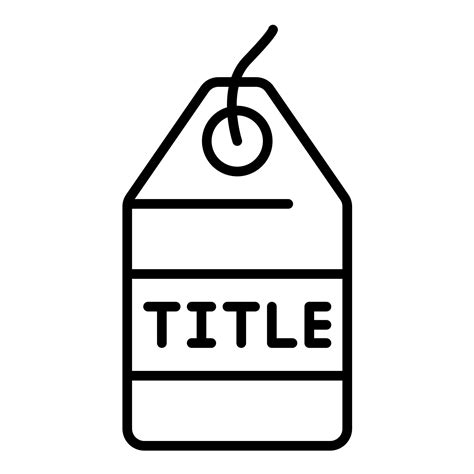
The process of curving aluminum involves shaping the metal into a curved form. This can be done for a variety of reasons, such as creating architectural features, automotive parts, or decorative elements. Curving aluminum can be achieved using a variety of techniques, each with its own advantages and disadvantages. The most common methods include roll bending, press brake forming, and stretch forming. In this article, we will explore the different methods of curving aluminum and discuss their respective advantages and disadvantages.
Roll bending is a process in which the aluminum is passed through a series of rollers that gradually bend the metal into a curved shape. This method is well-suited for large-scale production of curved aluminum components, as it is relatively fast and efficient. However, roll bending can only produce curves with a limited radius of curvature. For tighter curves, other methods such as press brake forming or stretch forming must be used.
Press brake forming is a process in which the aluminum is placed between a die and a punch. The punch is then pressed into the die, bending the aluminum into the desired shape. This method is capable of producing curves with a tighter radius of curvature than roll bending. However, press brake forming is a slower and more labor-intensive process than roll bending. It is also not as well-suited for large-scale production.
Preparation for Aluminum Curving
Curving aluminum requires careful preparation to ensure a successful outcome. The following steps provide a comprehensive guide to prepare for the aluminum curving process:
Materials and Equipment:
Gather the necessary materials and equipment, including aluminum sheet or plate, a bending brake or roll former, safety glasses, gloves, clamps, and measuring tools. Choose the appropriate aluminum alloy based on the desired curvature and thickness.
Aluminum Alloys:
Alloy |
Properties |
1100 |
Excellent formability, low strength |
3003 |
Good formability, moderate strength |
5052 |
High strength, good weldability |
Thickness:
The thickness of the aluminum will determine the minimum bend radius that can be achieved. Thinner aluminum is more flexible and can be curved with a smaller bend radius than thicker aluminum.
Clamping:
Securely clamp the aluminum to the bending brake or roll former to prevent slipping or movement during the curving process. This will ensure accurate and consistent bends.
Measuring:
Use measuring tools to accurately mark the intended bend location and radius. This will help guide the bending process and prevent errors.
Safety Precautions:
Always wear safety glasses and gloves when working with aluminum. Sharp edges and flying debris can pose a hazard. Ensure the bending brake or roll former is properly maintained and operated.
Heat Treatment for Aluminum Curving
Heat treatment plays a crucial role in ensuring the successful curving of aluminum. It involves manipulating the metal’s temperature to alter its mechanical properties and improve its ability to withstand bending without cracking or tearing.
Annealing
The annealing process involves heating the aluminum to a specific temperature, typically between 300°C and 450°C, and then slowly cooling it in a controlled manner. Annealing softens the metal, making it more ductile and pliable, which reduces its resistance to deformation.
Solution Heat Treatment
Solution heat treatment involves heating the aluminum to a higher temperature range of 500°C to 600°C, and then rapidly cooling it in water or air. This process dissolves the alloying elements into the aluminum matrix, creating a homogeneous structure that is stronger and more resistant to cracking during bending.
Heat Treatment Process |
Temperature |
Cooling Rate |
Effect on Aluminum |
Annealing |
300°C – 450°C |
Slow |
Softens and increases ductility |
Solution Heat Treatment |
500°C – 600°C |
Rapid |
Strengthens and increases crack resistance |
Bending Aluminum Using a Brake Press
Materials and Equipment:
- Aluminum sheet or plate
- Brake press
- Die and punch (for specific bend radius)
- Measuring tools (e.g., ruler, tape measure)
- Safety glasses
- Gloves
Steps:
1. Determine Bend Parameters:
Calculate the desired bend angle and bend radius based on the aluminum sheet thickness and desired shape. Determine the appropriate die and punch sizes to achieve the desired results.
2. Setup the Brake Press:
Install the die and punch into the brake press. Adjust the press settings to suit the material thickness and bend parameters. Ensure the machine is properly calibrated and operated according to safety guidelines.
3. Bend the Aluminum:
Position the aluminum sheet or plate between the die and punch. Align the sheet carefully to ensure a precise and consistent bend. Gradually apply pressure to the upper ram of the press to bend the material.
Bend Radius |
Die Radius |
Punch Radius |
0.5 mm |
1.0 mm |
1.5 mm |
1.0 mm |
2.0 mm |
3.0 mm |
2.0 mm |
4.0 mm |
6.0 mm |
4. Inspect the Bend:
Once the bend is complete, visually inspect it for accuracy and quality. Check for any wrinkles, cracks, or other imperfections. If necessary, make adjustments to the press settings or technique and repeat the bending process.
Rolling Aluminum for Curved Shapes
Rolling aluminum is a process of shaping aluminum by passing it through a set of rollers. This process can be used to create curved shapes in aluminum, such as those found in aircraft wings and fuselage panels.
The rolling process begins with a flat sheet of aluminum. The sheet is then passed through a series of rollers that are shaped to create the desired curve. The rollers are typically made of hardened steel and are designed to withstand the high pressures involved in the rolling process.
The rolling process can be performed either cold or hot. Cold rolling is performed at room temperature, while hot rolling is performed at elevated temperatures. Cold rolling produces a harder and stronger aluminum product, while hot rolling produces a more ductile and formable product.
The following are the four main types of rolling processes used to create curved shapes in aluminum:
- Stretch rolling: This process involves stretching the aluminum sheet as it is rolled, which produces a more uniform curvature.
- Roll bending: This process involves bending the aluminum sheet around a cylindrical roller, which produces a tighter curvature.
- Press brake forming: This process involves bending the aluminum sheet between two dies, which produces a sharp bend.
- Curved plate rolling: This process involves rolling the aluminum sheet between two curved dies, which produces a complex curvature.
Rolling Process |
Advantages |
Disadvantages |
Stretch rolling |
Produces a uniform curvature |
Limited to simple curves |
Roll bending |
Produces a tight curvature |
Can cause wrinkles in the aluminum |
Press brake forming |
Produces a sharp bend |
Limited to shallow bends |
Curved plate rolling |
Produces a complex curvature |
Slow and expensive process |
Hand Bending Aluminum for Gentle Curves
Hand bending is a simple and cost-effective method for creating gentle curves in aluminum. With the right tools and techniques, you can easily achieve the desired shape without the need for specialized equipment.
Materials and Tools
To hand bend aluminum, you’ll need:
- Aluminum sheet or strip
- Protective gloves
- Vise or bending brake
- Hammer or mallet
Step-by-Step Instructions
1. Plan the Bend: Determine the desired curve and mark the bend line on the aluminum.
2. Secure the Aluminum: Clamp the aluminum in a vise or place it on a bending brake to hold it firmly.
3. Initiate the Bend: Begin bending the aluminum slightly along the mark using a hammer or mallet. Avoid excessive force.
4. Gradually Increase the Bend: Continue tapping with the hammer, gradually increasing the bend angle as you work your way along the line.
5. Refine the Curve: Once the initial bend has been created, adjust the angle and shape by tapping the aluminum with light, precise blows. Use a block of soft wood or a rubber mallet to protect the surface from damage.
Aluminum Thickness |
Bend Radius |
0.020″ – 0.060″ |
1/4″ – 1″ |
0.060″ – 0.120″ |
3/8″ – 1.5″ |
0.120″ – 0.250″ |
1/2″ – 2″ |
6. Check for Defects: Inspect the bend for any cracks or other defects. If necessary, adjust the bend accordingly.
7. Finish: Remove the aluminum from the clamp and polish the bend to remove any burrs or sharp edges.
Forming Aluminum with Hydraulic Presses
Hydraulic presses are a versatile tool for forming aluminum, offering precise control over the bending process. The press’s hydraulic system generates immense force that can easily deform aluminum without cracking or tearing. Here are the key steps involved:
1. Preparation
Start by selecting the appropriate die for the desired bend radius. Ensure that the aluminum sheet is clean and free of any debris or corrosion.
2. Positioning
Place the aluminum sheet between the die and the punch. Align the sheet carefully to achieve the desired bend location.
3. Clamping
Secure the aluminum sheet firmly in place using the press’s clamping system. This prevents slippage and ensures an accurate bend.
4. Bending
Activate the hydraulic system to apply force to the punch. Monitor the bending process closely and adjust the pressure as needed to achieve the desired bend angle.
5. Unclamping
Once the bending is complete, release the clamping system and remove the formed aluminum sheet.
6. Heat Treatment
In some cases, heat treatment may be necessary to enhance the bend’s strength and durability. This involves heating the bent area to a specific temperature and then cooling it gradually. Heat treatment options include:
Method |
Temperature |
Cooling Rate |
Annealing |
Between 350-450°C |
Slow |
Stress Relieving |
Between 200-300°C |
Medium |
Quenching |
Above 450°C |
Rapid |
The appropriate heat treatment method and parameters depend on the specific aluminum alloy and thickness being formed.
Using Molds for Aluminum Curving
One of the most effective methods for curving aluminum is by utilizing molds. This technique involves shaping the aluminum sheet into the desired curvature using a mold or form. The mold is typically made of a rigid material such as wood, metal, or composite, providing the desired shape and support for the aluminum sheet as it is bent.
To achieve precise curves, it is recommended to use molds specifically designed for the intended shape. The aluminum sheet is placed over the mold and secured in place. External pressure is then applied to the aluminum sheet, gradually forcing it to conform to the shape of the mold. Spring clamps or straps can be used to maintain the shape and prevent the aluminum from springing back.
The amount of pressure required depends on the thickness and temper of the aluminum sheet. Thinner and softer aluminum will require less pressure, while thicker and harder aluminum may require more force. It is important to apply pressure gradually and evenly to avoid overstressing or damaging the aluminum sheet.
Once the desired curvature is achieved, the aluminum sheet is removed from the mold. Spring-back may occur when the sheet is released from the mold, so it is important to take into account this spring-back when determining the initial curvature.
The table below provides a summary of the steps involved in curving aluminum using molds:
Step |
Description |
1 |
Select or create a mold that matches the desired curvature. |
2 |
Secure the aluminum sheet over the mold. |
3 |
Apply external pressure gradually and evenly to the aluminum sheet. |
4 |
Maintain the pressure until the desired curvature is achieved. |
5 |
Remove the aluminum sheet from the mold. |
Annealing Aluminum After Curving
Annealing is a heat treatment process that restores the ductility and malleability of cold-worked aluminum, making it easier to bend or curve. It involves heating the metal to a specific temperature and then cooling it slowly.
Heating the Aluminum
The recommended temperature for annealing aluminum ranges from 650°F (343°C) to 800°F (427°C). Use an oven, heat gun, or induction heater to heat the metal evenly.
Holding the Temperature
Hold the metal at the annealing temperature for 30-60 minutes per inch of thickness. For example, a 1/4-inch-thick piece would need to be held at temperature for 7.5-15 minutes.
Cooling Slowly
After heating, allow the metal to cool slowly in a still-air environment. Do not quench it in water or air-cool it. Slow cooling prevents the formation of internal stresses that can lead to cracking or warping.
Annealing Parameters for Different Aluminum Alloys
Different aluminum alloys have slightly different annealing requirements. The following table provides guidelines for some common alloys:
Alloy |
Annealing Temperature (°F) |
Holding Time (minutes/inch of thickness) |
1100 |
700-800 |
30-60 |
3003 |
650-750 |
30-60 |
5052 |
700-800 |
30-60 |
6061 |
750-850 |
30-60 |
7075 |
800-900 |
30-60 |
Finishing and Polishing Curved Aluminum
Once the aluminum has been curved, it’s important to finish and polish it properly to achieve the desired look and protect the metal. Here’s how to do it:
1. Sanding
Start by sanding the curved aluminum with a fine-grit sandpaper (220-grit or higher). Sand in the direction of the curve to avoid creating scratches. Use a sanding block or a piece of foam to distribute pressure evenly.
2. Buffing
After sanding, buff the aluminum with a buffing wheel or a buffing compound on a cloth. This will remove any remaining scratches and bring out the shine.
3. Polishing
To achieve a mirror-like finish, polish the aluminum with a polishing compound and a soft cloth. Use gentle, circular motions and apply moderate pressure.
4. Sealing
To protect the finished surface from corrosion and wear, apply a clear sealant. This can be a lacquer, a clear coat, or a polyurethane.
5. Cleaning
To maintain the shine of the curved aluminum, clean it regularly with a mild detergent and warm water. Avoid using abrasive cleaners or harsh chemicals.
6. Maintenance
Over time, the curved aluminum may need to be refinished or polished to maintain its appearance. The frequency of maintenance will depend on the environment in which the aluminum is used.
7. Troubleshooting
If you encounter any problems while finishing or polishing curved aluminum, here are some troubleshooting tips:
- Scratches: If you notice scratches, sand the area again with a finer grit sandpaper.
- Dull finish: If the aluminum is not shiny enough, buff or polish it with a more abrasive compound.
- Corrosion: If the aluminum is corroding, clean it thoroughly and apply a protective sealant.
8. Safety Precautions
Always wear safety glasses and gloves when working with curved aluminum. Use a dust mask to prevent inhaling sanding dust. Keep the work area well-ventilated.
9. Considerations for Different Aluminum Alloys
Different aluminum alloys have different properties, which may affect the finishing and polishing process. Here are some considerations for common aluminum alloys:
Alloy |
Characteristics |
Finishing Tips |
1050 |
Pure aluminum |
Soft and ductile, easy to finish |
3003 |
Manganese alloy |
Stronger than 1050, more resistant to corrosion |
Use a fine-grit sandpaper for sanding |
5052 |
Magnesium alloy |
High strength and corrosion resistance |
May require more aggressive sanding and polishing |
Applications of Curved Aluminum
1. Architectural Facades
Curved aluminum panels enhance the aesthetics of buildings by creating unique and visually appealing exteriors. Their versatility allows for intricate designs and seamless integration with other building materials.
2. Roofing Systems
Curved aluminum roofing systems provide superior protection against weather elements and offer design flexibility. They can be curved into various shapes to match the curvature of the roof, resulting in a sleek and durable finish.
3. Cladding
Curved aluminum cladding panels are used to cover exterior walls of buildings. They are lightweight, durable, and can be customized to meet specific design requirements, adding both aesthetic appeal and weather resistance to structures.
4. Interior Design
Curved aluminum is employed in interior design to create unique features such as curved walls, ceilings, and decorative elements. Its malleability and flexibility make it suitable for shaping into complex forms, adding sophistication and visual interest to interior spaces.
5. Automotive Industry
In the automotive sector, curved aluminum is utilized for various applications, including body panels, hoods, and grills. It offers lightweight, strength, and durability, enhancing vehicle performance and aesthetics.
6. Aerospace
Within the aerospace industry, curved aluminum is used in aircraft fuselages, wings, and control surfaces. Its strength-to-weight ratio makes it ideal for these critical components, providing structural integrity while reducing overall weight.
7. Furniture
Curved aluminum is incorporated into furniture designs to create stylish and functional pieces. It can be formed into chairs, tables, and other furniture elements with unique shapes and textures, adding a contemporary touch to interior decor.
8. Medical Equipment
In the medical field, curved aluminum is employed in the production of medical devices, such as surgical instruments, implants, and diagnostic tools. Its biocompatibility and formability allow for precise and intricate designs that enhance patient care and outcomes.
9. Consumer Electronics
Curved aluminum is used in consumer electronics, including smartphone cases, tablet covers, and other device accessories. Its lightweight and durable properties provide protection and aesthetic appeal, enhancing user experience.
10. Signage and Displays
Curved aluminum panels are employed in signage and display applications. Their ability to conform to curved surfaces makes them ideal for creating eye-catching and memorable graphics, effectively attracting attention and conveying information.
Sign Type |
Benefits of Curved Aluminum |
Wayfinding Signage |
Guides visitors easily through complex environments |
Retail Signage |
Enhances product visibility and brand recognition |
Advertising Displays |
Creates visually impactful and immersive experiences |
Architectural Signage |
Adds a touch of elegance and distinctiveness to buildings |
How to Curve Aluminum
Curving aluminum is a relatively simple process that can be done with a variety of tools and techniques. The most common method is to use a brake, which is a machine that bends metal by applying pressure to it. Brakes come in a variety of sizes and shapes, and the type of brake you need will depend on the size and thickness of the aluminum you are bending.
If you do not have access to a brake, you can also curve aluminum by hand using a hammer and a block of wood. To do this, place the aluminum on the block of wood and use the hammer to gently tap it into the desired curve. Be careful not to hit the aluminum too hard, as this can damage it.
Once you have curved the aluminum, you can finish it by sanding the edges smooth and applying a clear coat to protect it from corrosion.
People Also Ask
How do you bend aluminum without a brake?
You can bend aluminum without a brake by using a hammer and a block of wood. To do this, place the aluminum on the block of wood and use the hammer to gently tap it into the desired curve. Be careful not to hit the aluminum too hard, as this can damage it.
What is the easiest way to curve aluminum?
The easiest way to curve aluminum is to use a brake. Brakes come in a variety of sizes and shapes, and the type of brake you need will depend on the size and thickness of the aluminum you are bending.
How do you make a sharp curve in aluminum?
To make a sharp curve in aluminum, you will need to use a brake with a sharp radius. The radius of the brake will determine how sharp the curve in the aluminum will be.