
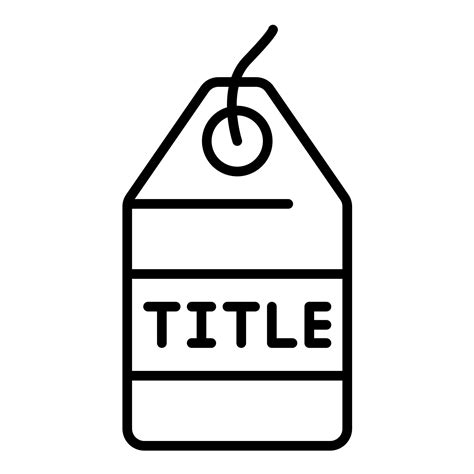
Are you tired of staring at your car’s dull and lifeless paint? Do you wish you could restore its former glory without spending a fortune? If so, then it’s time to learn how to buff your car with a buffer. Buffing, also known as polishing, involves removing a thin layer of paint from the surface of your car to eliminate imperfections and restore its shine. While it may seem like a daunting task, buffing is actually quite easy to do with the right tools and guidance. Keep on reading to learn the step-by-step process on how to buff your car like a pro.
Before you start buffing, it’s important to gather the necessary supplies. You will need a buffer, polishing pads, polishing compound, wax, and a microfiber cloth. Once you have all of your supplies, you can begin by washing and drying your car thoroughly. This will remove any dirt or debris that could scratch the paint during the buffing process. Next, apply a small amount of polishing compound to a polishing pad and attach it to the buffer. Start buffing the car in small sections, using a back-and-forth motion. Be sure to apply even pressure and avoid staying in one spot for too long.
As you buff the car, you will start to see the paint becoming smoother and shinier. Continue buffing until the entire car has been polished. Once you have finished buffing, wipe down the car with a microfiber cloth to remove any excess polishing compound. Finally, apply a coat of wax to the car to protect the paint and enhance its shine. Buffing your car is a great way to restore its beauty and protect it from the elements. By following these simple steps, you can buff your car like a pro and keep it looking its best for years to come.
Understanding the Basics of Buffing
What is Buffing?
Buffing is a multifaceted process that involves restoring a car’s paint to its former glory. It entails eliminating imperfections like scratches, swirls, and oxidation, resulting in a gleaming, mirror-like finish. Professional detailers commonly employ buffing techniques to transform dull, neglected vehicles into pristine masterpieces.
Essential Tools
The cornerstone of buffing lies in selecting the appropriate tools. A variable-speed buffer or polisher serves as the primary device, providing the necessary power and control. Buffing pads, typically made of foam or wool, are attached to the buffer’s backing plate. These pads come in varying degrees of abrasiveness, ranging from coarse to fine, to accommodate different paint conditions.
Types of Buffing Pads
Type |
Abrasiveness |
Usage |
Coarse |
Highly abrasive |
Removing deep scratches and defects |
Medium |
Moderately abrasive |
Smoothing out minor scratches and swirls |
Fine |
Lightly abrasive |
Polishing and refining the paint surface |
Safety Precautions
Prior to engaging in buffing, safety precautions must be observed. Wearing protective gear such as gloves and eye protection is essential. Proper ventilation is crucial to prevent inhaling harmful dust particles generated during the process. Furthermore, it is advisable to test the buffing technique on an inconspicuous area of the car to gauge its compatibility with the paint type before proceeding with the entire surface.
Selecting the Right Buffer and Compound
Choosing the Right Buffer
The type of buffer you choose will depend on the size of the area you’re working on and the condition of the paint. For small areas or delicate finishes, a smaller, handheld buffer is a good option. For larger areas or heavily oxidized paint, a larger, orbital buffer will provide more power and efficiency.
When selecting a buffer, consider the following factors:
* Size: Handheld buffers are typically smaller and more maneuverable than orbital buffers.
* Power: Orbital buffers generally have more power than handheld buffers, making them more effective for removing heavy oxidation and scratches.
* Speed: Buffers typically have variable speed settings, allowing you to adjust the speed to suit the task.
* Accessories: Some buffers come with additional accessories, such as backing plates and bonnets.
Choosing the Right Compound
The type of compound you use will depend on the severity of the damage to the paint. For minor scratches or oxidation, a mild compound will suffice. For heavier damage, a more aggressive compound will be necessary.
Here’s a table summarizing the different types of compounds available:
| Compound Type | Description |
|—|—|
| Mild | Removes light scratches and oxidation |
| Medium | Removes moderate scratches and oxidation |
| Heavy | Removes heavy scratches and oxidation |
| Ultra-heavy | Removes deep scratches and severe oxidation |
When choosing a compound, it’s important to consider the following factors:
* Abrasiveness: The abrasiveness of the compound determines how much material it will remove from the paint.
* Cut: The cut of the compound refers to its ability to remove imperfections.
* Finish: The finish of the compound determines the level of gloss and smoothness it will leave on the paint.
Preparing the Car’s Surface
Before you start buffing your car, it’s important to prepare the surface properly. This will help ensure that you get the best possible results.
1. Wash and Dry the Car
Start by washing the car thoroughly to remove any dirt or debris. Use a mild car wash soap and a soft sponge or wash mitt. Avoid using harsh detergents or abrasive brushes, as these can damage the paint.
2. Clay the Car
Claying the car is a process that removes embedded contaminants from the paint surface. These contaminants can include brake dust, tree sap, and tar. To clay the car, use a clay bar and a clay lubricant. Gently rub the clay bar over the paint surface, applying light pressure. The contaminants will stick to the clay bar, leaving the paint surface smooth and clean.
3. Protect the Trim
Before you start buffing, it’s important to protect the trim around the car. This includes the rubber seals around the windows and doors, the plastic bumpers, and the chrome accents. You can protect the trim by applying masking tape or by using a protective spray.
| Trim Type | Protection Method |
|—|—|
| Rubber Seals | Masking Tape |
| Plastic Bumpers | Protective Spray |
| Chrome Accents | Masking Tape or Protective Spray |
Applying Polish and Buffing Techniques
Applying Polish
Before applying polish, ensure the car surface is clean and free of contaminants. Apply the polish evenly using a circular or overlapping motion. Use a moderate amount of polish and avoid excess. Apply additional polish to any areas requiring more attention.
Buffing Techniques
Polisher Selection
Choose an appropriate polisher for the desired results. Orbital polishers are ideal for beginners and small corrections, while rotary polishers offer more power for deep scratches or severe imperfections.
Buffing Speed
Adjust the polisher speed based on the severity of corrections needed. Start with a lower speed for initial polishing and gradually increase as necessary. Avoid excessive high speeds, as it can damage the paint.
Buffing Pressure
Apply light to medium pressure on the polisher while buffing. Overapplying pressure can cause micro-marring or paint damage. Use a firm but gentle stroke to effectively remove imperfections without damaging the finish.
Buffing Time
Buff until the desired results are achieved. It may take multiple passes to remove all imperfections. Allow sufficient time for each pass to ensure thorough removal of scratches and swirls. Monitor the results frequently and stop buffing when the desired finish is obtained.
Buffing Tips |
Use a clean microfiber cloth to wipe away polish residue. |
Avoid buffing in direct sunlight or on a hot surface. |
Wash the car thoroughly after buffing to remove any remaining polish. |
Use a finishing polish to enhance the shine and protect the paint. |
Removing Swirls and Holograms
Swirls and holograms are common imperfections caused by improper washing or polishing techniques. To remove these defects, follow these steps:
1. Prepare the Car
Thoroughly wash and dry the car to remove any dirt or debris that could interfere with the buffing process.
2. Choose the Right Pad and Compound
Select a soft polishing pad and a gentle compound designed for removing minor imperfections. Avoid harsh pads or compounds, as these can cause further damage.
3. Apply the Compound
Apply a small amount of compound to the polishing pad and spread it evenly over a small area (about 1 square foot).
4. Buff the Surface
Use a dual-action polisher and apply light to medium pressure while buffing in a circular motion. Start with low speed and gradually increase as needed.
5. Refine the Buffing Process
Once the swirls and holograms are mostly removed, repeat the buffing process with a softer pad and a finer compound. This will further refine the surface and restore its pristine shine. Use the following table as a guide for selecting the appropriate pad and compound:
Pad type |
Compound type |
Blue or white pad |
Heavy cutting compound |
Orange or yellow pad |
Medium cutting compound |
Black or green pad |
Fine finishing compound |
Restoring Paint to a Mirror-Like Finish
Buffing a car is a process of restoring the paint to its original shine and luster. This can be done by hand or with a machine buffer. If you are using a machine buffer, it is important to use the correct technique to avoid damaging the paint.
Materials
You will need the following materials to buff your car:
- Car wash soap
- Bucket
- Wash mitt or sponge
- Clay bar
- Clay bar lubricant
- Compound
- Polishing pad
- Wax
- Wax applicator pad
- Machine buffer (optional)
Preparing the Car
Before you begin buffing, you need to prepare the car. This involves washing the car to remove any dirt or debris, and then claying the car to remove any contaminants that may be embedded in the paint.
Buffing the Car
Once the car is prepared, you can begin buffing. If you are using a machine buffer, it is important to use the correct technique to avoid damaging the paint.
To buff the car by hand, apply a small amount of compound to a polishing pad. Then, use a circular motion to rub the compound into the paint. Apply light pressure and avoid rubbing too hard.
To buff the car with a machine buffer, attach a polishing pad to the buffer. Then, apply a small amount of compound to the pad. Start by buffing at a low speed and gradually increase the speed. Use a light touch and avoid applying too much pressure.
Polishing the Car
Once the car has been buffed, you can polish it. This will help to remove any swirls or scratches that may have been created during the buffing process.
To polish the car, apply a small amount of polish to a polishing pad. Then, use a circular motion to rub the polish into the paint. Apply light pressure and avoid rubbing too hard.
Waxing the Car
Once the car has been polished, you can wax it. This will help to protect the paint from the elements and give it a glossy shine.
To wax the car, apply a small amount of wax to a wax applicator pad. Then, use a circular motion to rub the wax into the paint. Apply light pressure and avoid rubbing too hard.
Tips for Buffing a Car
Here are a few tips for buffing a car:
Tip |
Description |
Use a soft, clean polishing pad. |
A hard or dirty polishing pad can scratch the paint. |
Apply light pressure. |
Rubbing too hard can damage the paint. |
Work in small sections. |
Buffing too large an area at once can make it difficult to control the buffer. |
Keep the buffer moving. |
Stopping the buffer in one spot can burn the paint. |
Inspect the paint often. |
This will help you to avoid damaging the paint. |
Common Buffing Mistakes and How to Avoid Them
1. Using too much pressure
Applying excessive pressure while buffing can damage the paint and create swirls. Use a light touch and let the buffer do the work.
2. Buffing in one direction
Buffing repeatedly in the same direction can create streaks and unevenness. Move the buffer in a random, overlapping motion to avoid these issues.
3. Neglecting to clean the buffer pad
Accumulated polishing residue on the buffer pad can transfer to the paint, resulting in imperfections. Regularly clean the pad with a detailing spray.
4. Using the wrong polish for the job
Different types of polishes are formulated for specific purposes. Select a polish that is appropriate for the condition of the paint and the desired results.
5. Applying polish directly to the paint
Always apply polish to the buffer pad rather than the paint. This helps distribute the polish evenly and prevents over-application.
6. Buffing too long
Over-buffing can generate heat, which can damage the paint. Buff for the time recommended by the polish manufacturer.
7. Buffing in direct sunlight
Buffing in direct sunlight can accelerate polishing residue’s drying, making it difficult to remove and potentially causing staining. Buff in a shaded area or out of direct sunlight.
Mistake |
Cause |
Consequence |
Solution |
Applying too much pressure |
Overloading the buffer |
Paint damage, swirls |
Use a light touch |
Buffing in one direction |
Creating streaks, unevenness |
Polishing in a random, overlapping motion |
|
Neglecting to clean the buffer pad |
Transferring polishing residue |
Imperfections |
Regularly clean the pad |
Using the wrong polish |
Ineffective polishing |
Poor results |
Choose a polish specific to the paint condition |
Applying polish directly to the paint |
Uneven distribution, over-application |
Buffing only the pad |
|
Buffing too long |
Heat generation, paint damage |
Over-buffing |
Buff for the recommended time |
Buffing in direct sunlight |
Accelerated drying, staining |
Buff in a shaded area |
|
Maintenance Tips for a Lasting Shine
1. Wash Regularly
The first step to keeping your car looking its best is to wash it regularly. Use a mild car wash soap and a soft cloth or sponge. Avoid using harsh cleaners or abrasive cloths, as these can damage the paint.
2. Dry Thoroughly
After washing your car, dry it thoroughly with a clean cloth or chamois. This will help to prevent water spots from forming.
3. Wax Regularly
Waxing your car helps to protect the paint from the elements. It also makes your car easier to wash and dry. Apply a coat of wax every few months, or more often if your car is exposed to a lot of sun or rain.
4. Avoid Touchless Car Washes
Touchless car washes use harsh chemicals and high-pressure water to clean your car. This can damage the paint over time. It is better to wash your car by hand or at a touchless car wash that uses gentle cleaners and low-pressure water.
5. Park in the Shade
The sun’s ultraviolet rays can damage your car’s paint. If possible, park in the shade to protect your car from the sun.
6. Use a Car Cover
A car cover can help to protect your car from the elements. Use a car cover when your car is parked for long periods of time, or when it is exposed to a lot of sun or rain.
7. Buff Occasionally
Buffing your car with a buffer can help to remove minor scratches and imperfections in the paint. Buffing can also help to restore the shine to your car’s paint. It is important to buff your car correctly to avoid damaging the paint. If you are not sure how to buff your car, it is best to take it to a professional.
Buffing Your Car with a Buffer
To buff your car with a buffer, you will need:
– A car buffer
– A polishing pad
– A polishing compound
– A clean cloth or chamois
Steps |
Details |
1. Wash and dry your car. |
This will help to remove any dirt or debris that could scratch the paint. |
2. Apply a small amount of polishing compound to the polishing pad. |
Do not apply too much compound, as this can make it difficult to buff the car. |
3. Attach the polishing pad to the buffer. |
Make sure that the pad is securely attached. |
4. Start buffing the car. |
Start by buffing a small area of the car. Use a slow, circular motion. |
5. Gradually increase the speed of the buffer. |
Once you have started buffing, gradually increase the speed of the buffer. |
6. Buff the entire car. |
Once you have buffed one area of the car, move on to the next area. Continue buffing until you have buffed the entire car. |
7. Wipe down the car with a clean cloth or chamois. |
This will help to remove any excess polishing compound. |
8. Enjoy your newly buffed car! |
Your car should now have a beautiful shine. |
9. If you are not sure how to buff your car, it is best to take it to a professional.
Advanced Buffing Techniques for Detailers
9. Compounding and Polishing by Hand
While machine buffing is the preferred method for serious detailing, there are some situations where hand compounding and polishing may be necessary. For example, if the paint surface is badly swirled or scratched, hand polishing can provide the necessary control and precision to remove these defects without causing further damage. Additionally, hand polishing can be used to access areas that are difficult to reach with a machine, such as tight curves or recesses. For the best results,
when buffing by hand, use a high-quality polishing compound and a soft, microfiber cloth. Apply a small amount of compound to the cloth and gently rub it into the paint surface in a circular motion. Use light pressure and avoid rubbing too hard, as this can actually cause more damage to the paint. Once you have applied the compound, use a clean microfiber cloth to remove any excess and buff the surface to a high shine.
Here is a table summarizing the key differences between machine buffing and hand buffing:
|
Machine Buffing |
Hand Buffing |
Speed |
Much faster than hand buffing |
Slower than machine buffing |
Control |
Less control than hand buffing |
Greater control than machine buffing |
Precision |
Less precise than hand buffing |
More precise than machine buffing |
Effort |
Less effort than hand buffing |
More effort than machine buffing |
Buffing with Rotary vs. Orbital Buffers
There are two main types of buffers used for car detailing: rotary buffers and orbital buffers. Rotary buffers are more powerful and can remove deeper scratches, but they also require more skill to use. Orbital buffers are less powerful but are easier to use and are less likely to damage the paint if used improperly.
Here is a table comparing the two types of buffers:
|
Rotary Buffers |
Orbital Buffers |
Power |
More powerful |
Less powerful |
Speed |
Rotate at a high speed |
Oscillate at a lower speed |
Skill required |
More skill required |
Less skill required |
Damage potential |
Higher potential to damage paint |
Lower potential to damage paint |
Cost |
Typically more expensive |
Typically less expensive |
Ultimately, the best type of buffer for you depends on your experience level and the condition of your car’s paint. If you are new to car detailing, it is best to start with an orbital buffer. Once you gain more experience, you may want to upgrade to a rotary buffer for more aggressive polishing.
How to Buff a Car with a Buffer
Buffing a car is a great way to restore its shine and protect it from the elements. It can be done by hand or with a buffer, and while hand buffing is more labor-intensive, it can be just as effective as using a buffer. If you’re new to buffing, it’s best to start with a small, inconspicuous area of your car to practice on.
To buff a car with a buffer, you will need the following supplies:
- A buffer with a soft bonnet
- Polishing compound
- Wax
- A clean microfiber cloth
Once you have gathered your supplies, follow these steps to buff your car:
- Wash and dry your car thoroughly.
- Apply a small amount of polishing compound to the bonnet of the buffer.
- Turn on the buffer and start buffing the car in small, circular motions.
- Continue buffing until the polishing compound has been evenly distributed across the surface of the car.
- Wipe off the polishing compound with a clean microfiber cloth.
- Apply a coat of wax to the car and allow it to dry.
- Buff off the wax with a clean microfiber cloth.
Buffing your car regularly will help to keep it looking its best and protect it from the elements. It’s a relatively easy and inexpensive process that can make a big difference in the appearance of your car.
People Also Ask
What is the difference between polishing and buffing?
Polishing and buffing are two separate processes that are often used together to restore the shine to a car’s paint. Polishing removes scratches and other imperfections in the paint, while buffing brings out the shine. Polishing is typically done with a polishing compound and a buffer, while buffing is done with a wax or sealant and a buffer.
Can I buff my car by hand?
Yes, you can buff your car by hand. However, it is more labor-intensive than using a buffer. To buff your car by hand, you will need a polishing compound and a clean microfiber cloth. Apply a small amount of polishing compound to the cloth and rub it in circular motions over the surface of the car. Continue rubbing until the polishing compound has been evenly distributed. Wipe off the polishing compound with a clean microfiber cloth and apply a coat of wax or sealant to the car.
How often should I buff my car?
The frequency with which you should buff your car depends on several factors, including the type of paint on your car, the climate you live in, and how often you wash your car. As a general rule of thumb, it is recommended to buff your car every 3-6 months.