
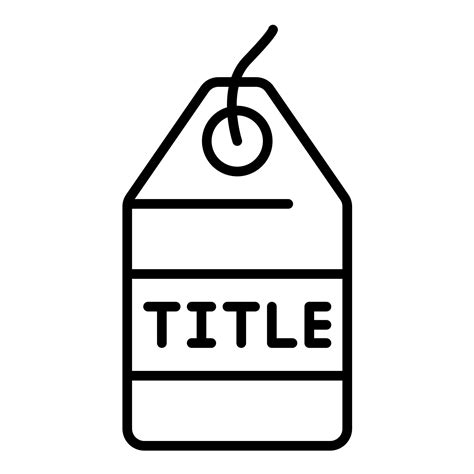
Tired of your car causing you endless headaches and frustration? Struggling to find a reliable and trustworthy repair shop that won’t break the bank? Look no further! Our comprehensive guide unveils the top-rated auto repair shops near you, ensuring your vehicle receives the expert care it deserves.
From minor maintenance to major overhauls, our handpicked selection of repair shops boasts a team of highly skilled and experienced technicians who utilize state-of-the-art equipment and genuine parts to restore your vehicle to its peak performance. Rest assured that your car is in safe hands, as these shops prioritize transparency and clear communication, keeping you informed every step of the way. Additionally, their commitment to customer satisfaction extends beyond repairs, offering convenient amenities such as complimentary shuttle services and comfortable waiting areas to make your experience as hassle-free as possible. Transitioning seamlessly to the next paragraph, we will delve into the specific criteria and factors that set these repair shops apart from the rest.
Furthermore, these repair shops are renowned for their exceptional customer service, going above and beyond to ensure your utmost satisfaction. Not only do they provide detailed explanations of the repairs, but they also offer personalized recommendations and advice to help you make informed decisions about your vehicle’s maintenance. Transitioning smoothly to the concluding paragraph, we will provide you with valuable tips and insights to consider when selecting the best repair shop for your specific needs.
Finding the Ideal Repair Shop: A Guide to Excellence
Factors to Consider When Selecting a Repair Shop
When your vehicle requires repairs, choosing the right repair shop is crucial for ensuring quality workmanship, fair pricing, and peace of mind. Consider the following factors to identify the ideal shop for your automotive needs:
- Experience and Expertise: Look for shops with a proven track record in your specific vehicle make and model. Technicians should possess ASE or OEM certifications to demonstrate their knowledge and skills.
- Warranty and Guarantee: A reputable shop will offer a warranty or guarantee on their work, providing you with assurance that the repairs will last. Check the terms and conditions of the warranty to ensure it covers both parts and labor.
- Reputation and Reviews: Read online reviews and consult trusted sources for insights into the shop’s customer service, reliability, and overall reputation. Positive feedback from previous customers is a valuable indicator of a shop’s commitment to excellence.
- Transparency and Communication: Choose shops that provide clear estimates, explain repairs in detail, and keep you informed throughout the process. Open and transparent communication fosters trust and ensures you understand the work being done on your vehicle.
- Convenience and Accessibility: Consider the location and hours of operation when selecting a repair shop. Accessibility is essential for scheduling appointments and picking up your vehicle when repairs are complete.
Factor |
Considerations |
Experience and Expertise |
ASE or OEM certifications, specialized knowledge in your vehicle make/model |
Warranty and Guarantee |
Covers parts and labor, provides peace of mind |
Reputation and Reviews |
Positive customer feedback, trusted sources |
Transparency and Communication |
Clear estimates, detailed explanations, frequent updates |
Convenience and Accessibility |
Location, business hours, ease of scheduling |
Evaluating Repair Services: Key Considerations
1. Reputation and History
Consider the shop’s online reviews, customer testimonials, and Better Business Bureau (BBB) rating. Seek out shops with positive feedback and a proven track record of providing quality repairs.
2. Experience and Expertise
Verify the shop’s technicians are certified, experienced, and knowledgeable in your specific repair needs. Look for shops that specialize in specific make and models to ensure they have the necessary tools and expertise to diagnose and fix your issue accurately.
Experience Level |
Qualifications |
Entry-Level |
Less than 2 years of experience, apprentice-level, basic certifications |
Intermediate |
2-5 years of experience, industry-recognized certifications, specialization in certain repair types |
Advanced |
5+ years of experience, master-level certifications, specialized training, diagnostic expertise |
3. Communication and Transparency
Effective communication is crucial. Choose shops that provide clear explanations of the issue, repair process, and estimated timeframes. They should also keep you updated throughout the repair and seek your approval before proceeding with any significant repairs.
Expertise and Reliability: The Hallmarks of Dependable Repair
Reliability is a combination of competence, consistency, expertise, responsibility, and honesty. A reliable shop can be trusted to deliver quality work, stand behind its repairs, and treat their customers fairly. Expertise is the knowledge, experience, and skill required to perform a specific task or job. A shop with expertise in a particular area will have the necessary training, tools, and experience to handle even the most complex repairs. A dependable shop should have a team of skilled technicians who will provide excellent service.
Technician Expertise
One of the most important things to look for in a repair shop is the expertise of its technicians. Ask about the training and experience of the technicians who will be working on your vehicle. Certified technicians have undergone rigorous training and testing to ensure that they have the skills and knowledge to work on your car. Experience is also important, so look for shops that have been in business for a while and have a track record of success.
Technician Certification |
Organization |
ASE Certified Master Technician |
National Institute for Automotive Service Excellence (ASE) |
GM Certified Service Technician |
General Motors (GM) |
Ford Certified Master Technician |
Ford Motor Company |
In addition to training and experience, it’s important to look for technicians who are passionate about their work. Technicians who love what they do are more likely to take pride in their work and provide excellent customer service.
Transparency and Communication: Building Trust with Customers
Trust and Transparency
Transparency is paramount in fostering trust with customers. Customers want to know what’s happening with their vehicle, why it needs repairs, and how much it will cost. Repair shops that provide detailed explanations, engage in open discussions, and keep customers updated on progress build a strong foundation of trust.
Clear and Effective Communication
Effective communication is crucial for ensuring customers understand their vehicle’s issues and the proposed repairs. Repair shops should use clear and concise language, avoiding jargon or technical terms that may confuse customers. They should also provide written estimates and explain any additional costs or services that may be required.
Personalized Communication Channels
Customers value personalized communication channels that cater to their preferences. Repair shops can offer multiple communication options, such as phone calls, text messages, or email updates. They should also make themselves available for inquiries or concerns at convenient times.
Customer Relationship Management (CRM) Systems
CRM systems can help repair shops track customer interactions, preferences, and repair history. By leveraging this data, businesses can tailor communication strategies, provide personalized recommendations, and foster long-term relationships with customers.
Communication Channel |
Benefits |
Phone Calls |
- Real-time communication
- Allows for nuanced conversations
|
Text Messages |
- Convenient and quick updates
- Can provide reminders or appointment confirmations
|
Email |
- Detailed explanations and written documentation
- Can include images or attachments
|
Convenience and Efficiency: Streamlining the Repair Process
1. Appointment Scheduling and Online Diagnostics
Top repair shops offer convenient appointment scheduling options, allowing you to book online or over the phone at your leisure. Advanced shops also provide online diagnostics, enabling you to submit vehicle symptoms and receive preliminary estimates without even leaving your home.
2. Efficient Repair Process and Timely Updates
Skilled technicians prioritize swift and efficient repairs, minimizing vehicle downtime. They keep you informed throughout the process with regular status updates, ensuring transparency and peace of mind.
3. Courtesy Transportation and Concierge Services
Exceptional repair shops offer courtesy transportation options to and from the shop or access to nearby public transportation. Some even provide concierge services, arranging for vehicle rentals or appointments with other local businesses while your car is being serviced.
4. Convenient Payment Options and After-Repair Support
Renowned repair shops accept various payment methods, including credit, debit, and online transfers. They also provide comprehensive after-repair support, including warranties and complimentary follow-up inspections, ensuring long-term satisfaction.
5. Digital Vehicle Inspections and Detailed Repair Reports
Advanced repair shops utilize digital vehicle inspections and provide detailed repair reports. These reports include high-quality images, videos, and comprehensive explanations of the work performed. This transparency allows you to fully understand the repairs and make informed decisions regarding your vehicle’s maintenance.
Service |
Convenience Feature |
Appointment Scheduling |
Online booking and preliminary diagnostics |
Repair Process |
Swift and efficient repairs, regular status updates |
Transportation |
Courtesy rides or access to public transportation |
Payment |
Multiple payment options, warranties, follow-up inspections |
Repair Reports |
Digital vehicle inspections, detailed repair explanations |
State-of-the-Art Equipment and Techniques: Ensuring Precision Repairs
Our repair professionals utilize state-of-the-art equipment and techniques to ensure precise, reliable repairs. This advanced technology enables us to diagnose and fix issues with unmatched accuracy and efficiency.
Expert Technicians and Skillful Craftsmanship
Our team of highly trained and experienced technicians possesses the expertise and craftsmanship to repair various devices. They undergo continuous training to stay abreast of the latest technological advancements, ensuring your repairs are handled by skilled professionals.
Genuine and Quality Parts
We exclusively use genuine and high-quality parts in our repairs. This ensures the highest level of performance and durability for your repaired device. By sourcing parts directly from authorized suppliers, we guarantee their authenticity and compatibility.
Comprehensive Diagnostics and Testing
Before any repairs, our technicians perform thorough diagnostics to identify the root cause of the issue. This comprehensive analysis ensures that we address the exact problem and prevent recurrence in the future. Additionally, we conduct thorough testing after repairs to verify the device’s full functionality.
Rapid Turnaround Times
We understand the importance of time, especially when your device is out of commission. Our efficient repair process and dedicated team ensure quick turnaround times. We strive to minimize downtime and get your device back into your hands as soon as possible.
Competitive Pricing and Flexible Payment Options
We offer competitive pricing without compromising on quality. Our pricing is transparent and includes all necessary repairs and parts. We also provide flexible payment options to suit your financial needs.
Repair Type |
Estimated Cost |
iPhone Screen Repair |
$150-$250 |
Laptop Keyboard Replacement |
$100-$150 |
Desktop Computer Diagnostics |
$50-$100 |
For an accurate quote, please contact us with the details of your repair needs.
Reputation and Customer Testimonials: The Power of Word-of-Mouth
Reputation is paramount for any trustworthy repair shop. Positive customer testimonials are a testament to the shop’s expertise, reliability, and overall service. Consider reading online reviews on platforms like Google My Business, Yelp, and Trustpilot.
The Magic of Word-of-Mouth
Satisfied customers are more likely to spread the word about their positive experiences, leading to valuable referrals and glowing recommendations. Encourage customers to share their experiences and testimonials.
Listen to the Feedback
Pay attention to customer feedback, whether positive or negative. Address any concerns promptly and use them as opportunities for improvement.
Acknowledge and Appreciate
Show gratitude for customer testimonials by acknowledging them publicly or offering small gestures of appreciation.
Build a Community
Engage with customers on social media, share repair tips, and foster a sense of community.
Monitor Your Online Presence
Keep track of your online reputation by regularly checking reviews and responding appropriately.
Case Study: Repair Hero
Repair Hero, known for its exceptional customer testimonials, maintains a 4.9-star rating on Google My Business. Customers praise their prompt service, reasonable pricing, and professional technicians.
Review |
Customer |
“Fast, efficient, and fair prices. Highly recommend!” |
Sarah J. |
“Fixed my laptop in a day, great service!” |
John D. |
Specialization and Experience: Matching Expertise to Vehicle Needs
When selecting a repair shop, it’s crucial to consider specialization and experience. Not all shops are equipped to handle all types of vehicles and repairs. Identifying the specific needs of your vehicle will help you narrow down your options.
8. Technical Capabilities and Advanced Equipment
Advanced diagnostics and repair techniques require specialized equipment and skilled technicians. Consider the following factors:
- OBD-II Scanners: Essential for diagnosing engine and electronic issues.
- Computer Diagnostics: Used to check for faults in electronic control modules.
- Specialized Tools: Some repairs require unique tools designed for specific models or makes.
A shop with access to the latest technology and experienced technicians can provide accurate diagnoses and efficient repairs.
Tool or Equipment |
Usage |
OBD-II Scanner |
Diagnostic engine and electronic issues |
Computer Diagnostic System |
Check faults in electronic modules |
Suspension Alignment Rack |
Adjust vehicle alignment |
Tire Balancing Machine |
Balance tires for smoother handling |
Brake Lathe |
Machine brake rotors to restore smoothness |
Competitive Pricing and Accurate Estimates: Budget-Conscious Repairs
Finding a repair shop that offers competitive pricing while providing accurate estimates is crucial for budget-conscious individuals. Here are a few tips to keep in mind:
Verify Hourly Rates and Labor Costs
Compare the hourly rates charged by different shops and ask about any additional labor costs associated with the repair.
Obtain Written Estimates
Always request written estimates that clearly outline the cost of parts, labor, and any other fees.
Negotiate Payment Plans
For larger repairs, inquire about the possibility of payment plans to spread out the cost.
Consider OEM vs. Aftermarket Parts
OEM (original equipment manufacturer) parts are typically more expensive but offer better reliability. Explore aftermarket parts as a cost-effective alternative while ensuring quality.
Seek Discounts and Promotions
Regularly check for online discounts, coupons, and loyalty programs offered by repair shops.
Compare Multiple Quotes
Obtain quotes from several shops before making a decision to ensure you’re getting the best value.
Emphasize Transparency and Communication
Choose shops that prioritize transparency and provide clear explanations of the repairs and estimated costs.
Consider Reputation and Reviews
Read online reviews and ask for recommendations to find shops with a positive reputation for fair pricing and accurate estimates.
Understand Warranty Coverage
Inquire about the warranties offered on repairs and ensure that they align with your expectations.
Best Repair Shops Near Me: A Comprehensive Guide
When it comes to finding a reliable and trustworthy repair shop, it’s essential to consider various factors. Here is a comprehensive guide to help you identify the best repair shops near you:
Expertise and Experience: Look for shops that specialize in your specific type of repair. Check their credentials, certifications, and years of experience in the field.
Reputation and Customer Reviews: Read online reviews and testimonials from previous customers. Positive feedback indicates a shop with a proven track record of quality work and customer satisfaction.
Convenience and Accessibility: Consider the location, hours of operation, and accessibility of the repair shop. Choose a shop that is easy to reach and accommodates your schedule.
Transparency and Communication: Seek shops that provide clear communication and transparent pricing. They should explain repair issues thoroughly and provide detailed estimates before commencing work.
Warranty and Guarantees: Look for shops that offer warranties or guarantees on their repairs. This ensures peace of mind and protects you from any future issues with the repaired item.
People Also Ask About Best Repair Shops Near Me
What is the typical cost of a repair service?
Repair costs vary depending on the type and complexity of the issue. Get quotes from multiple shops to compare pricing and identify the most reasonable option.
How can I find a repair shop that specializes in a specific type of repair?
Use online search engines or directories to filter results based on your specific repair needs. Read reviews and check credentials to ensure the shop has expertise in that particular area.
What are the signs of a reputable repair shop?
Positive customer reviews, clear communication, transparent pricing, expertise and experience, and a willingness to provide warranties or guarantees are all indications of a reputable repair shop.